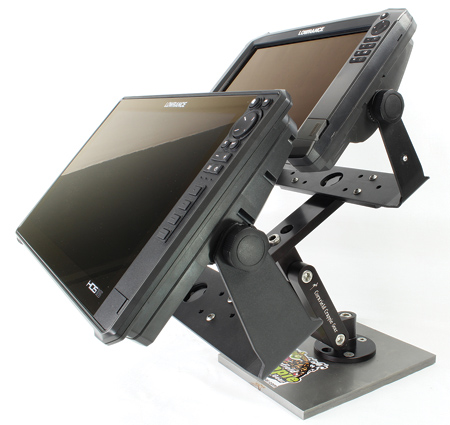
Double monitor mount
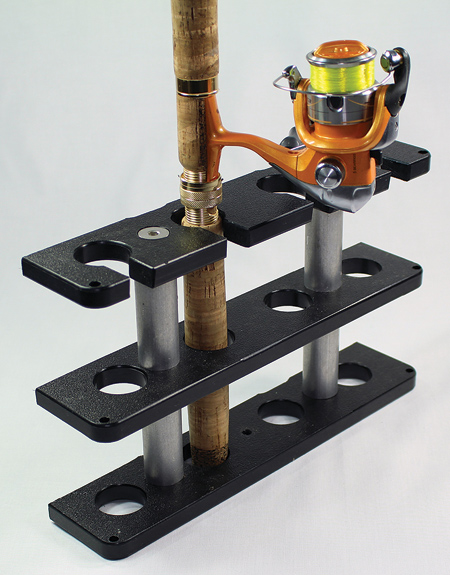
The 4-Rod Launch Pad works in tandem with the Cable-Save'R for more efficient crappie fishing.
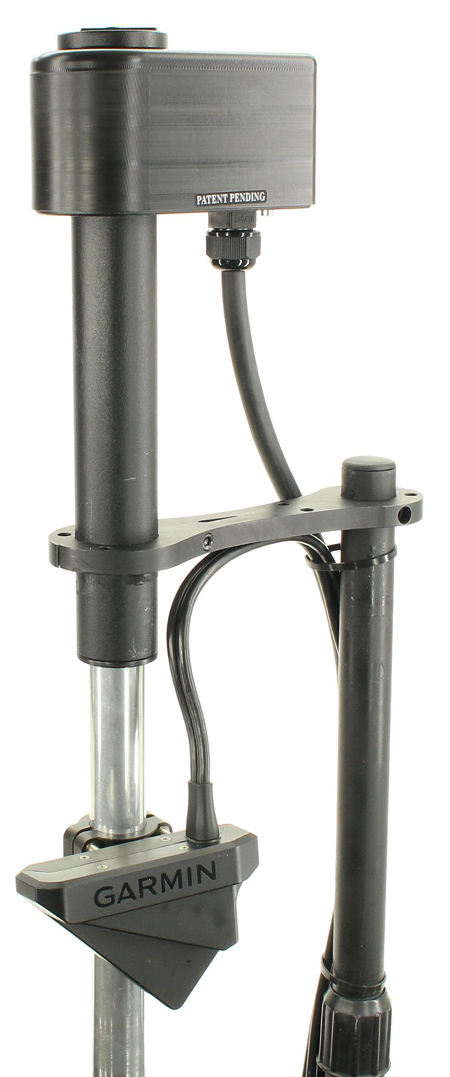
The Live Sweep "Remote Scope" is a 12 V powered sweeping arm that allows for 300° of adjustment to move a livescope head.
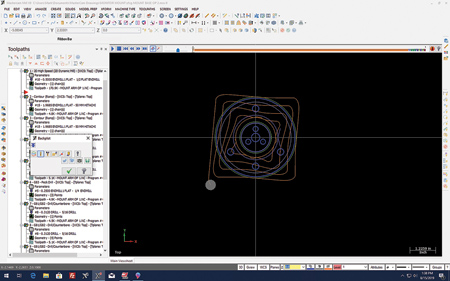
The monitor base is programmed using 2D Dynamic milling toolpaths and verified using Backplot.
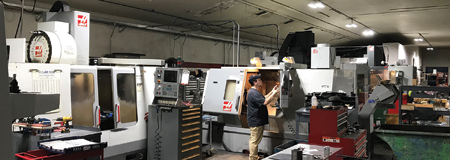
PTA has five 3-axis vertical mills-one with extra travel (60" in X), and all with fourth axis available-an indexing head and a trunnion table. They have one seat of Mastercam 2020 3D Mill to program them all.
