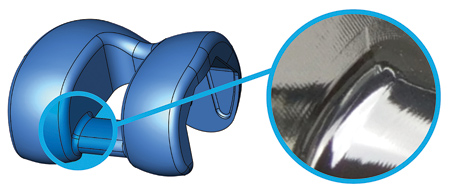
Small defects, commonly referred to as "shadows," are marks left by the machining operation when the cutting path, tool and machine are not optimized. These shadows subsequently require additional hand work, increase the risk of scrap and add cost to the overall process.
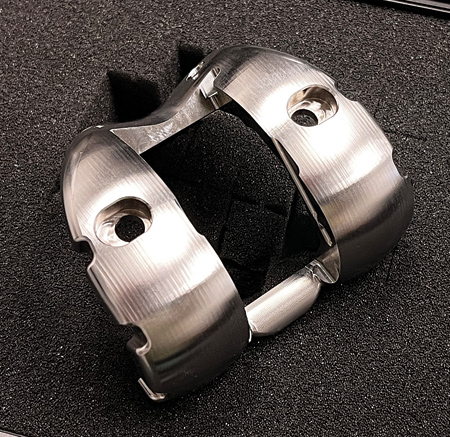
The holistic approach by GF Machining Solutions can improve surface finish smoothness by up to 80%, allowing implants to go from milling directly to polishing-saving time and operator hours-while eliminating the need for a secondary grinding operation.
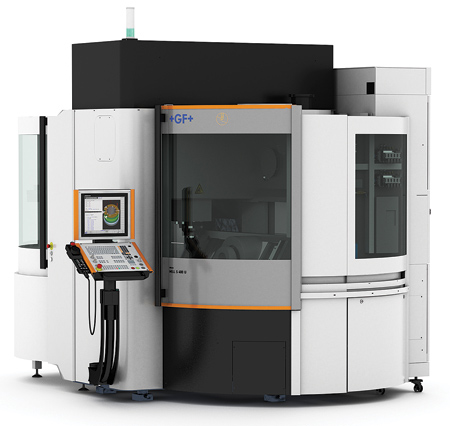
For its MILL S Series machines, GF Machining Solutions equips all its axes with linear drives and torque motors that are also internally cooled.
The success and longevity of a knee replacement depends, in large part, on the quality of the components. For the femoral side of the implant, tolerances and surface finishes are key, which makes the milling operation especially challenging. Small defects, commonly referred to as "shadows," created by depth differences in machined surfaces of only 20 microns (0.0008") can occur. These shadows subsequently require additional hand work, increase the risk of scrap and add cost to the overall process.
Fortunately, the combination of advanced cutting tools, software and the right machine can potentially reduce milling time by over 30%. But more importantly, this holistic approach can improve surface finish smoothness by up to 80%, allowing implants to go from milling directly to polishing-saving time and operator hours-while eliminating the need for a secondary grinding operation.
In this knee implant joint effort, the machine tool for the milling operation must have certain design features that control vibration, provide high-accuracy axis movement and compensate for thermal fluctuations, thus ensuring precision and a repeatable process. With those machine capabilities, shops can then take full advantage of special cutting tool geometries along with advanced CAM software specifically developed for the process.
One such machine tool that delivers all the necessary capabilities for femoral knee implant machining is a Mikron MILL S Series milling machine from GF Machining Solutions. In addition to high-speed spindles, the machines feature a polymer concrete base, linear and torque motor drives and advanced thermal compensation systems.
A MILL S Series machine's polymer concrete base is an engineered material, and as such, it allows machine builders like GF Machining Solutions to design in stiffness where it is most needed and vibration dampening where it is required. Effective vibration dampening and extreme strength where needed in a machine base contribute greatly to workpiece surface finishes and cutting tool life.
Because polymer concrete is an engineered material, MILL S machine bases can also incorporate efficient internal cooling channels. These built-in cooling systems help ensure the machine operates at static thermal conditions even when a shop's ambient temperature varies. When it comes to high-tolerance workpieces such as femoral knee implants, internal base temperature control also contributes to higher positioning accuracy, which in turn, helps reduce the risk of shadowing on part surfaces.
Along with internal base temperature control, drives and torque motors also play a key role in a machine's positioning accuracy. The more precise a machine moves, the less chance of shadowing on a knee implant's surface finish.
For its MILL S Series machines, GF Machining Solutions equips all its axes with linear drives and torque motors that are also internally cooled. "Compared to conventional mechanical ball screw drives that have inherent backlash, linear type systems never experience backlash because they are electrical and have no mechanical components," said a company spokesperson. "As such, there is no physical contact between the system's elements that are guiding it. This translates into faster acceleration and deceleration speeds along with greater stiffness and smoother motion-resulting in shorter cycle times, better surface finishes and high precision."
Taking machine positioning accuracy to the next level, GF Machining Solutions equips its MILL S Series machines with the company's Intelligent Thermal Compensation (ITC) system that basically guarantees repeatable results across many hours of continuous machine operation, the company reported. The system's software relies on real-time measurements and uses algorithms to further reduce any chance of machine drift caused by thermal variations.
Thermal variations occur when a machine is under different loads as well as during work interruptions such as tool or pallet changes. "The ITC system keeps these variations in check to within 5 microns as compared to standard compensation, which often drifts by over 30 microns," noted the spokesperson.
ITC uses sensors to monitor several aspects of a machine, in particular the temperature of the water in the internal cooling systems for the base and axis drives. Larger temperature variations will obviously impact the machine more than will smaller fluctuations. The ITC system identifies the amount of variation and the direction of machine drift and compensates accordingly for each machine axis.
"Efficient manufacturing of complex medical parts such as a femoral knee implant depends on using the best available technology at every process step," said the spokesperson. "By taking a holistic approach that encompasses advanced cutting tool geometries, optimized CAM software and high-precision machines such as those in the MILL S Series from GF Machining Solutions, medical shops can develop a stable, reliable machining process that significantly reduces costs and improves overall product quality."
For more information contact:
GF Machining Solutions LLC
560 Bond St.
Lincolnshire, IL 60069
800-282-1336
info.gfms.us@georgefischer.com
www.gfms.com/us