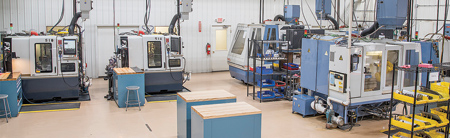
Fully automated tool grinders and trays filled with upcoming jobs offer a window into the long-standing partnership between ANCA and Tru-Edge.
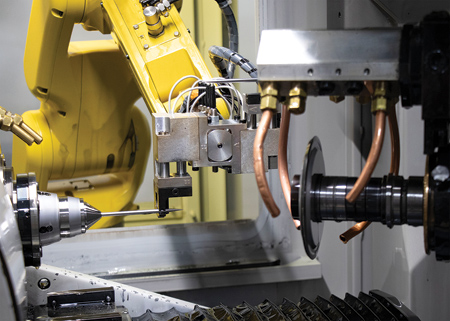
Speedy automation is one reason Tru-Edge makes its medical customers happy. Here, one robot gripper on an ANCA MX7 removes a finished surgical instrument just before its twin swings down to load the next blank.
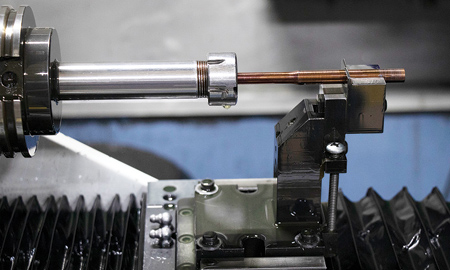
Tru-Edge relies on ANCA's traveling steady rest and part-specific bushings to keep tools perfectly straight during the grind
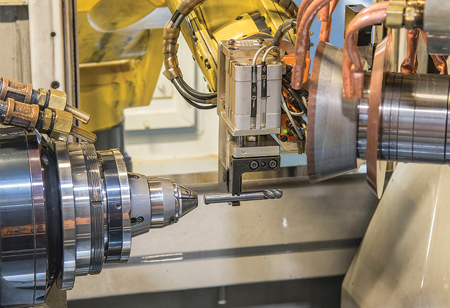
Metalworking tools, like this carbide ball nose endmill, account for most production at Tru-Edge
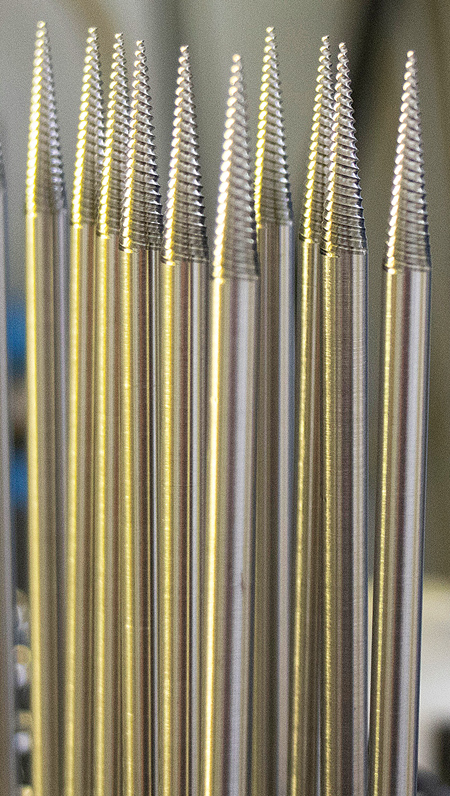
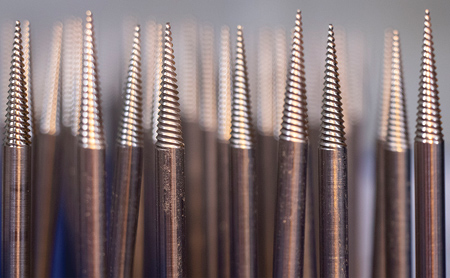
Guided by the motto to "Simplify Tooling to Deliver Productivity," Tru-Edge has long provided proficiency in manufacturing and re-sharpening custom crafted round tools in several industries, including aerospace and automotive. Success in these industries stems from its expertise in tight tolerance carbide grinding, an experienced tool design team and a technical sales staff that knows how to solve problems at the spindle. While the team has carried on this tradition since 1996, they added a new capability in 2007.
That year, several big orthopedic customers in the Warsaw, IN, area contracted with Tru-Edge to produce hip broaches, bone rasps, bone graft drills, reamers and taps-all of which are typically stainless steel tools with entirely different geometries than the metalcutting tools they were accustomed to manufacturing. The team embraced the challenge and made it a key part of Tru-Edge's business, earning ISO 9001 and ISO 13485 certification and adapting to customers' changing demands in the years that followed. Vice President Brian Hackman reported that surgical instruments now represent 10% of their total sales, even as the company continues to grow rapidly.
