
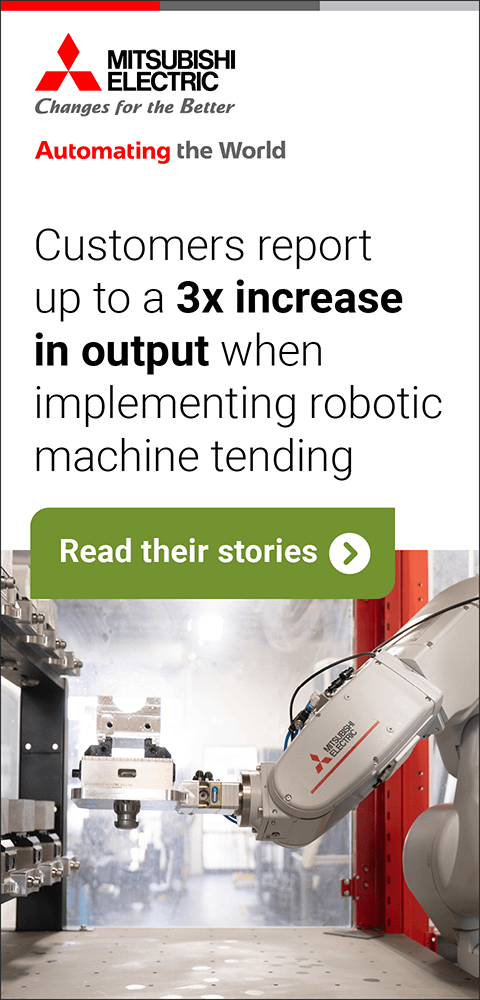
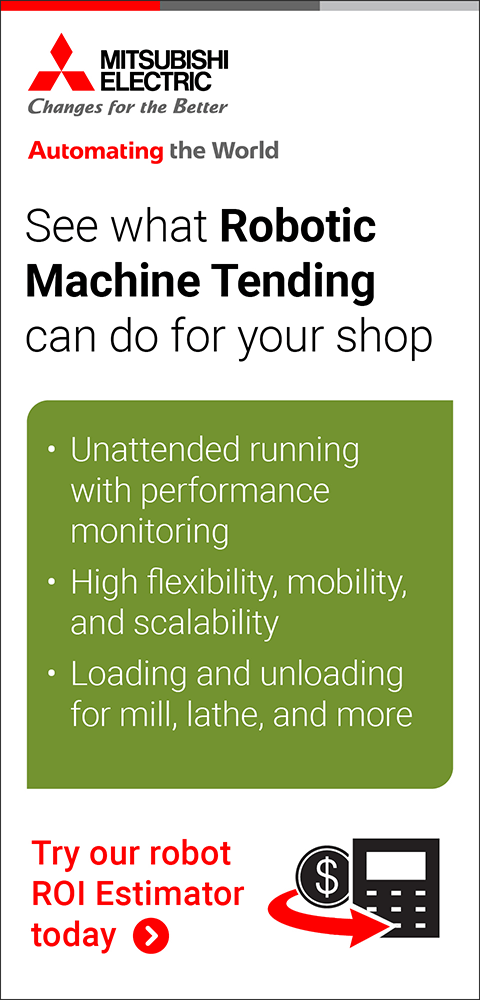
