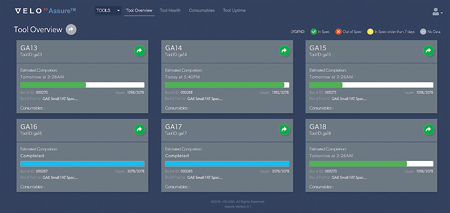
VELO3D's Assure quality control dashboard enables engineers to track the quality and progress of Sapphire machines in real time.
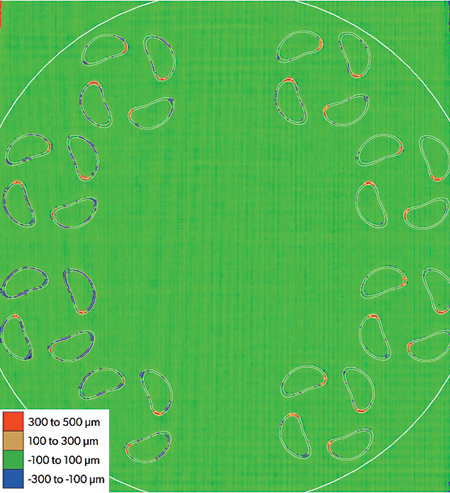
Assure provides true Z-height quantitative powder bed and part metrology. Note the sections of parts with red lobes indicating metal protruding >300um above the powder bed but still below control limits.
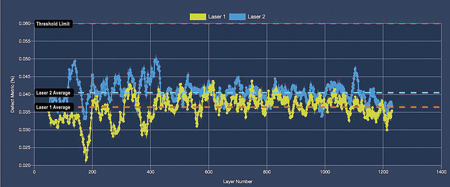
Assure predicts defectivity as a function of layer number. An increase in the defectivity metric is correlated with increasing defectivity in the bulk core of the part.
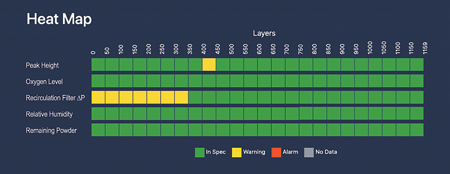
Before and during a build, Assure validates that critical parameters stay within control limits, helping ensure high quality parts. Clicking on individual squares reveals details on the underlying event.
VELO3D, an innovator in metal additive manufacturing (AM) has announced the release and availability of the VELO3D Assure Quality Assurance and Control System for its Sapphire 3D metal printers. Stratasys Direct Manufacturing, a subsidiary of Stratasys, Ltd. and one of the largest providers of additive (3D printing) and conventional manufacturing services in North America, is the first customer to implement Assure.
Assure provides substantiation of part quality needed for volume production. It detects process anomalies, flags them and highlights the corrective actions required so errors are not repeated. Through real-time, multi-sensor, physics-based detection algorithms, Assure offers high traceability of part quality and flags process anomalies as soon as they occur. This decreases variation and provides comprehensive documentation to fast-track printed part validation.
"Assure is a revolutionary quality-control system, an inherent part of the VELO3D end-to-end manufacturing solution for serial production," said Benny Buller, founder and CEO of VELO3D. "Assure is part of our vision to provide an integrated solution to produce parts by AM with successful outcomes."
Stratasys Direct began working with VELO3D on Assure testing soon after it acquired a Sapphire printer. Stratasys Direct implemented Assure to identify variations and anomalies in the production of the parts on several builds. Throughout the study, Stratasys Direct accessed Assure's dashboard and sophisticated algorithms to monitor the integrity of the builds, validate the bulk material density, observe ongoing process metrics and verify the calibration of the system across multiple production runs. These trials and results confirmed the capabilities of the software, and were documented in a whitepaper that both VELO3D and Stratasys Direct co-authored.
"Stratasys Direct has built a culture of continuous improvement that means we are continually setting new standards for our industry on quality," said Kent Firestone, CEO of Stratasys Direct Manufacturing. "We integrated Assure into our quality control workflow because it produces highly actionable insights. The user interface features intuitive graphs and charts that enable us to see and interpret the vast amount of data collected during builds. This information helps our engineers verify the quality of the build each step of the way, and enables them to make quick decisions in the event of an issue. Assure helps us reduce production variation, improve yields and circumvent anomalies to ensure consistent additive manufacturing."
For more information contact:
VELO3D
511 Division St.
Campbell, CA 95008
408-610-3915
www.velo3D.com