
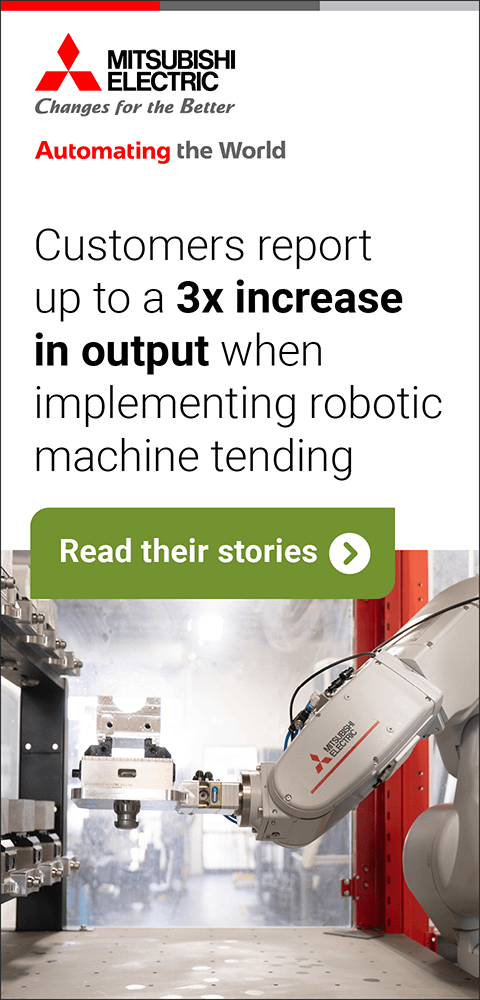
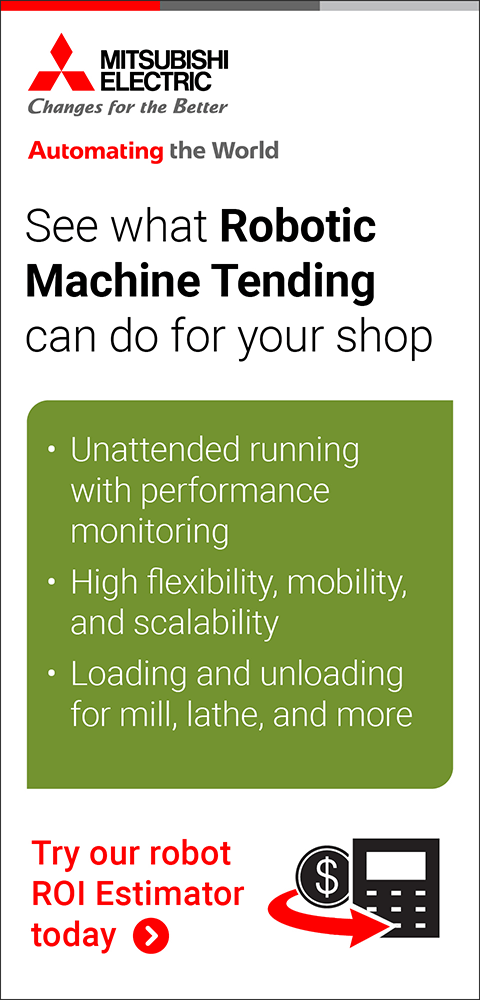
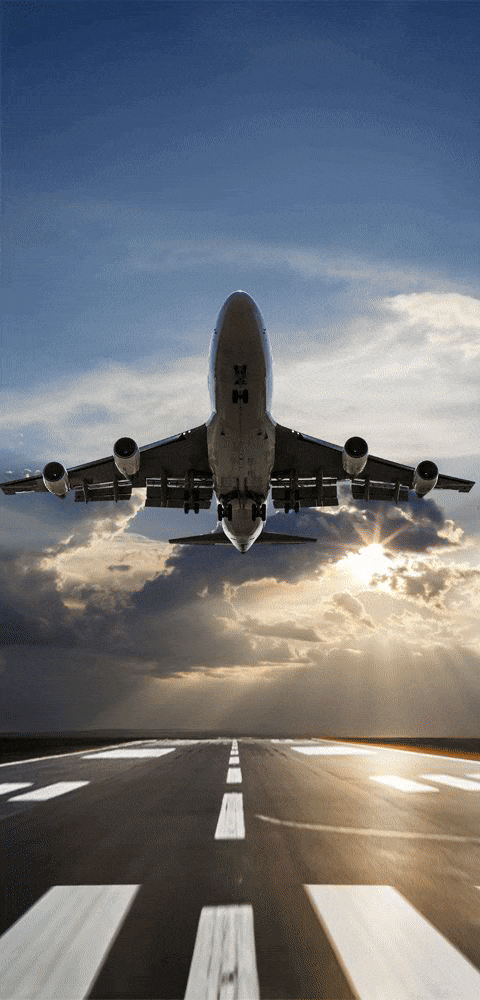
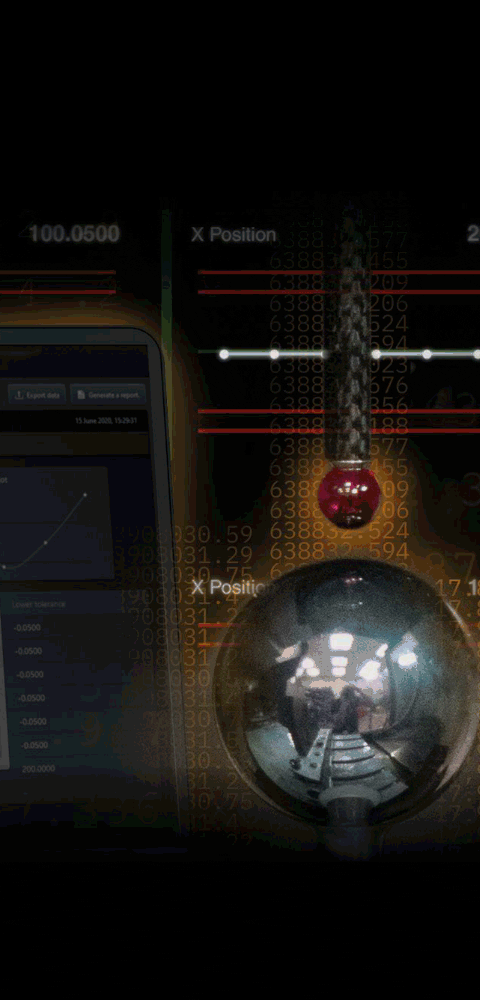
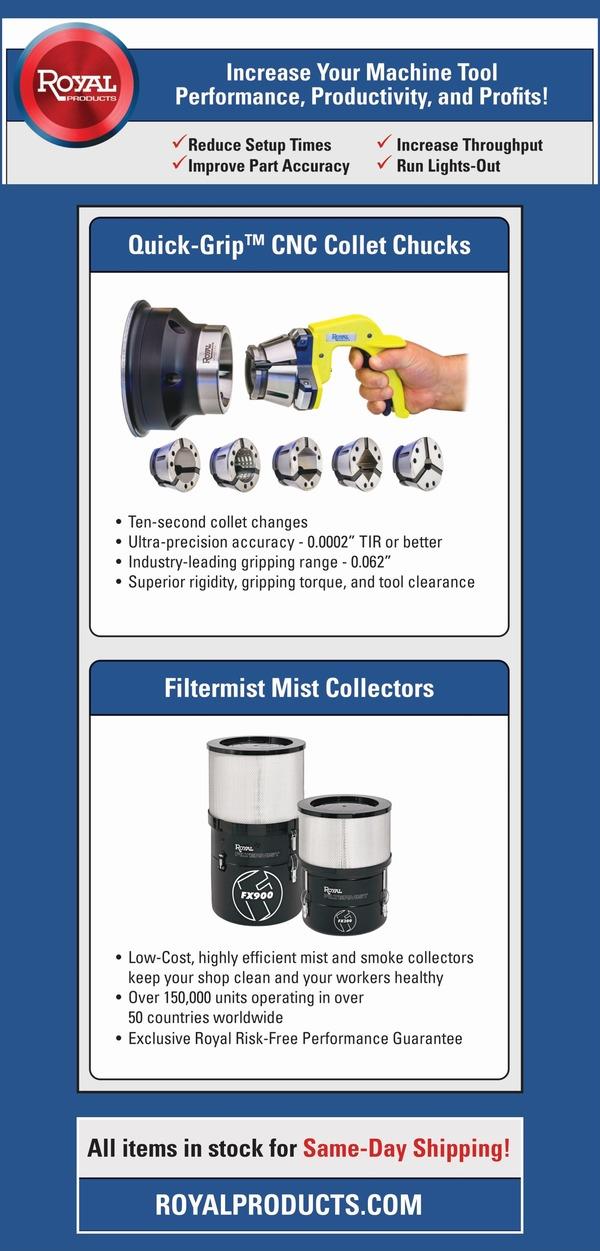
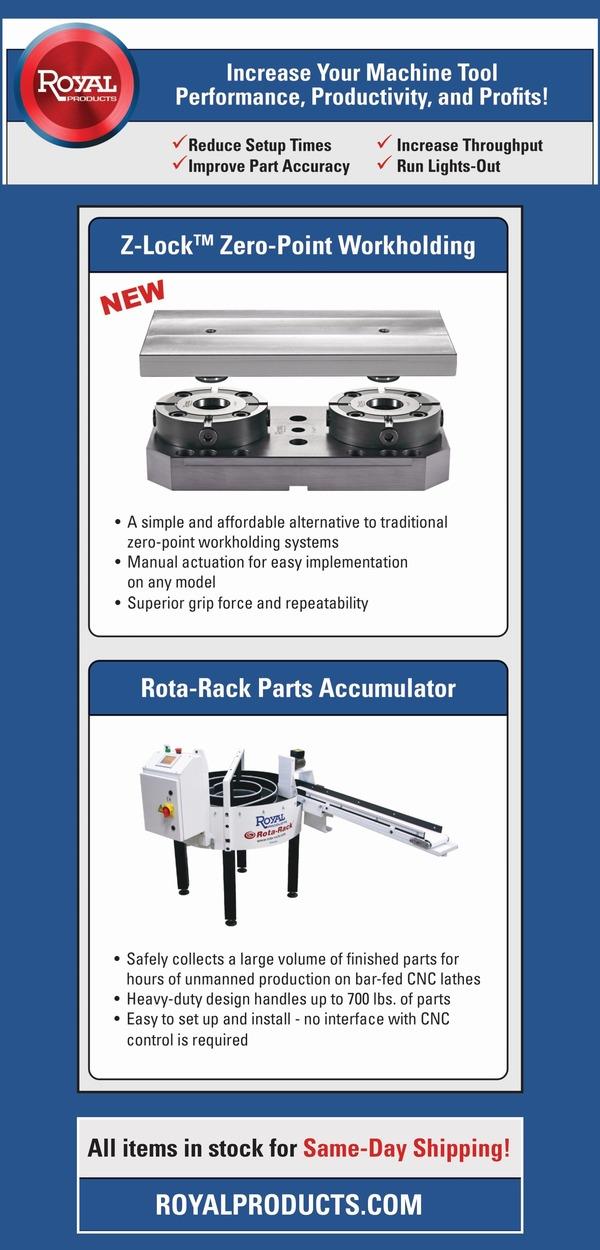

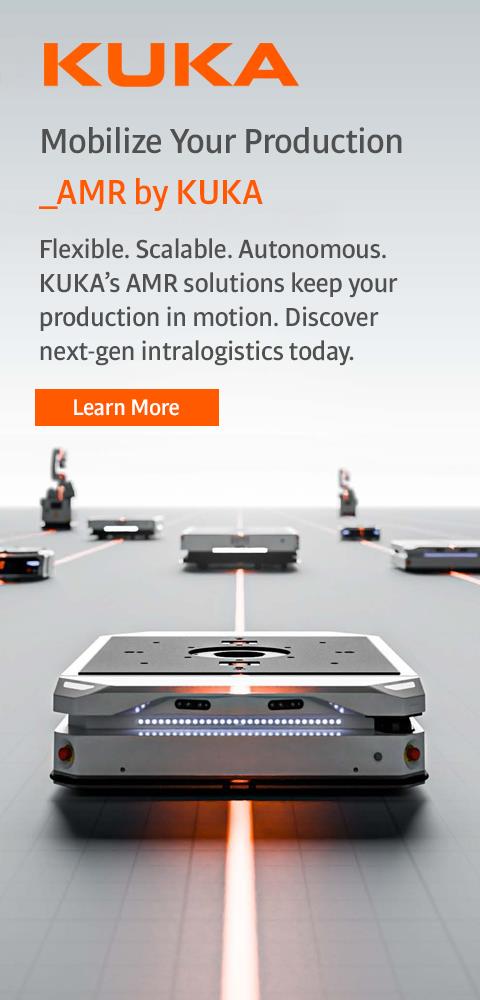
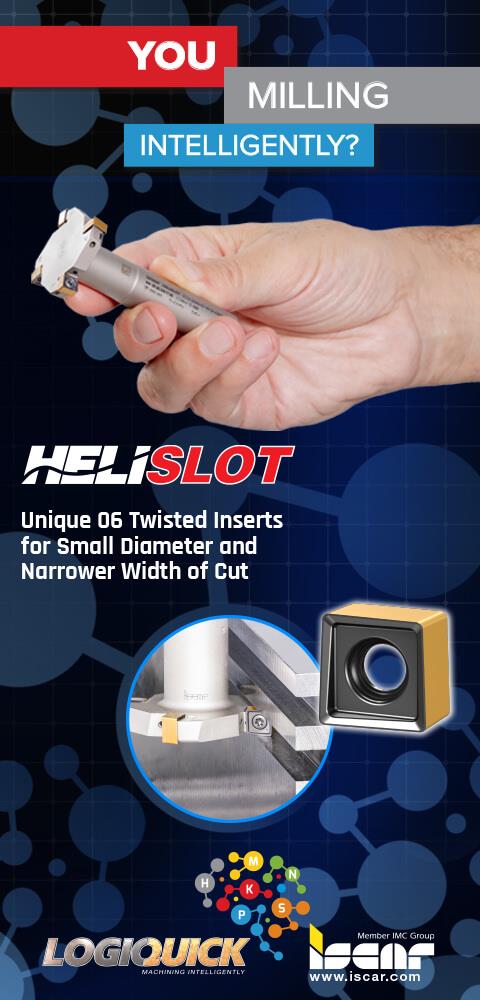
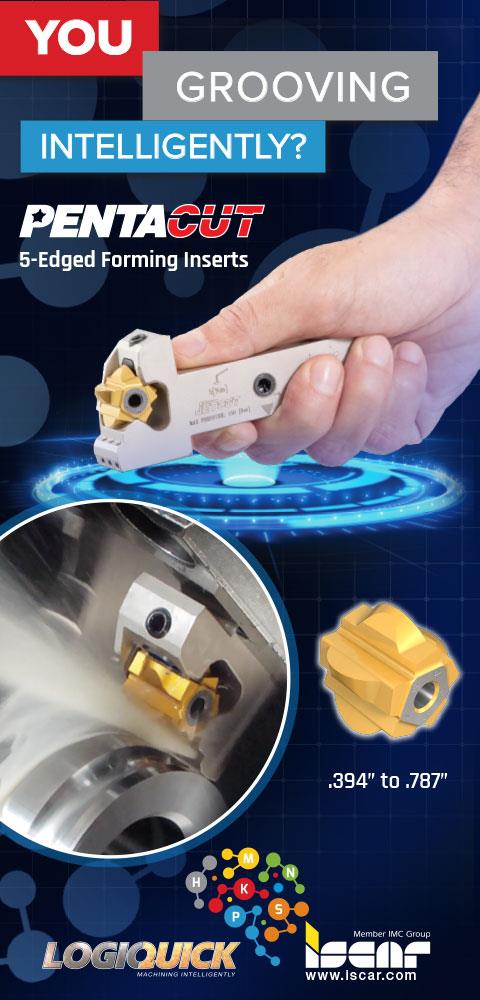
5-Axis CNC Turning/Milling Center
August 1, 2020
V-Tec by Vision Wide now offers its first 5-axis CNC turning and milling machining center. The ASM series vertical and horizontal 5-axis machining centers are designed by Vision Wide to meet machining requirements for delicate cylindrical