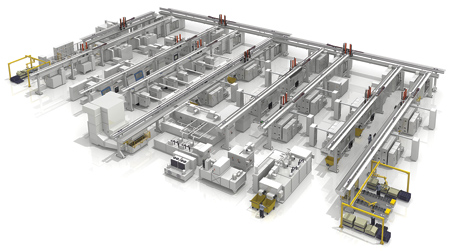
Production plant for four-cylinder crankshafts in "herringbone" layout planned and supplied by BOEHRINGER as a turnkey project
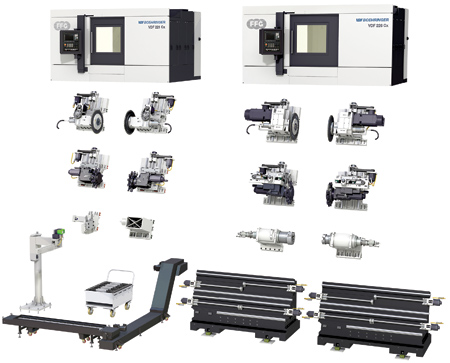
Modular construction kit for lathes and special machines for crankshaft and camshaft machining
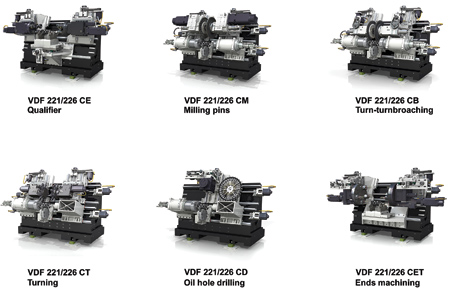
Machine designs for the individual machining sections of shaft machining (shaft diameter max. 290 mm, VDF 221 workpiece length 550 mm and VDF 226 workpiece length 750 mm)
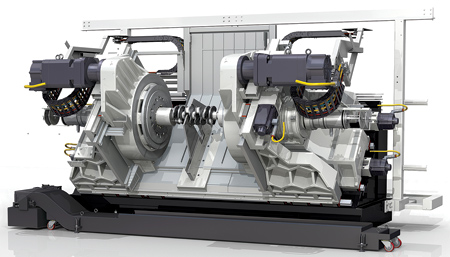
Turning/milling machine for axially parallel machining of main and pin bearings as well as the ends by pendulum stroke feed of the internal milling units BOEHRINGER VDF 221 CIM - Innovative gantry design
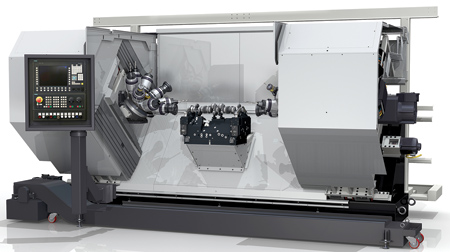
BOEHRINGER VDF 221 CET end machining machine for shaft components with highly dynamic cone turret, 8 spindles each
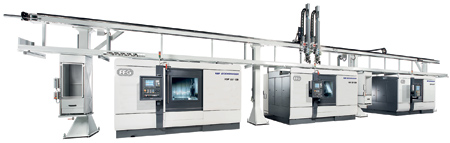
Integration of shaft machining machines into a production system in line setup with a portal load from MAG Factory Automation
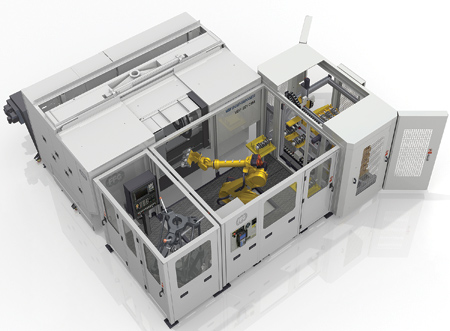
Expansion of the shaft machining machines by a "MAG Cell" with automated workpiece measurement and material supply by pallets
The demand for combustion engine will last for a few more years until the transformation of automotive companies and markets to alternative drive systems is completed. For quite some time now, we have been experiencing the consequences that ambiguous strategies among manufacturers, technologies and, above all, politics have had on mobility customers. In addition to significant developments in exhaust gas purification and synthetic fuels, the so-called "e-fuels," other functions of the engine are also considered. Until drive technology is completely replaced, the focus will continue to be on productivity, quality and costs, as well as state-of-the-art production technology for crankshafts.
