
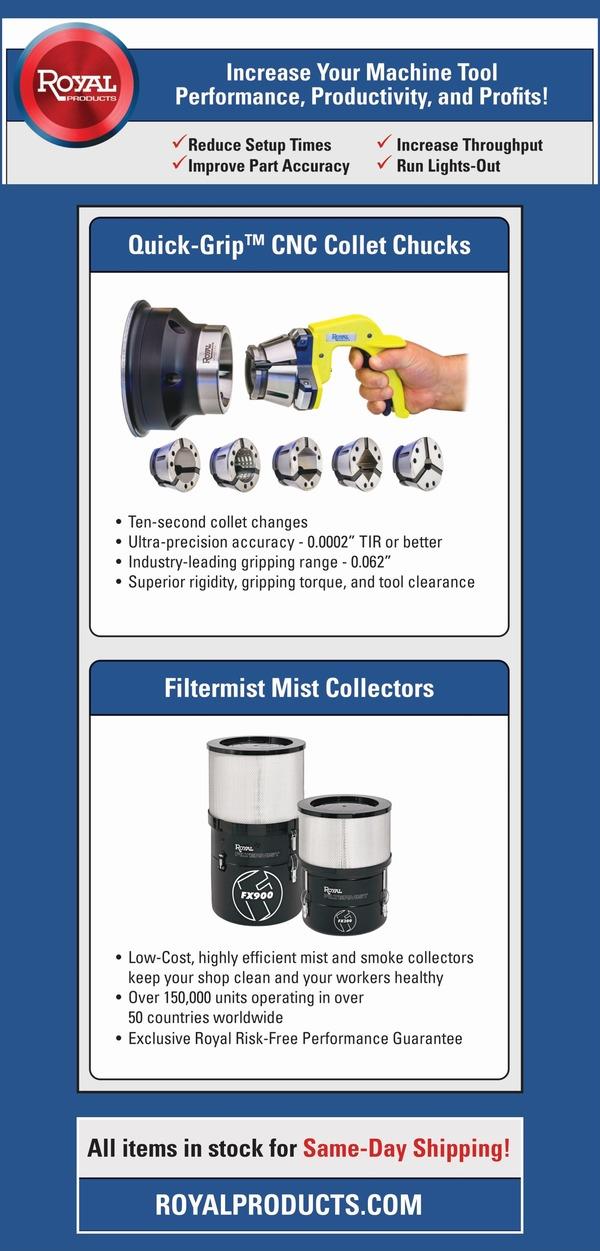
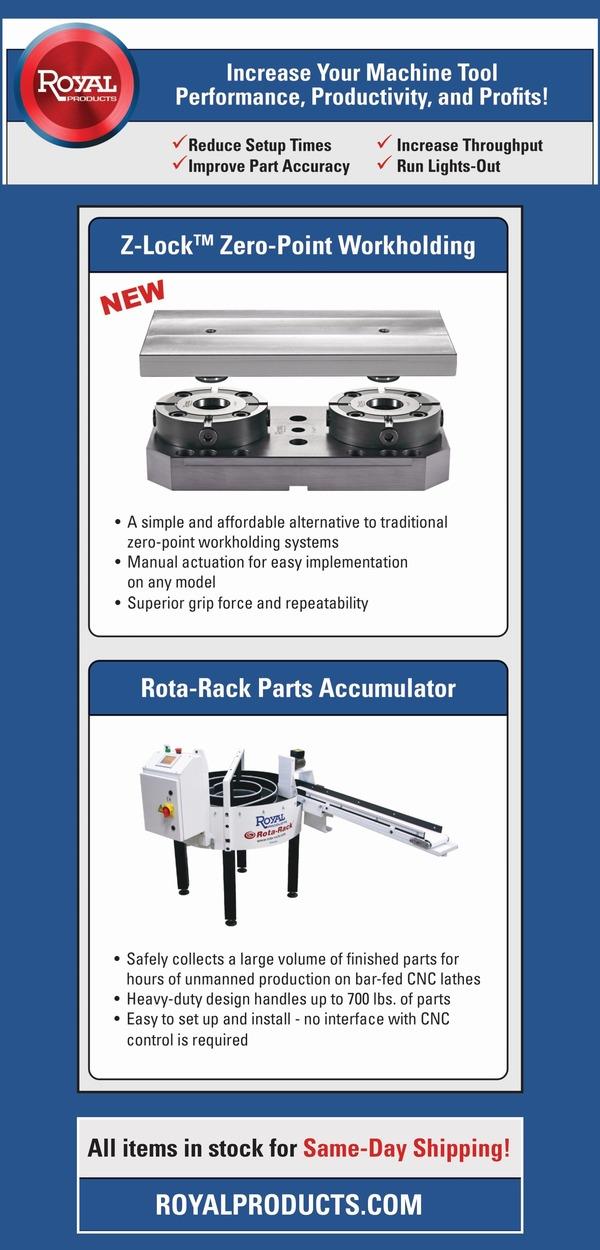

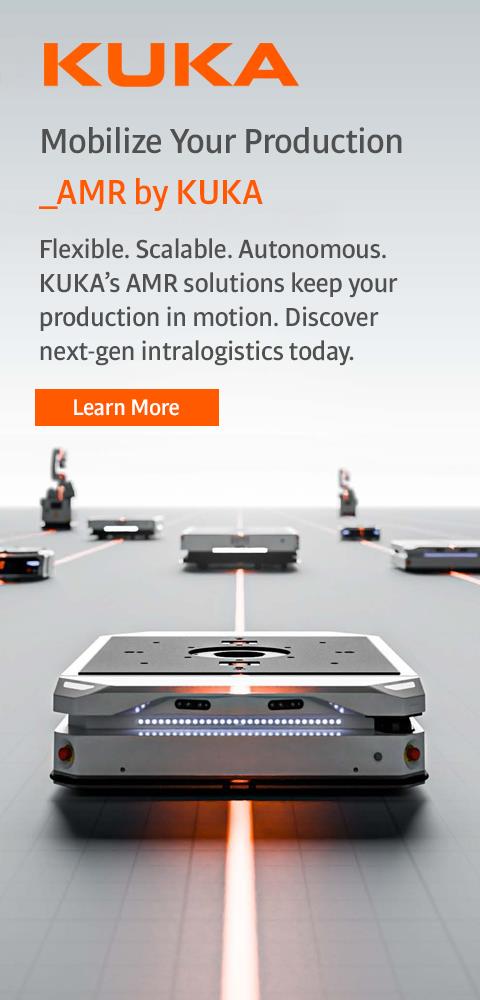
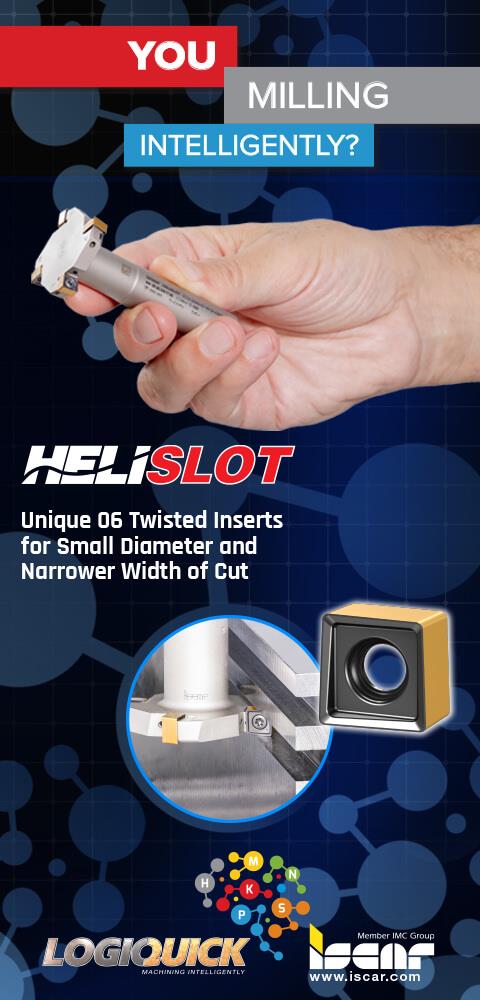
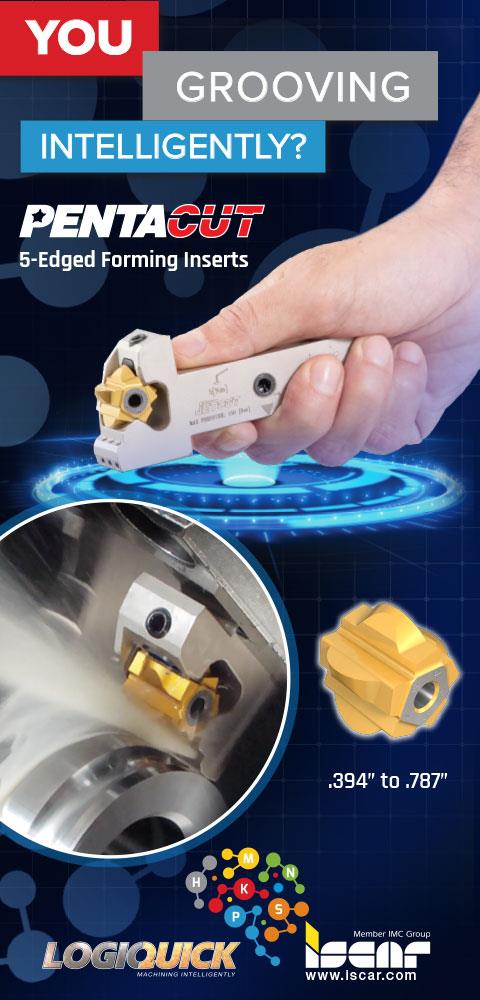
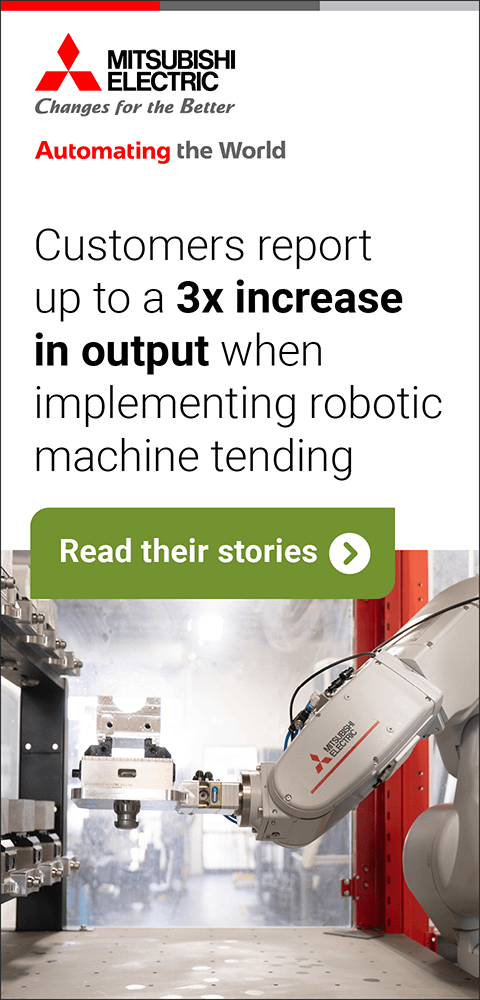
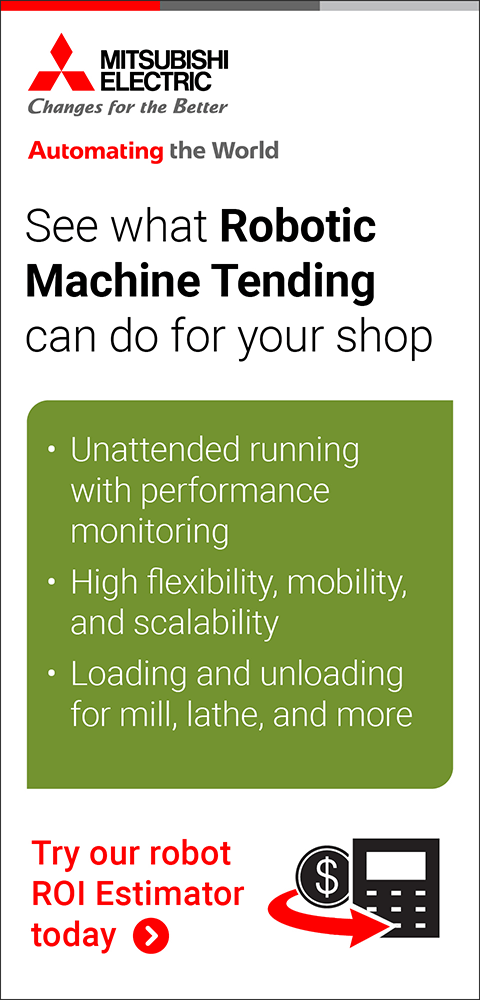
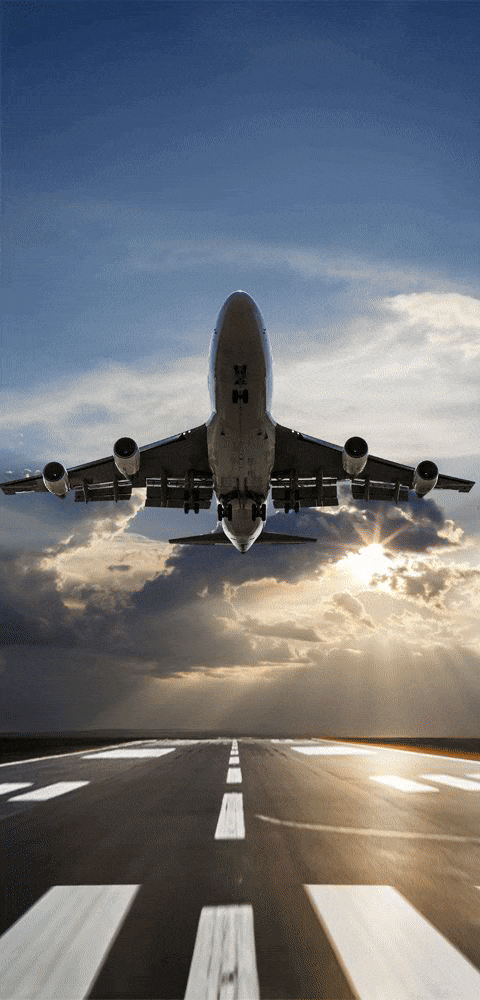