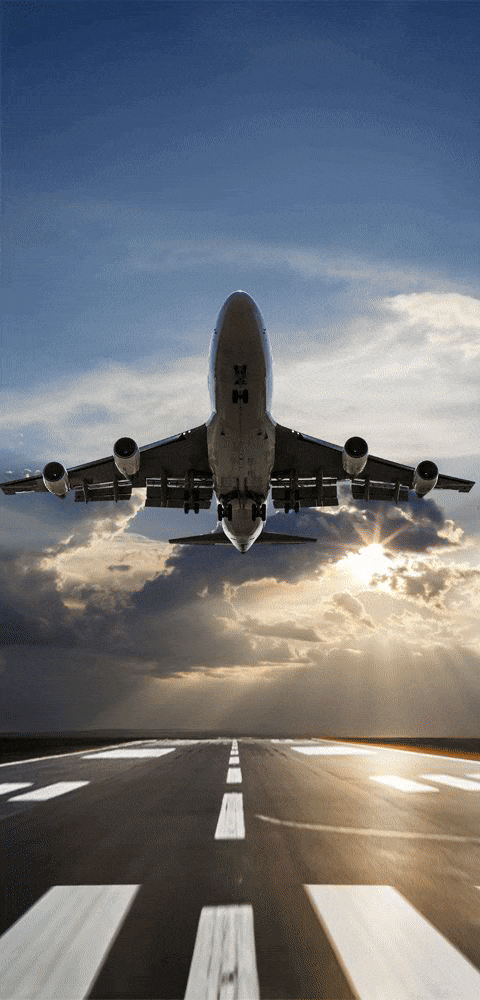
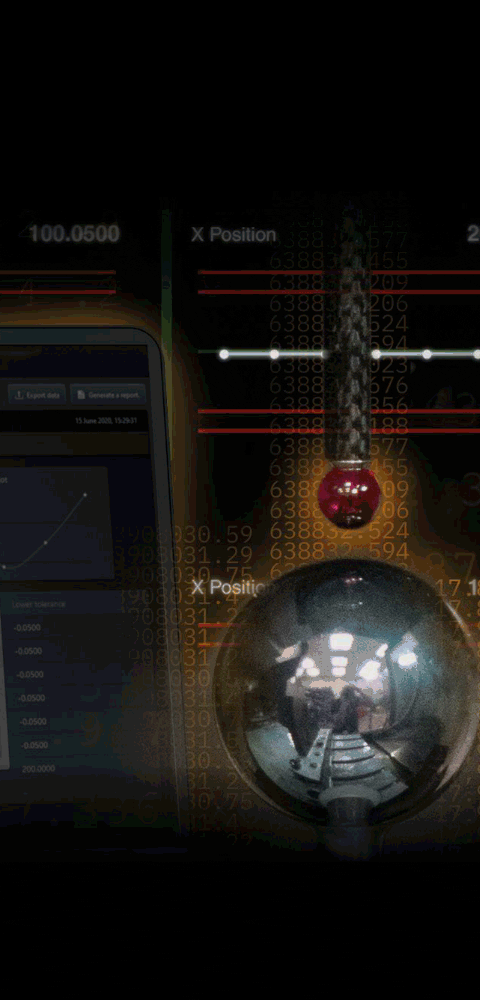
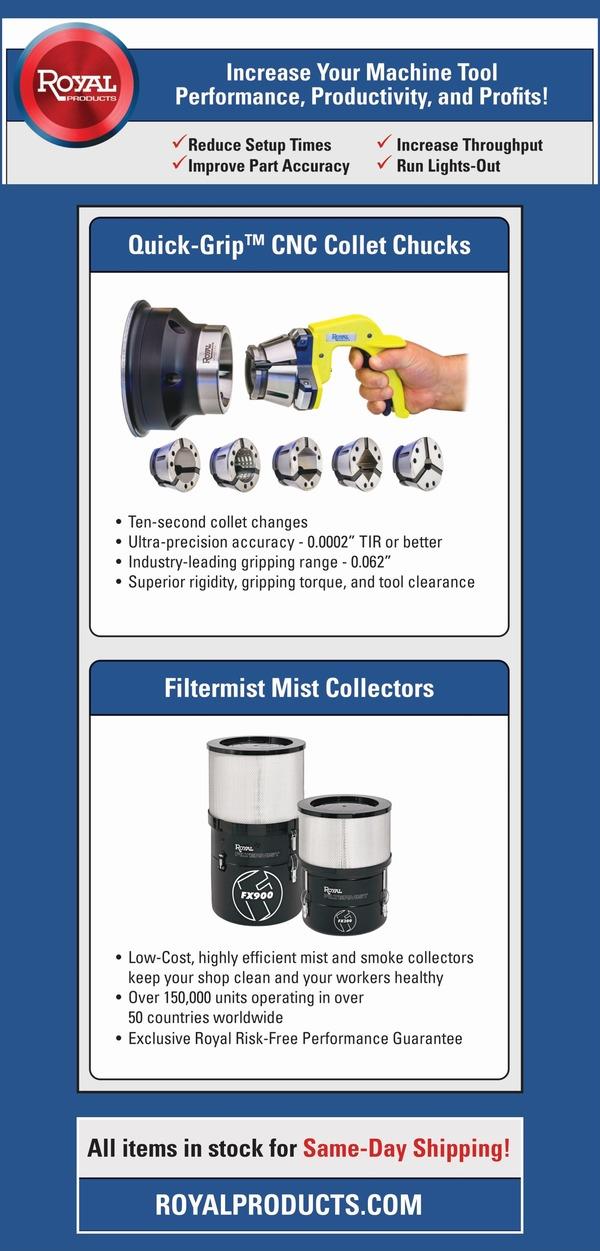