components requiring high acceleration, rapid feedrate and synchronized axes machining. Suitable for aerospace and automotive components, this series features a contour accuracy of +/-0.03 mm and a total cycle time of 25 minutes.
The ASM series is equipped with a 2-axis continuous head with a built-in spindle, allowing for simultaneous 5-axis machining while maintaining a highly rigid and light weight mechanical structure. There is a built-in no-backlash direct-drive motor specifically for the milling of filiform and narrow workpiece contours. The spindle located within the head is a high-speed 12 k/24 k RPM, HSK-A100 taper with thermal compensation and cooling systems.
ASM Series machines also come with a Heidenhain TNC640 control with Heidenhain Dynamic Collision Monitoring. X-axis travel ranges from 39.9" to 63.8" with a Y-axis of 49.6" and Z-axis of 41.3". Other features include an automatic pallet changer, a 40-, 60- or 116-piece automatic tool changer, a cutting feedrate of 945 IPM and a rapid traverse of 1,575 IPM.
All V-Tec by Vision Wide machines maintain a single-source core concept, which incorporates all machining processes-from raw material input to final machining-in just one machine. "This is done through specialized machine configurations that offer maximum productivity and improved machining accuracy while reducing production lead times and lowering operating expenses," said the spokesperson.
Single source one-step capabilities include:
- Increased capacity, flexibility and productivity
- Improved machining accuracy and overall part quality
- Streamlined production and boosted output with fewer machines
- Maximized use of shop floor space
- Enhanced overall management and enabled production of parts on-demand
- Reduced part costs from fewer fixtures and less tooling.
For more information contact:
J2 Machine Tool Group
24688 US Highway 322
Cochranton, PA 16314
814-807-2113
sales@j2machinegroup.com
www.j2machinegroup.com
< back