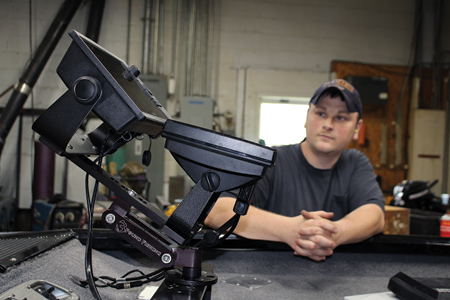
Nate Carter with a 3 lb. double monitor mount
Mark Ridl, owner and President of Production Tooling & Automation (PTA), has been an avid crappie fisherman as far back as he can remember. He balanced the demands of his busy machine shop with the calm of fishing excursions, realizing he could make or improve upon his existing fishing equipment himself. When PTA experienced a brief slow-down in its manufacturing operation, Ridl turned to his leisure time passion to keep the machines running. Six years later, his company is experiencing an unprecedented surge in orders from Texas, Louisiana and Florida. It is all about "Cornfield Crappie Gear," Ridl's name brand for boat accessories that can be invaluable when fishing for crappie, a type of freshwater fish native to North America. The products include Monitor Mounts, the Cable-Save'R, trolling racks and drift paddles.
"Every morning when we come in, we have orders waiting for us," said Ridl. "We are shipping Crappie Gear all over the country, to Sweden, to New Zealand-basically, all over the world."
But making fishing gear is not the company's only line of work. In fact, until recently, it was small and secondary to what PTA did when Ridl started the company in 1997.
Ridl began working as a machinist more than 30 years ago. In 1988, he purchased a Bridgeport milling machine, and, in his own garage, he made parts for his personal pursuits, like his old '34 Ford street rod pickup. In 1997, he quit what he calls "a perfectly good job" and, in the middle of the cornfields of Hoopeston, IL, started PTA.
The company had only manual machines before Ridl added a couple of used CNCs. At the time, he was writing programs by hand on a legal pad. Over the years, the company grew, and he bought a used Haas milling machine. At that point, he knew he would have to add programming software. In 2002, Ridl reached out to Mastercam CAD/CAM software reseller ShopWare, Inc. and purchased 2D milling and Mastercam lathe software. According to Ridl, installing the software not only made a huge improvement in PTA's productivity and efficiency, but the move vastly expanded the jobs on which his company could bid.
Business remained steady for the next several years. In 2011, PTA landed a big job from a customer in the automotive industry with contracts from Ford and General Motors for forging dies for crankshafts. Ridl knew he would need to upgrade his CAD/CAM software to 3D.
"Once again, ShopWare helped with the upgrade and gave us some of the best technical support you could ask for," Ridl said. "With their help, we tackled the programming for the first die block job."
But once up and running, Ridl encountered a huge challenge with the material being provided for the die blocks by a company in Germany. It was incredibly hard and heavy. Called CR7V, the material was a proprietary composition.
"We were running a set of arms that are fork jaws for forging that picks up the hot orange billet," Ridl recalled. "They were just 4140 PH, but we were going around them with 50 mm face mill. There were a lot of angles and a V-shaped jaw that grabs the hot part. We were tearing up tooling, tearing up inserts and, sometimes, wrecking one of the face mill heads. We were ramping down to remove as much material as we could in order to get the shape we wanted. Then we would come back with a 1/2 inch carbide end mill and go in and finish the rest of it. One day, we went through $500 worth of drills trying to figure out how to tap a hole in this stuff. Plus, it took us an hour to make one part."
Then one day, Ridl and Nate Carter, his lead machinist, decided to explore using the software's Dynamic Motion toolpaths to run the part. Dynamic Motion, or Dynamic Milling, uses proprietary algorithms programmed into the software to keep the tool constantly engaged with the material, allowing it to cut intricate geometries at higher speeds. They kept trying different speeds and feeds until they finally figured it out.
"Now we run the same part with a 1/2 inch carbide end mill. We went from just over an hour to 38 minutes to make a part. We run one end mill to do all of it, and we run multiple parts on that same end mill," he noted. "Before, we changed inserts for every part-sometimes in the middle of the part. We maybe got one or two parts per end mill on the finishing. Now, we run 16 at a time. In fact, we now use the same end mill to rough and finish. We can run eight to 10 parts before changing an end mill using ordinary grit carbide."
Ridl reported that PTA is now using the software's Dynamic Milling feature for much of their work.
"It is just unbelievable how fast you can run hard materials, soft materials-it does not matter," Ridl said. "Whatever you have, Mastercam makes it easy. If I am honest, Mastercam is a big part of our success in accomplishing basic 3D machining."
