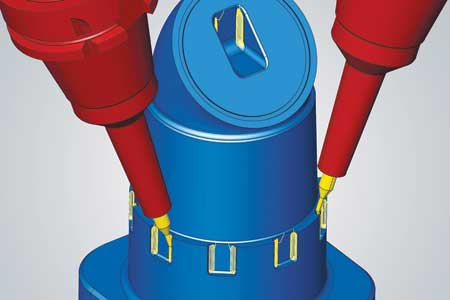
In 3-axis and 5-axis machining, new algorithms for rest material detection help ensure that all rest material areas are automatically accounted for in full.
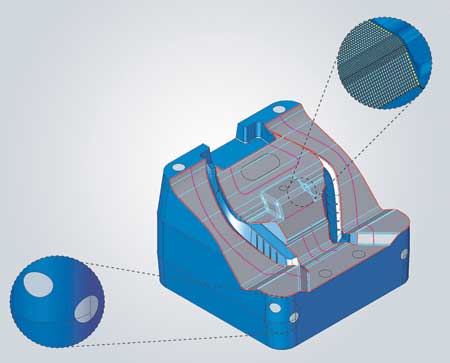
hypermill CAM Plan calculates the optimum point distribution based on part topology data.
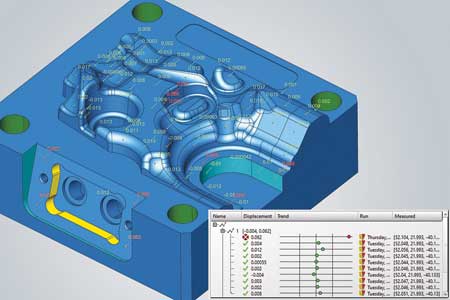
Measuring points read back for improved quality and process control. The 3D model of the component shows at a glance which measuring points are outside the tolerance.
OPEN MIND Technologies will be highlighting the hyperMILL 2024 at IMTS booth 133351 located in the Software Pavilion. OPEN MIND recently introduced its latest hyperMILL 2024 CAD/CAM software suite that includes a range of enhancements to its core toolpath capabilities, as well as new functionality for increased NC programming efficiency in applications ranging from 2.5D machining to 5-axis milling.
In addition to its show presence, OPEN MIND, together with Oak Ridge National Laboratory, will be making a presentation at the IMTS Conference Sessions, titled "HEAL-IT: Hybrid-Manufacturing Enabled Agility and Longevity of Industrial Tools". The presentation by David Bourdages, Additive Manufacturing Product Manager at OPEN MIND Technologies, and Lauren Heinrich, R&D Staff Member at Oak Ridge National Laboratory Manufacturing Demonstration Facility, will focus on a recent collaboration to repair a bottle mold using hybrid manufacturing (additive and subtractive machining), and will take place on Wednesday, September 11 at 11 AM to 11:55 AM in Room W192-C, West Hall. For more information and to register, visit imts.com/conference.
New and Enhanced CAM Capabilities
An Optimized Deep Hole Drilling CAM strategy offers improved machining reliability by providing a user-friendly interface with process-relevant parameters clearly defined on a new process tab. New capabilities enable coolant and dwell time stages to be identified, allow a chip break to be integrated into a drilling process and more. A new single-tip gun drill tool simulation function provides precise collision checking and a detailed visualization of the stock removal.
A new algorithm for 3-axis and 5-axis rest machining helps ensure automatic, complete detection of all rest material areas, in addition to optimized toolpath calculations for faster, reliable machining. Toolpaths are now optimally divided to ensure more efficient machining, and the detection of intersection areas where paths meet has been optimized for collision avoidance.
An additional toolpath improvement is an enhanced path layout for the 3D Plane Machining cycle. The new strategy has a smoother path and fewer pick-ups. While the toolpath length (distance) may be longer in some cases, the machining time, as tested on a variety of NC controllers, has been reduced.
A new, novel generation of programming assistance and analysis, "CAM Plan," is introduced in hyperMILL 2024, simplifying various programming tasks and identifying possible sources of error. Predefined workflow steps safely guide users through the preparation and programming process, while the geometries and features required are automatically created. Also, potential errors are flagged for removal, such as double surfaces or gaps between model patches.
Once the data is organized, the CAM workflow can be processed with more intelligence and higher efficiency. The first benefit from hyperMILL CAM Plan is that component topology is analyzed to produce a precise toolpath that has command locations aligned with key geometric features and with optimized point distribution for milling. The result is improved surface finishes, easier processing by NC controllers and reduced machining times.
Optimizing VIRTUAL Machining
For easy generation of 3-axis and 5-axis NC programs with axis change and an optimized use of the workspace, the NC Optimizer feature in the hyperMILL VIRTUAL Machining strategy now offers the option to transform X- and Y-axis movements into a movement that utilizes the rotation axis in the table. By swapping axes, an XY movement is transformed into a simultaneous CX movement, which eliminates rewind movements during machining. This is especially impactful on machines that have a limited linear axis range.
The reading back of measuring points when using hyperMILL VIRTUAL Machining is a new feature that allows graphical representation of measured points on the part model, rather than comparing a list of measurement results. Users can also quickly identify measuring points that are out of tolerance on a 3D part model and compare trends over sequential measurements. As a result, it is easier to analyze and compensate for inaccuracies and tool wear after milling.
For more information contact:
OPEN MIND Technologies USA, Inc.
1492 Highland Ave., Unit 3
Needham, MA 02492
888-516-1232
info.americas@openmind-tech.com
www.openmind-tech.com
IMTS East Building, Level 3
Booth 133351