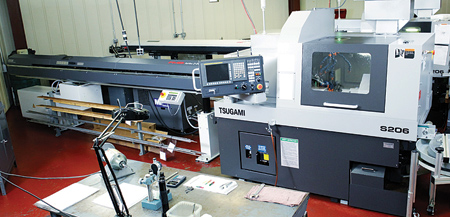
Tsugami S206 6-axis opposed gang tool CNC lathe at Thomas W. Springer
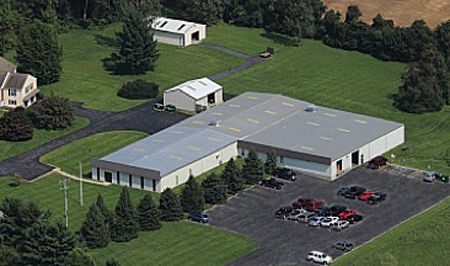
Thomas W. Springer's 20,000 sq. ft. facility located in Landenberg, PA.
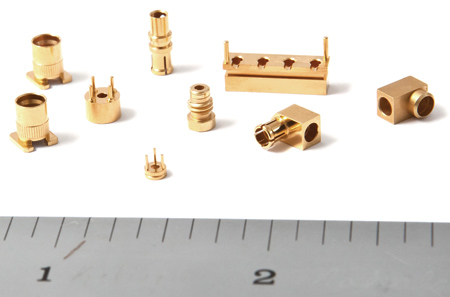
Thomas W. Springer manufactures complex close tolerance components made from Kovar, SST, aluminum, beryllium, copper, brass and most plastics, including Ultem, Vespel and Fluoroloy, in quantities from one to 50,000.
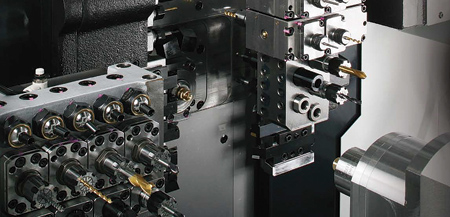
The Tsugami S206's modular tooling layout can feature up to 15 different live tools. The S206 features a Y-axis tool post, which allows users to machine complex parts using the main and back spindle simultaneously.
Thomas W. Springer, a second-generation CNC job shop founded in 1976, manufactures complex close tolerance components made from Kovar, SST, aluminum, beryllium, copper, brass, and most plastics including Ultem, Vespel, and Fluoroloy, in quantities from one to 50,000.
"Parts are being engineered increasingly smaller over the years, requiring smaller tools with a higher chance for tool breakage and chip removal issues-not ideal for unattended machining without a tool monitoring system," said a company spokesperson.
One of the company's recent manufacturing challenges involved a miniature fitting in 316L material with 16 RMS finish in a cone that tapers to O.021 and a O.010 through hole. The job was taken as a "best effort only" job with a top set-up man only being able to produce up to 55 parts in an 8 hour shift.
Thomas W. Springer has been using Tsugami solutions for 25 years. For this manufacturing challenge, after researching other options, the solution was a Tsugami S206 6-axis opposed gang tool CNC lathe with a CARON Engineering Tool Monitoring Adaptive Control (TMAC) system. "We have always received exceptional support from Tsugami in the past, even on older model machines, so we knew what to expect for support on new purchases," said the spokesperson. "We worked with Ron Gainer, who guided us in outfitting our most recent S206 with a Caron TMAC system and was also able to get us an extended trial period to make sure the TMAC system would work for us."
The Tsugami S206 is suitable for variable volume production with a wide range of capability. The S206's modular tooling layout can feature up to 15 different live tools, delivering enhanced capability and rapid changeover times. The S206 features a Y-axis tool post, which allows users to machine complex parts using the main and back spindle simultaneously. The Tsugami S206 CNC lathe is convertible and may be run as a traditional sliding headstock Swiss turn using the guide bushing or run without the guide bushing with the addition of an optional chucker kit. When run as a chucker the S206 can use drawn bar stock instead of centerless ground stock, reducing remnant size and increasing shop flexibility.
CARON Engineering's TMAC system protects the CNC machine while providing valuable information about the cutting process. TMAC is designed to reduce the high costs associated with broken tools, lost production and rejected parts by effectively measuring tool wear in real time. It operates on the principle that the power required to cut a part increases as the tool's cutting edges deteriorate. The "Adaptive" control feature of TMAC reduces cycle time and optimizes cutting time under changing cutting conditions to improve tool life.
Adding the TMAC system allowed Thomas W. Springer to increase the output to 300+ parts running 20 or more hours per day, 12 of which are unattended.
Most of the parts have a lot of intricate internal work consistently requiring a 16 finish or better in heat treated 17-4PH or 316SST. "We hold +/-.0002 inch in Nitronic 60 all day long with some unattended running at night," said the spokesperson.
The most challenging part on the S206 is not really complex, but micro in size. "We can drill a .009 inch hole at 10,000 RPM in 316L SST for thousands of parts and bore down to .021 inch diameter," said the spokesperson. "The same part also has an M2X.25 internal thread that is too small for a single point tool, so we use a thread mill on the sub side in 316L material. Another big advantage of these machines is the high-pressure coolant and the 8,000 RPM cross-attachments that smaller tools require."
The company now has six Tsugami S206 Swiss-type CNC lathes, two with TMAC systems.
Thomas W. Springer currently employs 25 full-time employees operating 30 CNC machines in a 20,000 sq. ft. facility running one manned and up to two unmanned shifts. Industries served include electronics, life-sciences, analytical instruments, aerospace, medical and military.
The company uses Esprit for lathes and Mastercam for mills, and utilizes LNS barfeeders.
"Our goal is to stay ahead of the curve by staying lean, using modern state of the art equipment and software, and continually striving for as much unattended operation as possible," said the spokesperson. "The manufacturing industry is facing a shortage of skilled workers, we plan on continuing to utilize automation to fill the gaps."
For more information contact:
Thomas W. Springer, Inc.
227 Buttonwood Road
Landenberg, PA 19350
610-274-8400
www.twspringer.com
Rem Sales, LLC
910 Day Hill Road
Windsor, CT 06095
866-224-8576
www.remsales.com