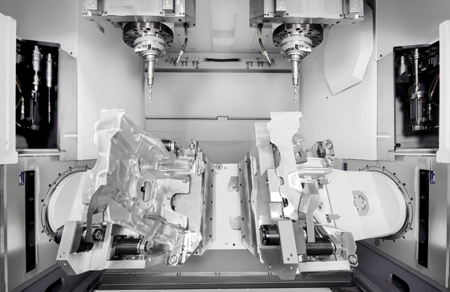
Double-spindle machining on a DZ 25 P increases productivity in series production of structural components.
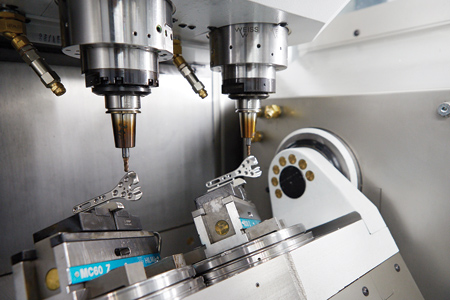
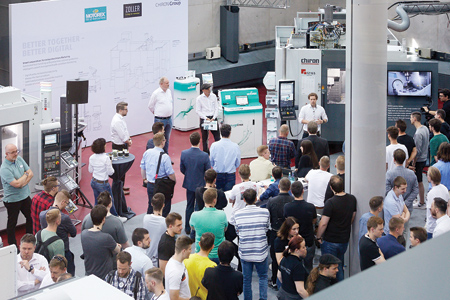
The recent CHIRON Group open house in Tuttlingen, Germany, had more than 1,200 visitors from around the world and featured new technology to improve manufacturing practices.
Visitors saw live demonstrations of combined friction stir welding (FSW) and machining processes, scalable manufacturing system for microtechnology and high-productivity twin-spindle machining-three new product innovations by the CHIRON Group that are focused on productivity, efficiency and sustainability.
The 22, 25 and 28 Series machines offer enhanced dynamics and stability, large working chamber plus a twin-spindle machining center concept with a spindle distance of up to 1,200 mm.
"These features are engineered to provide greater productivity and precision," said a company spokesperson. "As an example, a DZ 25 P that has been in use for two years improved the manufacturing of automotive structural components. All in all, this turn-key solution has provided, according to the customer: 'A stable and high-precision process with greatly increased output in comparison to the previous system.'"
"In addition to other double-spindle applications, such as battery and eMotor housing manufacturing, these new series are also fully capable of massive machining applications starting with solid material," added the spokesperson. "The stable portal design forms the basis for high precision, while an efficient work area and user ergonomics enable flexible integration of a wide range of automation solutions for ideal productivity and process reliability."
Scalable Manufacturing System for Microtechnology
The CHIRON Group also demonstrated a new manufacturing system for the microtechnology sector. It offers high-precision automated machining of workpieces with maximum dimensions of 50 mm x 50 mm x 50 mm. "It is based on the Micro5 from the Chiron FACTORY5 brand-a high-speed milling center with the power consumption of a coffee machine and the size of a refrigerator," said the spokesperson
As a stand-alone solution, it is suited for manufacturing smaller batch sizes in the medical technology sector. With its six-pallet capacity, the Micro5 also supports production with minimal personnel.
"The combination of a Micro5 with a Feed5 handling system will form an ideal plug & play solution once it enters series production. Feed5 offers increased autonomy for automated workpiece handling with a 6-axis robot. Capacities for Micro5 and Feed5 projects are currently being expanded further," the spokesperson said.
Combining Friction Stir Welding and Machining
"One process that may not be particularly well known is friction stir welding (FSW), a reliable, efficient and sustainable manufacturing technology for creating pressure-tight and media-tight connections between two materials," said the spokesperson.
The spokesperson continued, "FSW is suitable for applications that involve joining aluminum or unrelated materials. The target workpieces for FSW currently include battery trays and inverter housings, as well as all electronic components that require heat dissipation alongside high requirements for leak-tightness. FSW technology also enables car manufacturers to relocate electrical modules to the wet areas of vehicles."
"The CHIRON Group boasts comprehensive expertise and practical user experience for machining these target workpieces," the spokesperson said. "By combining FSW and machining, the CHIRON Group is developing a forward-thinking innovation to provide benefits for users similar to those offered by other process combinations: reduced space requirements, shorter cycle times and higher quality and productivity. The first projects using this combination are already underway at a technology partner company, resulting in the first turn-key machining centers such as the MILL 2000 machining center, offering combined FSW and milling technology."
"We received much positive feedback from customers, partners and suppliers on the many new innovations and experiences at the open house, indicating that the CHIRON Group and the product portfolio has the right answers to current and future questions and demands," said Carsten Liske, CEO of the CHIRON Group.
For more information contact:
CHIRON America, Inc.
10950 Withers Cove Park Drive
Charlotte, NC 28278
704-587-9526
info@chironamerica.com
www.chironamerica.us