The internal combustion engine will be indispensable in the coming years and, as a singular drive system, it will undergo further development as part of hybridization in vehicles. The disruption is in progress and the unknown variables include the timeline and the production volume to a possible compensation by the drive alternatives.
For production planning, this scenario initially means a maximum degree of flexibility with regard to product design and plant capacity. In the phase of uncertainty, new plant purchases are delayed and demands for reconfiguration of existing equipment increase whereas investments are available for individual process steps.
BOEHRINGER offers compatible solution and implementation for all upcoming project specifications, including: procurement of new production lines, expansion or modification of existing plants, as well as reconfiguration of existing systems.
The new BOEHRINGER 221/226 series can be easily integrated into any layout and connected to automation. All conceivable parameters of the specification for crankshafts and shaft machining can be carried out through small installation footprint, higher performance of the components, higher machining accuracy and lower consumption data with high flexibility for the required technology. The new shaft machines are developed from a modular system of which lathes, end machining machines for shaft components and special crankshaft machines are configured. On a slanted mineral casting (polymer concrete) bed, all guideways and carriage drives are arranged in one level. This concept achieves maximum possible stability and damping and reduces thermal influences to a minimum, and the compact size of the components avoids unfavorable cantilevers, resulting in low-vibration machining. The modern vehicle engines are getting smaller yet higher performance with optimal smoothness. For crankshafts of passenger cars, this specification means lower friction due to smaller bearings, mass reduction and higher material stability. In terms of machining, this means higher cutting performance for small and thus unstable workpieces. The guideways and carriage drives as well as the modular system are designed for these parameters under higher drive power of the milling units.
Two alternatives are available for the paraxial mill-turn process: internal milling (tool ring with internal cutting edges) and external milling (tool disc with external cutting edges). The choice of technology in the peripheral areas can be determined analytically: external milling is ideal for small shafts whereas internal milling for large shafts. In between, there is a grey area that is a controversial subject discussed among process specialists. In order to serve the market completely-with the exception of machining on a stationary workpiece (whirling)-the product range was expanded by BOEHRINGER VDF 221/226 CIM. Internal milling is traditionally used for roughing.
With the technology innovation of hard fine internal milling of crankshaft bearing positions, an alternative is available for the first time that replaces the costly roughing after hardening and offers significant savings in procurement. With the innovative portal design of the VDF BOEHRINGER VDF 221 CIM for internal milling of crankshaft stroke and center bearings as well as for cheek machining, a very robust machine is available that enables vibration-free, heavy-duty machining with maximum performance. External milling on the VDF 221 CM has successfully implemented the fine machining of shafts after hardening with hard fine milling.
The significant advantage of this technology lies in:
- Lower procurement costs for machine equipment (-25% compared to grinding)
- Can be dry-machined and therefore no maintenance and disposal of grinding abrasive (oil or emulsion) required
- Environmentally conscious with lower energy consumption
- Cost efficiency.
As a development partner for hard fine internal milling, Ingersoll supports us in technology optimization. The new VDF 221 CIM offers the following technical features in heavy and/or precise machining of difficult workpieces:
- Milling units mounted on portal slides with central headstocks and thus ensure maximum system rigidity compared to competitors
- Temperature-controlled spindle head with generous bearing dimensions as known by VDF BOEHRINGER
- Powerful milling drives with recirculating oil lubrication and temperature control
- Temperature compensation in the working area
- System support NC programming
- Excellent access to all assemblies due to wide opening housing on both sides
- Cutting force control for an optimum machining process.
