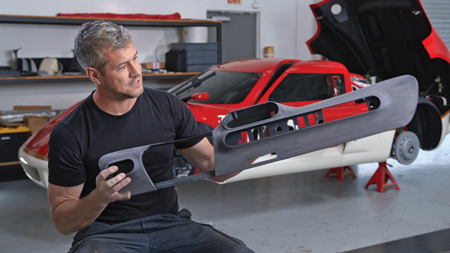
Ant Anstead shows a 3D-printed part for the Lotus Type 62-2 coachbuilt as shown in the Discovery+ documentary, "Radford Returns."
Stratasys Ltd. partnered with Radford, a global luxury automotive brand, to create over 500 3D-printed parts for the launch of the Lotus Type 62-2 coachbuilt as shown in the Discovery+ documentary, "Radford Returns."
Radford Returns tells the story of the revival of the art of coachbuilding using technology for the 21st century. The show features car builder and host Ant Anstead and former Formula One champion racecar driver Jenson Button, and documents the build of the retro-modern Lotus Type 62-2 supercar. It features the uses of 3D printing, and viewers get an inside look at the process from designing to prototyping, tooling and finally producing production parts utilizing Stratasys FDM, PolyJet and stereolithography 3D printing technologies.
To produce the first two cars, over 500 parts were 3D-printed at the Radford Studio, automotive design and engineering firm Aria Group, and Stratasys Direct Manufacturing. Using Stratasys' GrabCAD Shop workflow software, the Radford team scheduled and tracked their 3D prints across five global locations, using a fleet of up to 20 different Stratasys 3D printers at one time-a true demonstration of distributed manufacturing. The array of Stratasys printers included the F900, F770, Fortus 450mc, F370 and J55, each used to achieve different desired outcomes for each part.
By utilizing various 3D printers and technologies, the team was able to produce parts like a large solid composite firewall sandwich core, printed in two halves on the Stratasys F900 printer in ULTEM 1010 resin. The part was bonded together and then wrapped with carbon fiber without the use of a layup tool. The design of the firewall included complex mounting features for interior speakers, a fuel filler mount and a luggage compartment. Additionally, many exterior items like side mirror housings, radiator ducts and body vents were printed in FDM Nylon 12 Carbon Fiber and ASA materials. Numerous mounting brackets throughout the car were printed in FDM Nylon 12 CF due to many factors, including strength requirements, the aggressive project schedule and complete design freedom.
Stratasys will continue to support the Radford Lotus Type 62-2 project with 3D-printed production parts across the company's various 3D printing technologies including FDM, SAF, stereolithography and P3 Programmable PhotoPolymerization.
For more information contact:
Stratasys Ltd.
7665 Commerce Way
Eden Prairie, MN 55344
877-489-9449 / 952-937-3000
info@stratasys.com
www.stratasys.com/automotive