In 2014, with the lion's share of its business coming from the automotive industry, one of PTA's customers lost an automotive contract. The shop began to struggle. "We went from feeling like we were on top of the world to, all of a sudden, things drying up," Ridl recalled.
With his machines quieted down, a restless Ridl went back to something he knew: crappie fishing. He began making one-off pieces for himself and his fishing boat. Before long, his friends saw the custom brackets and rod racks, and they wanted some too.
"Pretty soon, it became a decent little side business," Ridl said. He called the products Cornfield Crappie Gear "because we were in the middle of the cornfields of east central Illinois making gear for crappie fishing."
Over the next year or two, word spread and demand and orders for crappie fishing gear came rolling in. Business improved to the point where Ridl and his wife considered a permanent move 300 miles south to their vacation home on Kentucky Lake where Ridl had been doing most of his crappie fishing. In the spring of 2017, Ridl bought a building and, that fall, he moved his home, his machining company and his lead machinist to Gilbertsville, KY.
Cornfield Crappie Gear products have come a long way since Ridl's one-offs. The premier product was a monitor mount, an arm/bracket that holds an electronic monitoring unit (like a GPS unit) in place and, at the same time, is adjustable so it can be viewed from different angles. For multiple unit applications, CFCG offers a double-mount product that, according to Ridl, is "a very hot seller."
But by far, Crappie Gear's number-one seller is the patented Cable Save'R. Ridl designed it to solve a problem he had running the wires from the electronics box in the boat to the transducer. The cable would often get caught or tangled in the trolling motor and ruin the cable. Cable Save'R is offered in six different models for use with a variety of trolling motors.
CFCG also offers drift paddles (two pieces of ABS plastic on an aluminum frame), Crappie Gear Rod Racks made from 6061 aluminum and UV-resistant seaboard plastic for transporting up to 10 rods, and Trolling Racks that keep fishing rods in place at the front of the boat for trolling.
Ridl is working with Garmin, the electronic location products manufacturer, as that company expands into the freshwater fishing market. Crappie Gear offers a mount that can be used with Garmin's Panoptix LiveScope transducer, described by Ridl as "the hottest thing in fishing. It actually lets you see the fish swimming-in real time-in the water. You can even see your bait, and the fish going to look at your bait. We have probably sold more than 200 of these mounts in the last month and a half."
In addition to Garmin, CFCG is working with Hummingbird, another maker of electronic monitoring units, and with Minn Kota, a company that makes trolling motors.
"Crappie Gear has just exploded. We are sponsoring a crappie fishing promoter group called `Three Pound Fishing,' guys who have a YouTube Channel who just produced a Cornfield Crappie Gear video for us. We have gotten an unbelievable response from the video," Ridl said.
Today, PTA has five 3-axis vertical mills-one with extra travel (60" in X), and all with fourth axis available-an indexing head and a trunnion table. They have one seat of Mastercam 2020 3D Mill to program them all. Ridl estimates that, at this point, Cornfield Crappie Gear represents about 50% of PTA's business, and they are also doing an increasing amount of prototype work. However, he said the company continues to serve other industries, including long-time customers like Quaker Oats. For the past 20 years, PTA has been making replacement parts for Quaker Oats' production line equipment used to make its "Chewy" granola bar. PTA also does work for a customer that manufactures mass mailing equipment and machinery for bookbinding and book packaging.
"Can we do close tolerance work? Sure. But we do not do it all that often," he said. "In our day-to-day production, especially with the Crappie Gear, the focus is on the cosmetics of the product-it has to look good. Look, we are a small mom and pop shop. Always have been, and all I am ever planning to be. I am happy with that. We have the capability to do more. For now, it is good to know that we could just do about anything we want to do-just sit down at the computer and draw it up, program it with Mastercam, throw it in a mill and we are rolling."
Ridl continued, "As far as Cornfield Crappie Gear is concerned, we have our own brand of products with a great reputation, we have our own website on the internet, and we are on FaceBook and Instagram. We have dealers, outfitters, business connections and users worldwide. It is just amazing what we are doing, and we have no plans to stop."
For more information contact:
Cornfield Crappie Gear
217-304-1680
www.cornfieldcrappiegear.com
CNC Software, Inc.
671 Old Post Road
Tolland, CT 06084
800-228-2877
info@mastercam.com
www.mastercam.com
SOUTHEAST ONLY
CAD/CAM Solutions, Inc.
2336 Wisteria Drive, Ste. 520
Snellville, GA 30078
770-982-3400
www.cadcamsolutions.com