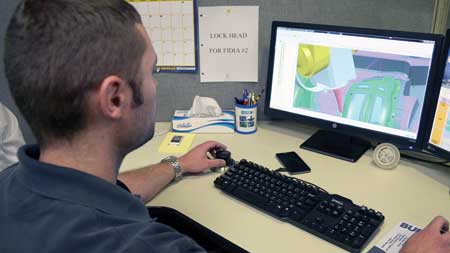
Paragon now uses PowerMILL to program all of its machining. Standardizing on PowerMILL allows Paragon to move programmers between departments.
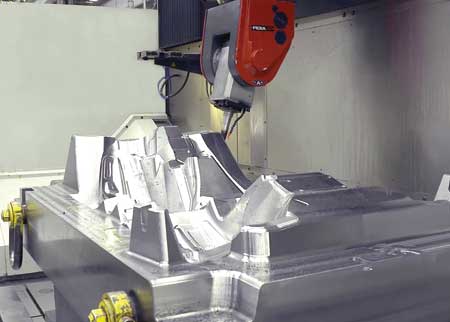
Paragon produces very large tooling and components.
"We are seeing jobs coming in days ahead of schedule," said Paragon D&E Manufacturing Engineer Brian Kerkstra. "We are seeing jobs that would traditionally have taken us 10 weeks being completed in four or five weeks." This has been the result of standardizing on Delcam's PowerMILL CAM software for all of its machining, which has proved a key component of Paragon's "Power to Change" philosophy.
"Our 'Power to Change' philosophy is about our team working together to develop methods to do things more efficiently. It is about getting people involved and really trusting in their decisions," explained Paragon President David Muir. "We are actually envisioning what Paragon could look like in a year from now. Before we had PowerMILL, this was a five-year plan for Paragon - we are accelerating our plans by using Delcam as a sole software provider."
Paragon, which is based in Grand Rapids, MI, is best known for producing very large and very accurate tooling and components. The company serves a variety of industries, including automotive, heavy truck, oil and gas, aerospace, defense, marine and nuclear. "We have a lot of big equipment," said Andrew Samrick, Vice President of Manufacturing. "Our customers are frequently looking for machining capabilities for large, high quality, high tolerance components, as well as fast delivery."
The culture of Paragon, when it comes to product development, has really come from the relationships the company has with its customers. "We ask our customers what innovations they need, and they use us as problem solvers for their product development," said Muir.
Diversity has been an important part of the company's success. "A big advantage that Paragon has is that we are able to cross-pollinate ideas from different projects," said Muir. "What we learn in one industry, like aerospace, we are able to apply in injection molding or vice versa, or in compression tooling or even now in hydro-form tooling."
In contrast, a diverse range of programming software used to be a major problem. "We had too many software programs on the machine floor," remembered Muir. "That problem was driving a lot of inefficiencies with our training and with the ability for our staff to move from one station to another. We explored the idea of looking for only one software program across the whole shop. We looked through all of the available software and we decided on Delcam."
The decision was not only about the strength of the software. "Delcam brought us a willingness to listen to what our company needed and what our users needed," stated Muir. "Most of the competitors told us 'This is how it is going to be' but Delcam said 'What can we do to make your business more profitable?' We needed more customized input and, instead of being the traditional software vendor that pushed back and tried to shoe-horn us into its product, Delcam gave us direct access to the development team."
"Delcam provided regular training onsite. We were able to move from zero knowledge to a better cost performance in less than six months," added Samrick.
"Our customers have been telling us that, because of the way we can move now, we are doing things that no one else can do for them," he continued. "We have got some great 'mad scientists' who can think up these incredible things. PowerMILL has helped us to take their focus off of the day-to-day issues and to begin to look forward. The type of equipment that we build is among the largest of its kind, but that is simply a stepping-stone towards being able to build more custom solutions for specific customer needs. Delcam allows us to take care of our customers and to make money at the same time."
One area where Paragon needed extra support was dynamic machining control for the company's large 5-axis machines. Paragon staff worked with Delcam developers to create the integrated mechanism for optimizing 5-axis positioning in the 2014 R2 release of PowerMILL.
One of the main drivers for the change in technology at Paragon was the availability of skilled labor. "There is a shortage of labor out there right now, especially of skilled machinists," explained Muir. "That shortage means that we need to find technology that takes the labor that we have and applies it across more machining time."
To tackle the problem, in 2013 Paragon decided to start a training program within the company called Paragon Technical University (PTU). Dean of PTU, Larry Oppenhuizen, explained, "This program allows us to put our apprentices on the right path for the right career choice. We have 26 of them currently and they are all learning PowerMILL.
"Now that we are using the same software throughout the plant, an apprentice that is learning PowerMILL in, for example, the small machine department, can go over to another department more quickly because he already has Delcam knowledge. It makes it easy for us to give our apprentices a good rounded education because they only need to learn one set of software."
Established in 1959, Paragon designs and manufactures prototype to production tooling in aluminum, steel, Invar and composites for simple to complex aerospace parts. Paragon also machines and CMM inspects composite and metal parts including titanium and Inconel. With 50+ ton crane capacity and machines from 1' to 52' in length, Paragon is equipped to handle large and small projects.
For more information contact:
Paragon D&E
5225 33rd St. SE
Grand Rapids, MI 49512
616-949-2220
www.paragonde.com
Delcam
877-335-2261
marketing@delcam.com
www.delcam.com