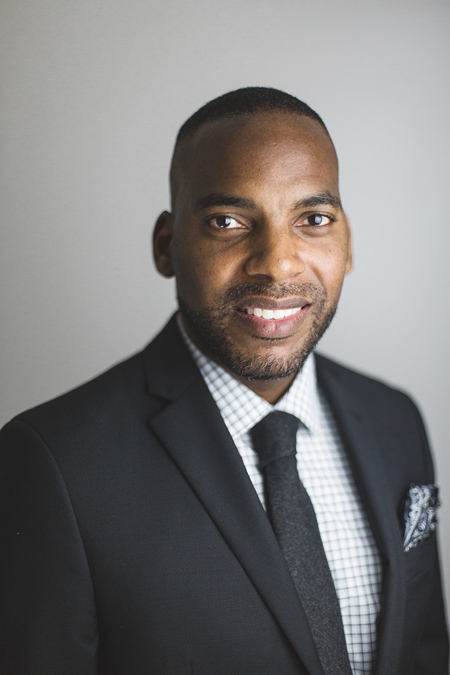
Montez King, Executive Director, NIMS
Mention the skills gap in manufacturing to most anyone in the industry, and it is bound to be met with a sigh and a shrug. The issue is well known and daunting for sure. The positive news: training programs at community colleges are well supported in certain regions, grassroots efforts are effecting change and government-funded apprenticeship programs are making headlines. "Still, we at NIMS have come to realize after visiting hundreds of manufacturers and listening to their needs, that there is not only a skills gap, there is a significant training gap," said Montez King, Executive Director, NIMS. "A majority of the current training programs that lead to an industry-recognized credential are often described as too rigid, too long, too expensive, and the projects involved in validating employee skills have little resemblance to a company's actual production requirements."
These conventional training programs focus on the "journeyman" occupational model, which is all-encompassing and often includes pages of work standards that are often unnecessary for a specific role in modern manufacturing environments. While the all-around-the-shop master is to be praised, and anyone would be crazy not to hire him or her, that is not exactly what manufacturers need when discussing their immediate and specific needs. What they want is a modular, portable set of skills aligned with specific roles and duties that can evolve and grow as job responsibilities become more complex.
The prevailing driver of this change in human resource needs is the velocity of new technology adoption at manufacturing companies. As production methodologies have advanced, that gap between traditional metalworking skills training and the automation revolution-physical and digital-has widened considerably.
In keeping with that growth and change in needs, we at NIMS are advancing our training and validation methods. Our credentials remain the same, for example, we have industry certified credentials for CNC milling, CNC turning, EDM, CAM programming and many more. The most significant change are the projects used in the training and testing process. They can now be more akin to a company's own parts. This change is a vast improvement for employers. For instance, an aerospace subcontractor likely has extremely tight tolerance requirements in tough materials. A mold and die shop might want finishing operations to be a focus. An oil and gas manufacturer may have proprietary threading and hole making processes. Therefore, the projects and validation requirements can now adjust for each employer's particular needs as long as the core, nationally recognized standards are met. Before, the projects were more generic to teach and test certain skills. For schools, that non-specific workpiece is okay, but even our educational institution customers are appreciating the new flexibility surrounding projects, as they need to meet the industry training demands in their local communities.
A fundamental aspect of the new, more flexible approach is the concept of Performance Measures (PMs) for the NIMS validation process. These give a much clearer assessment of how well someone is trained. PMs translate job descriptions and competencies into practical experiences that reflect what employees will, or do, face on the job. Each PM includes six metrics, providing a method to systematically develop and implement a program to measure and track performance. PMs are made up of a specific set of deliverables, including a performance agreement, a specific hands-on project, a delivery system defining its requirements, a data collection piece and an end report synthesizing the PM data. Ultimately, PMs allow companies and schools to benchmark internally and externally, visually identifying skill strengths and opportunities for improvement using the NIMS' digital tool.
For a real world example of this method pertaining to CAM Mill Level 1, visit nims-skills.org/resources/prints-and-cars/893.
In today's manufacturing environment, an employer needs-perhaps above all else-critical thinking skills. Manufacturers need people who can pull from their repository of competencies and knowledge to solve a problem or initiate a smart new way of doing something, rather than merely demonstrating learned behavior from occupational training and a task validation checklist. The PMs go beyond what a person knows and instead take a comprehensive look at what the person can apply on the job.
In addition to developing a more relevant way to train, validate and credential people for today's roles in manufacturing, NIMS is also reconstructing its digital platform. Much like data-driven manufacturing, we are now able to use rich data to grasp much more than before. In the past, a candidate would either pass or fail an exam. Now, we-and employers-can ascertain where a person shines and where he or she needs improvement and address that in future training. This is highly valuable information and allows the employer to better understand an employee's skill set, and thereby place the person where he or she will succeed and grow.
"The team at NIMS welcomes learning about the skills needed at your company," said King. "I am confident we can devise a flexible and effective solution for you. The process will take less of your time than you might imagine, and ultimately it will reduce the time and money you spend hiring, firing, and dealing with scrap parts."
Authored by Montez King, Executive Director, NIMS
For more information contact:
NIMS
10565 Fairfax Blvd., Suite 10
Fairfax, VA 22030
703-352-4971
support@nims-skills.org
www.nims-skills.org