Sticking with ANCA Machines
From the beginning, ANCA tool grinders represented Tru-Edge's primary production equipment, and their inherent flexibility made them a perfect fit for the new line of business. Hackman recounted that for the first 14 years or so, the contracts called mostly for reusable instruments, with the ultimate customer being major hospitals that had the ability to sterilize the instruments.
"They wanted the tools to be as visually appealing as they could possibly be," said Hackman, "and Tru-Edge-produced tools had a jewel like appearance due to the highly polished surface finish and complex geometries. The different facets and reliefs we would grind in them would literally sparkle." By optimizing wheels, plus the speeds and feeds on their ANCA TX, MX and FX machines, Hackman said Tru-Edge was also able to deliver a burr-free finish that virtually eliminated the need for post-processing. This contributed to even more business and an award from the regional manufacturing association in 2018.
Hackman credited their success in part to innovations in ANCA's Toolroom software and the incorporation of linear motors. While Rick Brunswick, Engineering Manager at Tru-Edge, pointed to ANCA's in-process wheel dressing capabilities as a key ingredient to maintaining tight form tolerances, especially on medical taps, while also reducing cycle time and the number of operations. He added that they favor ANCA's approach to outfitting a machine with a large (o250 mm) dressing roll around the work head, rather than the optional side-mounted dresser. "It lasts much longer, because you have more surface area on that diamond dressing roll than you would with a smaller dressing roll that is off to the side," he said.
Automation Solutions
By 2020, reported Hackman, customer requirements started shifting dramatically toward single use instruments, owing to a corresponding explosion in the number of orthopedic surgeries occurring in smaller outpatient medical centers, facilities that are generally doctor-owned. As Hackman explained, demand for a simpler, functional tool at the lowest cost, replaced the need for a visual showpiece. Thus, the primary material changed from 17-4 stainless steel to various other types, such as 455, 465, etc., which have "a different surface finish and tend to produce more burrs, so it takes more time to deburr the parts," explained Hackman.
As one might expect, the switch to single use instruments also increased production volumes exponentially. As Hackman summarized it, "Ten years ago we were doing six-, eight- and 10-piece orders. We had an 11,000-piece order last July. We still have the technology, the innovation and the know-how to provide a burr-free, beautifully finished part. But now we have to manufacture them by the thousands, instead of by the fives and sixes."
Once again, ANCA fit the need. For example, with robot loaders and automatic wheel changing from a six-position carousel on the MX machines, Tru-Edge is able to run lights-out. Another contributor is the traveling steady rest, riding on what ANCA calls the P-axis. As Brunswick explained, long, thin surgical cutting tools tend to bow, but Tru-Edge developed part-specific bushings that, in conjunction with the steady rest, force the tool into a perfectly straight set-up for the grind. As such, Hackman said a single MX can produce 5,000 small diameter surgical drills per month.
Automating femoral rasp production typically involves both an automatic collet chuck and a swing-out tailstock to secure the other end. As Hackman put it, these rasps vary widely. "Some are long, skinny and very concentric," he said. "Others are more crooked, like a dog's leg. So, we had to develop part specific tailstock fixturing to allow different shapes to be held on center." (Tru-Edge makes its own fixtures at a sister company, MetalCut Tool Services, in Dayton, OH.)
These parts are typically designed in Siemens NX, and ANCA provides a post-processor to create the necessary machine motions. After importing this file, ANCam gives the operator the ability to manage specific process parameters, like speeds and feeds, offsets and wheel selection and dressing cycles. While ANCA's CIM3D package offers a full simulation to verify the grinding motion and to compare the expected part with the original model.
In short, with engineering, design and manufacturing all under one roof, Tru-Edge leveraged its partnership with ANCA to reduce cycle time, remove supply chain pain and reduce the end-users' total cost of ownership.
Bright Future
Hackman foresees continued growth in the medical instruments market as baby boomers continue to age and the trend of patients seeking care at smaller surgical centers continues. He believes that Tru-Edge's embrace of automation positions them to be "the premier supplier to the industry for that niche market." In fact, he added, their orthopedic customers have made Tru-Edge their sole supplier for instrument grinding.
Along that line, Hackman said Tru-Edge's next project is further automating bone rasp production. That advance would grow the company's medical business 10-15%, he reasoned, eliminating the need to buy another four machines and hire enough staff in today's tight labor market to hand load these complex parts.
At Tru-Edge, the future is bright because the company has expanded its capabilities and managed growth with surgical precision.
For more information contact:
Tru-Edge
752 Jim Lachey Dr.
St. Henry, OH 45883
419-678-4991
tru-edge@tru-edge.com
www.tru-edge.com
ANCA Inc.
31129 Century Drive
Wixom, MI 48393
248-926-4466
usainfo@anca.com
www.anca.com