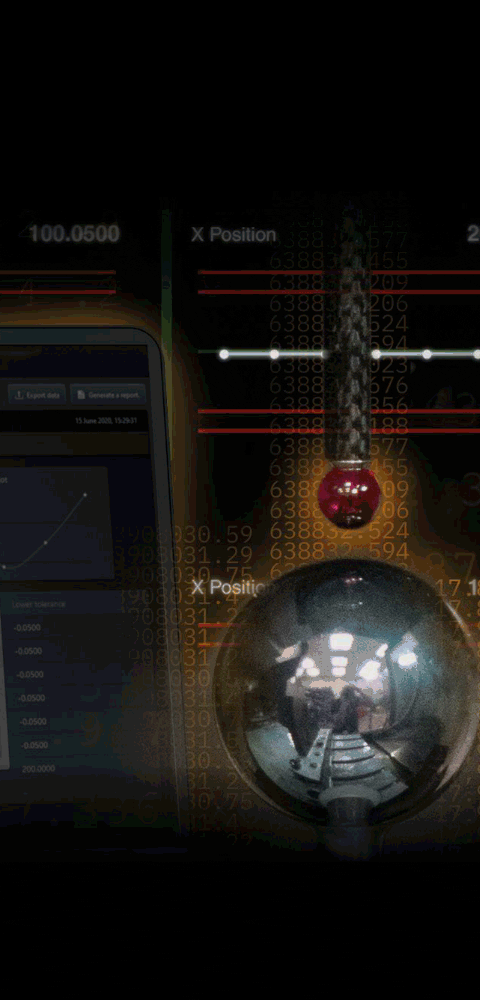
Solution for Chucked Components in Transmission and Engine Production
August 1, 2020
"What will the cars on our streets look like in the future? A new study by the Boston Consulting Group forecasts a mix of gasoline and diesel engines (48%), hybrid vehicles (33%) and all-electric drives (19%)," said an EMAG spokesperson. "As for OEMs and supply companies, this means that both conventional components, such as transmission gears, and many new transmission components will be produced in the future-in alternation and under considerable cost pressure. A look at the EMAG VLC 350 GT turning/grinding machine reveals how this challenging task can be implemented efficiently in production: different hard machining processes are performed on chucked components with a diameter of up to 350 mm in succession and in a single clamping operation. Users benefit from a flexible solution with an excellent price-performance ratio."
