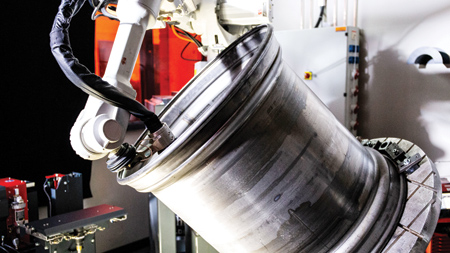
The tandem high-performance welding process ensures that high-volume components and long seams are joined efficiently
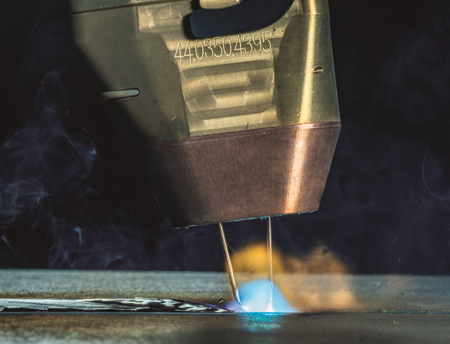
The two wire electrodes are isolated from each other, allowing the arcs to be controlled individually.
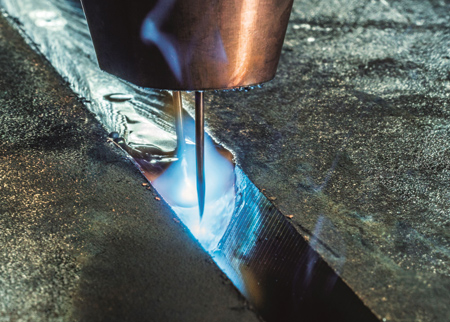
The improved torch cooling system on the TPS/i TWIN Push system extends the service life of the wearing parts.
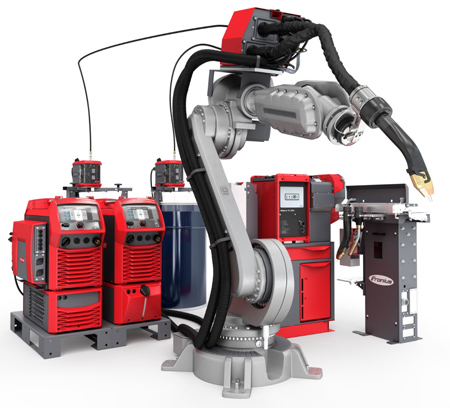
The TPS/i TWIN Push welding system consists of two powerful TPS/i welding systems, the TWIN Controller, a compact wirefeeder, a cooling system, hosepacks and the TWIN welding torch. The new Robacta TSS/i TorchServiceStation torch cleaning station and the TX TWIN welding torch change station complete the system.
Fronius now offers its tandem welding process on the TPS/i welding platform. The TPS/i TWIN Push high performance welding system is designed to be more compact, easier to use and network-capable, and it also integrates enhancements to the welding process. "For users, this means higher deposition rates, higher welding speeds and increased efficiency in production due to the reduced need for pre-fabrication and rework," said a company spokesperson.
High performance welding is characterized by a high deposition rate that permits a high weld seam volume or high welding speeds. This is relevant in particular when joining high-volume components or long seams for construction machinery, commercial vehicles as well as automotive parts and in shipbuilding. "The high processor power of the TPS/i improves the synchronized TWIN Push tandem process: the process is even more stable and reliable, and the enhanced gap-bridging ability saves the user time at the component preparation stage. The amount of rework can also be reduced, since precise control of the welding process enables controlled droplet detachment and low heat input into the component, permitting low-spatter results with minimal distortion," said the spokesperson.
Fronius offers new process and control options with the TPS/i TWIN Push. Pulse Multi Control (PMC) TWIN features a short, focused pulsed arc that enables improved penetration and a higher welding speed. The PulseSync option allows the user to select widely varying travel speeds for the two wire electrodes. This gives the user greater flexibility to ideally adjust the welding parameters to the component and achieve higher welding speeds. The power source will automatically correct all relevant power source parameters, such as the ignition properties, the point of droplet detachment and the pulse ratio. New control mechanisms assist the welder in other ways too - the arc length stabilizer and the penetration stabilizer increase process stability and make it easier to configure parameters. Where the position of the interface varies, possibly due to component distortion or imprecise clamping, automatic seam tracking assists: during welding the welding system transmits a seam tracking signal to the robot so that it can make corrections as required.
The TWIN process is based on tandem welding and features two wire electrodes that are fed into a welding torch with a single gas nozzle but that remain electrically isolated from one another. As a result, the arcs can be controlled independently and, despite differing outputs, can be precisely synchronized and coordinated. In addition to two TPS/i power sources, the TWIN Push system requires a TWIN Controller. The controller synchronizes the welding process and acts as an interface that is compatible with all robot makes. The compact wirefeeder, cooling system, hosepack and TWIN welding torch complete the welding system.
The cooling system for the torch has been improved, extending the service life of wearing parts. Alongside this, Fronius has developed the Robacta TSS/i TorchServiceStation. This welding torch cleaning system combines a number of cleaning methods, including high pressure cleaning, brush cleaning and magnetic cleaning as well as cleaning by means of a cutter. The professional torch cleaning device lowers the overall system costs by extending the service life of wearing parts.
The efficiency of the welding system can be further increased by using the TX TWIN welding torch change station: the console allows for automatic switching between TWIN and Single torch bodies. This means the same system can be used to weld areas that are particularly difficult to access with the more compact Single torch body. The robot automatically changes the torch body - allowing for unmanned shifts.
For more information contact:
Fronius USA LLC
6797 Fronius Drive
Portage, IN 46368
219-734-5500 / 877-FRONIUS
sales.usa@fronius.com
www.fronius.com