The new development of the CNC end processing machine BOEHRINGER VDF 221/226 CET is the consistent continuation of the process improvement to increase productivity by the specialist of crankshaft and shaft machining. The core components of this new 6-axis machining center are the two crown turrets, each with eight tool interfaces, which work as 3-axis units at the both ends of the stationary (firmly clamped) workpiece. Alternatively, spindle and multi-spindle heads in special designs can be flanged to the carrier units for specific applications. The main technical features of the components used are as follows:
- Maximum robustness and performance, especially in milling applications
- Design with minimal lubrication technology (MMS) or wet machining possible
- Various toolholders available (standard HSK)
- Compact unit with less cantilever and stable spindle
- Direct drive with max. 15,000 RPM
- Chip-to-chip time < 1.5 s.
Compared with other known units for end machining scores the crown turret with the direct power flow of the feed unit on the turret drive and the respective spindle in machining position with correspondingly higher power (40 kW) and powerful feed (10 kN).
The machining unit is carried by stable portal slide (gantry carriage) in Z direction, on which the cross slide positions the turret highly dynamically in X and Y directions. In the compact design of the VDF 221 CET, workpieces with a maximum length of 650 mm (up to 280 kg) can be loaded and the long version VDF 226 CET accommodates shafts up to 3,000 mm (1,400 kg) for machining. The machine can be loaded manually with a lifting device, fully automatically from the front by a robot or from the top by a loading gantry.
The modular VDF BOEHRINGER construction kit makes a decisive contribution to high quality and reduces the storage costs of spare and wear parts when installing a complete production line through the common parts strategy, and therefore providing attractive pricing.
Prominent advantages of the machine concepts:
- Slanted machine bed
- Arrangement of all components on this inclined bed level
- Optimal chip removal in the machine, especially with dry and MQL processing
- Wide opening housing allows free and ground level access to all modules
- Compact, space-saving machine layout with central electrical and fluid cabinets
- High energy efficiency and broad experience in environmentally conscious manufacturing technologies
- Workpiece flexibility due to large working area in X and Y directions.
All the machines of the VDF series are highly ergonomically designed; they can be loaded manually and automatically. A wide opening of the working area supports the positioning of the components and provides convenient access to the workpiece holder during loading and unloading, even with a hoist. The swiveling control panel of the machine is adjustable to the operator's need. In most cases, automatic loading takes place from above with a loading gantry or from the front with a robot. The standardized MAG Cell can be connected to the machine as a production cell. Inside there is a floor mounted robot, which removes components from a storage tower or from a belt feeder and delivers the finished parts in the same way. The MAG Cell can be expanded with further functions such as cleaning and/or measuring. MAG Factory Automation plans to integrate machines in the production environment from stand-alone machine with loading to the complex turn-key system for the production of ready-to-install components.
Processes and layouts are simulated and optimized using state-of-the-art planning tools. Thus, regardless of new machines, used machines or a mix of both in one system, the required plant output and quality can be planned bindingly in the quotation phase. The combination of parallel (redundant) stations and the bottleneck areas (sequential stations) must be managed and a maximum productivity must be achieved in logistics planning. In terms of turn-key projects, for example, cutting machines with measuring, washing and assembling can be connected via an automated transport system. Furthermore, the respective processes can be validated with Digital Twins, station availability can be determined and simulating the material flow variants a Digital Production Twin can be created. During project implementation, these models are further refined and through virtual commissioning to guarantee a higher level of quality as well as a noticeable reduction in delivery times. With the virtual shadows of the system components, the numerous modifications over the service life can be planned much more easily and implemented in the shortest possible time by anticipating a virtual commissioning at the Twins in production. Additional advantages of the digitization include operator and maintenance training as well as remote services.
Until combustion engines are completely replaced, highly productive plants will continue to manufacture the components. However, with respect to the transformation of alternative drive concepts, using the robust and durable BOEHRINGER machine for virtual planning of future application is already possible today. The BOEHRINGER VDF series is ideally equipped to meet the high and growing quality requirements of drive shafts for electric drives.
Authored by Dr. Manfred Berger, Business Development, FFG Europe & Americas GmbH, and Andreas Schweizer, Development Manager, BOEHRINGER, MAG IAS GmbH
For more information contact:
MAG Automotive LLC
6015 Center Drive
Sterling Heights, MI 48312
586-446-7000
Sales-NA@mag-ias.com
www.mag-ias.com