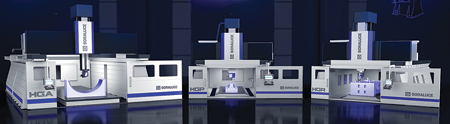
Soraluce Dynamic Line of high rail gantry machines, shown left to right, HGA Series, HGP Series and HGR Series.
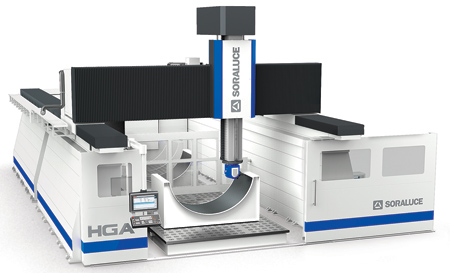
Soraluce Dynamic Line HGA high rail gantry machine configured with dust extraction system on the head and 5-axis contouring fork-type milling heads. It is suited for aerospace applications machining composites and aluminum.
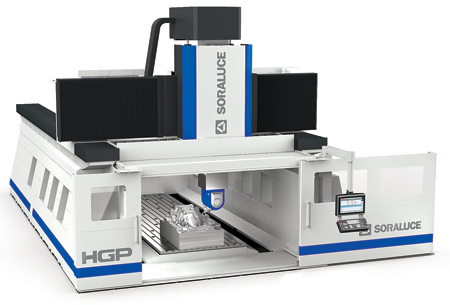
Soraluce Dynamic Line HGP high rail gantry machine configured with 5-axis contouring fork-type milling heads. It is suited for mold & die applications.
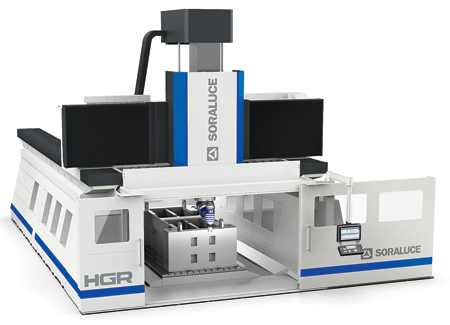
Soraluce Dynamic Line HGR high rail gantry machine available with an automatic head changing system for a wide range of spindle heads to deliver high stock removal and versatility for mechanical engineered products.
Soraluce has launched its Dynamic Line of high rail gantry machines.
"The high rail gantry machines from Soraluce are engineered to propel manufacturing operations to unprecedented levels of performance," said a company spokesperson. "Offering high-speed cutting capabilities, exceptional precision rates and the ability to handle high-volume machining tasks, these machines are backed by Soraluce's extensive expertise in the milling sector and state-of-the-art technology."
The Dynamic Line comprises three machine models tailored to applications in sectors such as aerospace, mold & die and mechanical engineering, with solutions designed for specific materials like composites, light alloys and steel-based components.
Tailored to suit the specific needs of diverse sectors and applications, these machines can be outfitted with either 5-axis contouring fork-type or high-torque milling heads. This versatility allows seamless handling of intricate and complex shapes. Additionally, they feature a comprehensive splash guarding system to uphold cleanliness and safety standards in the working environment. Moreover, incorporating diverse dust extraction systems, both within the enclosure and integrated into the heads, facilitates the removal of dust and debris generated during machining processes, thereby maintaining optimal cleanliness throughout operations.
Increased efficiency is provided with the High Dynamics feature of the Dynamic Line high-speed cutting capabilities. With axes speeds reaching 60,000 mm/min and accelerations to 4 m/sq. sec., these machines are engineered to improve productivity.
The 5-axis contouring heads offer speeds of up to 30,000 RPM with high precision. "With these heads, intricate designs and complex geometries are achievable," said the spokesperson. "Whether you are sculpting the perfect aerospace component or executing intricate mold & die machining, semi-finishing and finishing in steel or aluminum, the High Dynamics feature ensures that your machining operations are executed with unmatched precision and efficiency."
The Dynamic Line offers enhanced surface quality due to thermal stability, helping ensure that performance remains consistent even in the face of fluctuating temperatures and rigorous machining tasks.
Moreover, the Dynamic Line features highly calibrated kinematics, further enhancing its ability to deliver advanced results. "Every movement is precisely controlled, every motion meticulously calculated, ensuring that each component is crafted with the utmost accuracy and finesse," said the spokesperson.
The spokesperson added, "The Dynamic Line's high revolutions enable long-duration machining without compromising on quality or performance. Whether you are engaged in marathon machining sessions or tackling intricate designs that require extended running times, Dynamic Line delivers consistent results, time and time again."
At the heart of cutting power lies heavy-duty mechanical heads, engineered to provide power with up to 73 kW. This power output helps ensure optimal performance, enabling users to tackle challenging cutting tasks with ease and precision.
A diverse range of high-torque mechanical 5-axis contouring heads is available, featuring torque levels of up to 2,000 Nm. This versatility empowers operators to execute intricate cuts with accuracy, catering to a wide spectrum of application needs across various industries.
To augment stability and performance, cutting power integrates intelligent damping solutions such as DAS+ and DWS, complemented by a full cast iron structure. These features work in tandem to minimize vibrations and help ensure consistent operation, even in demanding working environments.
"We are thrilled to introduce the Soraluce high rail gantry machines, representing a new pinnacle in precision engineering," said Oier Elguezabal, Global Business Development Director, Soraluce. "These machines embody our commitment to innovation and excellence, empowering manufacturers to achieve unparalleled levels of productivity and quality in their operations."
For more information contact:
Doug Schulte
Select Machining Technologies
910 Day Hill Road
Windsor, CT 06095
256-508-0805
dschulte@selectmachiningtech.com
www.selectmachiningtech.com