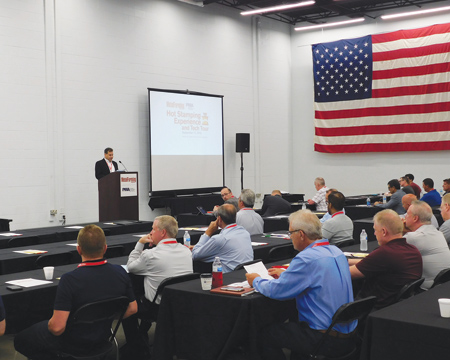
Over 70 industry leaders and practitioners attended the conference held in the Design Center of Urgent Design & Manufacturing.
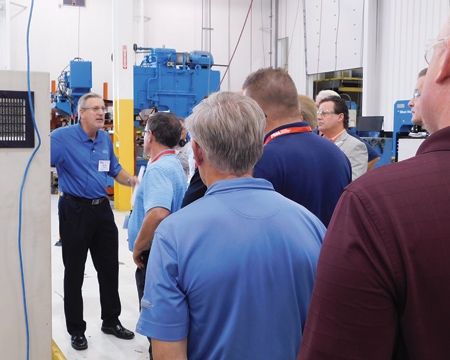
Alan Peterson, President, The 3-Dimensional Services Group leads a guided plant tour of Urgent Design & Manufacturing.
The 3-Dimensional Services Group, a manufacturer of production-intent prototypes and low-volume production, and its affiliate Urgent Design & Manufacturing, hosted a one-day conference devoted to understanding the manufacturing technology behind hot stamping. The conference was organized by the Precision Metalforming Association (PMA) and its sponsors, APT, Hitachi and Weld Systems Integrators. The all-day forum, titled "Hot Stamping Experience and Tech Tour," was held at the Urgent Design & Manufacturing Design Center and its manufacturing facility.
Over 70 registrants and sponsors attended the event. The keynote speaker was Eren Billur, Owner of Billur Metal Form, who presented the Fundamentals and Applications of Hot-Stamping Technology for Producing Automotive Parts. Other speakers included: Harald Lemke, Chief Commercial Officer, Formetrix, who addressed Novel Cost-Efficient 3D Printed Hot and Cold Forming Tools for High Volume Production; Mike Austin, Director-Manufacturing Engineering, Diversified Tooling Group, who spoke on Hot-Stamping Developments and Optimization; Nathan Harris, Industry Management-Automotive, Trumpf, Inc. on Laser Cutting Hardened Steel; and Bob Collins, Senior Applications Engineer, Weld Systems Integrators, Inc. on Welding Fasteners to Hot-Stamped Coated Steels.
Attendees were provided with a guided plant tour of Urgent Design & Manufacturing, showcasing the company's many technologies in fabrication and metalworking such as fiber laser cutting, robotic welding, hydroforming and tube bending. The focus of the tour was on the company's hot-stamping cell and its role in producing complex metal components.
According to Chad Peterson, The 3-Dimensional Services Group General Manager, "The mandate for lighter and stronger components is a game changer. Some component design geometries cannot be cold stamped due to work hardening of the material, strain limitations and increased spring-back. Trying to achieve these components' geometries would require three to four forming operations, and material would work harden to the point that it is not practical or possible. But hot stamping, with blanks or parts in a red-hot state, enables the drawing, with the material's end strength far superior to what cold stamping can provide."
The 3-Dimensional Services Group, headquartered in Rochester Hills, MI, consists of 3-Dimensional Services, Urgent Plastic Services, Urgent Design & Manufacturing, 3-Dimensional Services-Europe and Michigan Integrated Technologies.
For more information contact:
3-Dimensional Services
2547 Product Drive
Rochester Hills, MI 48309
800-959-0804
www.3dimensional.com
Urgent Design & Manufacturing
3142 John Conley Drive
Lapeer, MI 48446
810-245-1300