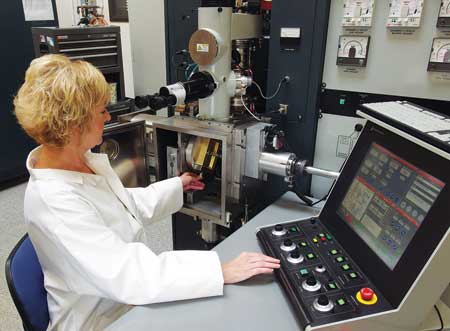
An EBE engineer operates the electron beam welder, which is used to attach rods with end-bearings, creating a precise weld designed to withstand the pressures and debris of air travel.
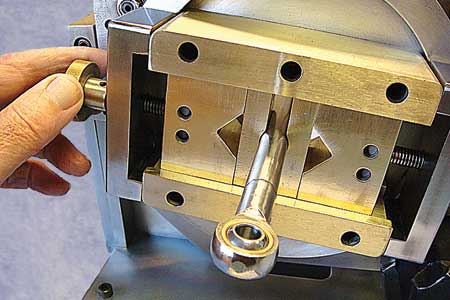
"Big Mouth," the electron beam welding machine used by EBE Inc. to weld link assemblies for airplane engines. Half of one of the smaller diameter assemblies can be seen protruding from the tooling ready for welding while the other half is inside an extension tube attached to the side of the vacuum chamber.

A rod and end-bearing prior to welding.
Electron Beam Engineering (EBE) provides precision electron beam and laser beam welding services, and specializes in working with complex components and precision assemblies. An aerospace parts manufacturer approached EBE with a request to electron beam weld a variety of link assemblies that, when mass-produced, would be used in the General Electric and Pratt & Whitney engines for civilian and military aircraft across the nation.
The assembly is made of Inconel 718, a nickel-chromium-based superalloy designed for strength and heat resistance. The assembly includes two end-bearings, one on each end of a hollow tube (tube is used instead of rod for weight reduction). The rod-end-bearings ultimately get fitted with balls that act as bearings that are used to support the engine. They provide flexibility to allow the high speed rotating engine some movement and isolation from the aircraft frame.
The welds joining the tube and the end-bearings together are critical for an aircraft engine due to the stresses on the engine, extreme temperatures and exposure to the elements. It is equally critical that there be no welding splatter inside the closed tube that could come loose and cause erosion of the tube; fortunately X-ray inspection, which occurs on completion of the welding will detect this splatter should it occur. "The stresses and environment are especially great in military aircraft and require that at routine intervals the links be replaced with new ones," said Richard Trillwood, Founder and President of EBE.
When the project was brought to EBE, Trillwood said there were issues with the previous conventional gas tungsten arc welding (GTAW) or TIG welding processes. They required a more invasive handling of the Inconel tube so as to provide Argon shielding gas to the top and root of the weld. Typically, holes would have to be drilled through the tubes at each end to allow the flow of Argon purge gas. These holes would then have to be welded shut, which introduced two additional welding operations not necessary when using electron beam welding.
"An advantage of using electron beam welding on this part is minimized heat input and distortion," said a company spokesperson. "In addition, the vacuum inside the tube (a byproduct of welding a sealed component in a vacuum chamber) reduces the problems of oxidation and stress during the subsequent vacuum heat treatment, which is performed to optimize the material strength and remove residual stresses."
Because these were critical components, added precautions were taken by EBE. The weld profile has a minimum width requirement that allows for a few thousandths of an inch misplacement of the weld position, which will occur as a result of machining tolerances and tooling wear during volume production. Before every welding batch, a first article test sample that simulates the actual joint is electron beam welded. Its position is optically checked, and then it is sectioned to confirm the correct weld profile, lack of visible defects such as absence of weld splatter inside the tube. Every production component also undergoes visual and positional inspection of the weld, which is logged by the operator as part of the production data collection. To complete the process, the parts are vacuum heat treated and X-rayed as a final quality assurance.
"What they are looking for are smooth welds, top to bottom, so as not to create stress points - and the absence of weld splatter that gives a clean, sealed tube inside," said Trillwood.
The rod-end-bearings at each end of the rod are set at different angles to each other so as to align with the support at one end and the engine at the other end. This very precise angle and the overall length between the centers of the bearings is difficult to maintain because of the shrinkage which occurs during welding. To mitigate this one of the rod-end-bearings is left for finish machining after the welding has been completed to ensure perfect angular and linear alignment of each bearing.
The machine and the tooling used for this project were all designed and made by EBE. The machine is named a 312 BEAMER, an electron beam welder operating at 3 kW maximum power and fitted with a 12" cube stainless steel chamber with one extension tube. Special tooling included:
- A weld-tacking fixture to ensure alignment orientation and intimate contact of the joint
- A special rotator, later named "Bigmouth," which accommodates the large rod-end of some links and rotates the assembly in the vacuum chamber
- An optical measuring tool specially designed and built to check the position of the weld joint and then check the centerline of the weld to ensure that the weld was centered on the joint.
All of the EBE machines are fully upgraded to current standards for power supplies, optics and vacuum systems. Additionally, EBE's machines can store all the weld parameters and log all the data on every weld in production. None of this requires operator participation. The machine operating data, including vacuum levels, are automatically recorded every few milliseconds. The data can be stored internally or on a dedicated server and shared within the company or, if permitted, shared outside of EBE for analysis.
EBE provides precision electron beam and laser beam welding services throughout the United States and Europe, and provides sample welds for companies wanting to evaluate the EBW and LBW processes on their assemblies. It specializes in working with companies designing or producing complex components for a variety of applications, including aerospace and defense, medical devices, oil and gas exploration, sensors, automotive and transportation products, satellite communications, electronics, jewelry, semi-conductors and commercial uses such as race cars.
EBE was founded in 1991 by Richard Trillwood, the designer of the world's first compact production electron beam welding machine. EBE's quality and welding processes are AS9100, ISO and National Aerospace and Defense Contractors Accreditation Program (Nadcap) certified, quality systems required by many major aerospace and medical companies.
For more information contact:
Richard Trillwood, CEO
Electron Beam Engineering, Inc
1425 South Allec Street
Anaheim, CA 92805
714-491-5990
richard@ebeinc.com
www.ebeinc.com