"Large output quantities, precise machining processes and massive cost pressure-the requirements in transmission manufacturing are high and will continue to rise in the future as ongoing changes in the automotive industry affect this area in particular," continued the spokesperson. "A significantly greater number of transmission variants will have to be manufactured in the future. How can this challenge be met? EMAG provides an answer with its VLC GT series."
The "GT" in the product designation stands for "grinding" and "turning." The combination of grinding and turning (and additional processes) with pick-up automation from EMAG allows for a variety of manufacturing solutions. This enables it to cover the entire range of machining operations required for transmission components.
EMAG is now introducing the VLC 350 GT machine to the market. It is larger than the VLC 200 GT and therefore designed for components of up to 350 mm in diameter. For the first time, it offers the option of integrating a grinding spindle with an NC swiveling axis. This can hold, for example, a cylindrical grinding element for grinding internal bore holes. What is the overall strategy behind this new development? "Among other things, we are aiming at manufacturing processes with smaller batch sizes that inevitably involve many retooling processes," explained Marina Manger, EMAG Sales. "In these applications, the fact that the machine includes several different grinding spindles from the outset is an obvious advantage. The machining area also provides plenty of space. The machine is ready to handle any task."
From Traditional Gearwheels to Chucked Components with Internal Taper
The VLC 350 GT enables traditional hard machining of gear wheels-from hard turning of end faces to pre-turning of the bore hole and outer synchronizing taper to finish grinding of these contours-as well as of many other chucked components with internal taper.
For the latter, the internal grinding spindle with NC swiveling axis offers benefits:
- End face turning: Loading and subsequent unloading is performed at high speed with a pick-up spindle. The machining operation starts with hard turning of the end faces.
- Contour turning: Depending on the component geometry, inner contours (with one or two tapers), a cylindrical bore hole and the outer synchronizing taper can be pre-turned in the second step.
- Inner contour grinding: The use of a cylindrical grinding element on the swiveling NC axis makes it possible to machine various internal taper angles. To do this, the grinding spindle is precisely swiveled to the required angle in each case. Any required bore holes are also completed in this way (with a zero-degree grinding angle).
- Outer counter grinding: The final operation consists of grinding the outer synchronizing taper with the external grinding spindle.
"If a customer wants to machine a wide range of parts with many different bore holes, we can also integrate two internal grinding spindles in the VLC 350 GT," said Marina Manger. "The reason for this is that smaller bore holes require the grinding element to operate at higher speeds, while large bore hole diameters instead require a lower speed. In certain circumstances, this cannot be achieved with a single grinding spindle."
Shorter Cycle Times-Decreasing Tool Costs
"In addition, it is of fundamental importance that the combined machining operation consisting of (hard) turning and grinding ensures fast processes and high machining quality: the residual machining allowance after turning is only a few millimeters," said the spokesperson. "The grinding process with corundum or CBN grinding wheels is significantly shorter. Considering the low residual machining allowance, the specification of the grinding wheel can also be geared more specifically toward final quality. An integrated measuring probe checks the diameter and length of the component after the process. In addition, a linear motor in the X-axis ensures short chip-to-chip times, because it moves the components to the machining position particularly fast."
Flexible Configuration for Many Solutions
Altogether, there are many possible applications for the VLC 350 GT in regards to the desired production volume, for example, as Marina Manger noted: "Owing to its performance, the machine is particularly recommended for medium and high-volume production. Its ease of tooling, including two large doors and accessible tools, as well as its flexibility in terms of configuration, as mentioned above, nevertheless also make it interesting for small batch sizes with frequently changing production tasks." At the same time, the machine can be loaded manually or integrated in production lines.
For more information contact:
EMAG L.L.C.
38800 Grand River Ave.
Farmington Hills, MI 48335
248-996-4703
www.emag.com
< back