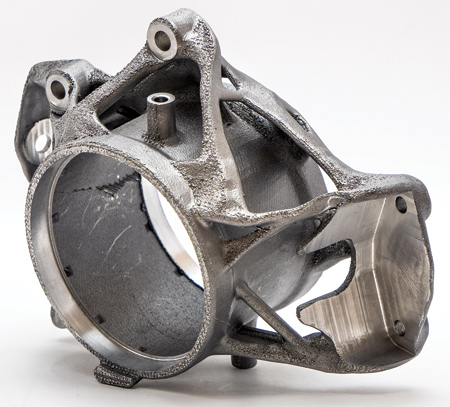
Printed wheel carrier, before finishing
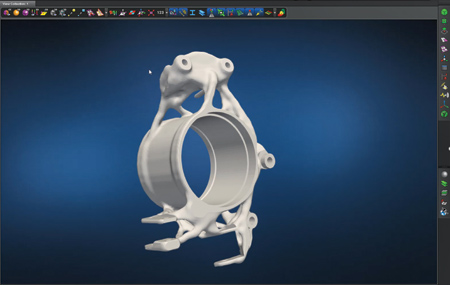
Generative design of a wheel carrier
MSC Software Corporation offers the MSC Apex Generative Design, a new design optimization solution designed to improve quality through automation of the design processes with embedded manufacturing knowledge.
"MSC Apex Generative Design aims to improve productivity by up to 80% compared to classic topology optimization," said a company spokesperson. "The software produces a part design that is ready for additive manufacturing (AM) within a few hours-a fraction of time usually required-making reliable AM more cost efficient and accessible."
In MSC Apex Generative Design, the designer only needs to specify the boundary conditions and design objective. Multiple lightweight design candidates that explore the possibilities of the design space will be produced that provide optimal stress distribution and minimize weight. This enhances the creative process, so designers have more time to optimize the product's concept and integrate additional features that add value. "The software's intelligent smoothing technology ensures that every candidate has an enhanced finish that is ready for print," said the spokesperson.
"New design freedoms in AM require a new generation of software solutions that take full advantage of the new AM possibilities. We make the generative design process smarter by producing design candidates that both satisfy the engineering criteria and look as the designer intended when 3D printed," said Dr. Thomas Reiher, Director of Generative Design.
"Conventional topology optimization workflows require manual work and multiple tools to achieve production-ready results, which can lead to information loss as data is converted," said the spokesperson. "MSC Apex integrates all relevant steps within one computer aided engineering (CAE) environment to improve productivity with a single user experience, from design to AM preparation."
The design process is workflow-oriented, providing easy and fast model set-up from existing geometries or mesh in common CAD, STL or MSC Nastran BDF formats. Designers can find optimized design candidates and perform design validation within the same CAE environment, simplifying the work process and reducing design iterations. The result is a fully integrated, automated optimization process in which compatibility for previous and subsequent operations plays a vital role. This capability implies the conversion from the CAE mesh to CAD with no manual reconstruction of geometry, simplifying the work process for designers.
The MSC Apex Generative Design for AM solution combines print-ready geometries with robust metal (Simufact) and polymer (Digimat) build process simulation from Hexagon's AM portfolio. Designers only generate part designs that can be successfully manufactured using their chosen material and print process to eliminate costly prototyping.
"AM promises innovation and manufacturing productivity advances. But to truly transform, the new technologies require automated design workflows with embedded process knowledge. We are integrating our structural analysis, design optimization and manufacturing simulation solutions to optimize and validate designs for additive processes before a single part is printed," said Hugues Jeancolas, VP Product Management.
MSC Software is part of Hexagon's Manufacturing Intelligence division.
For more information contact:
MSC Software
4675 MacArthur Court
Newport Beach, CA 92660
714-540-8900
info-msc@mscsoftware.com
www.mscsoftware.com