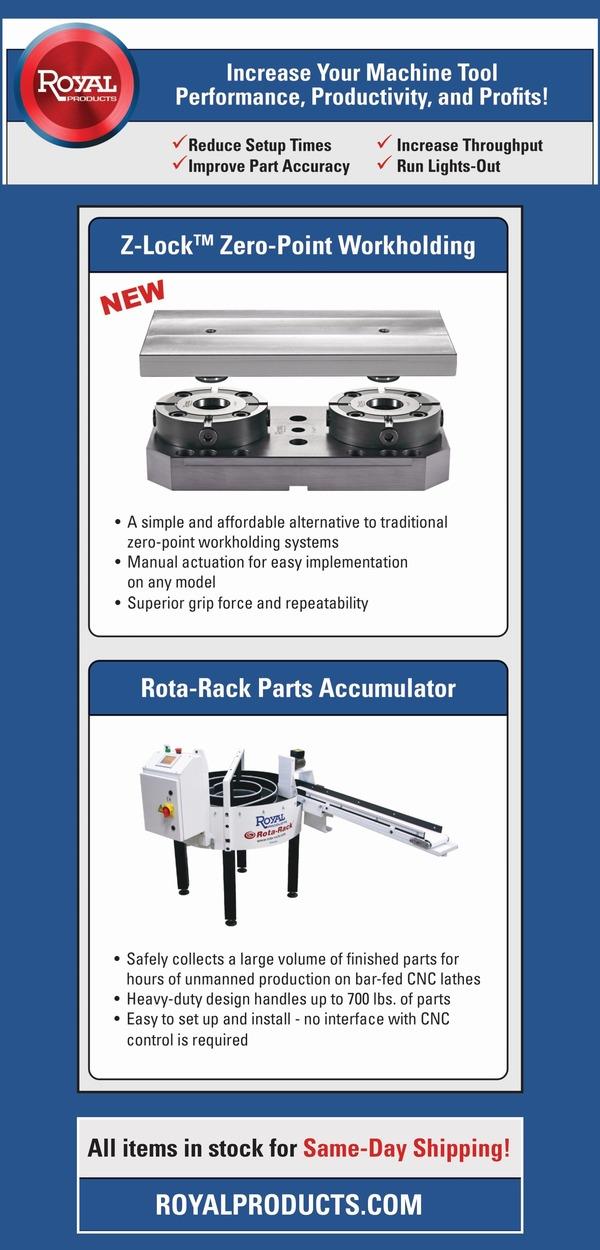

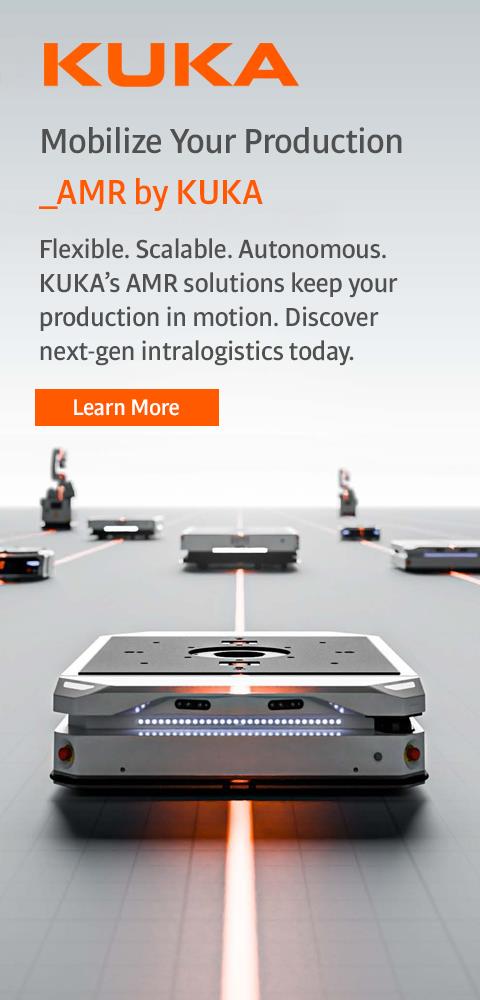
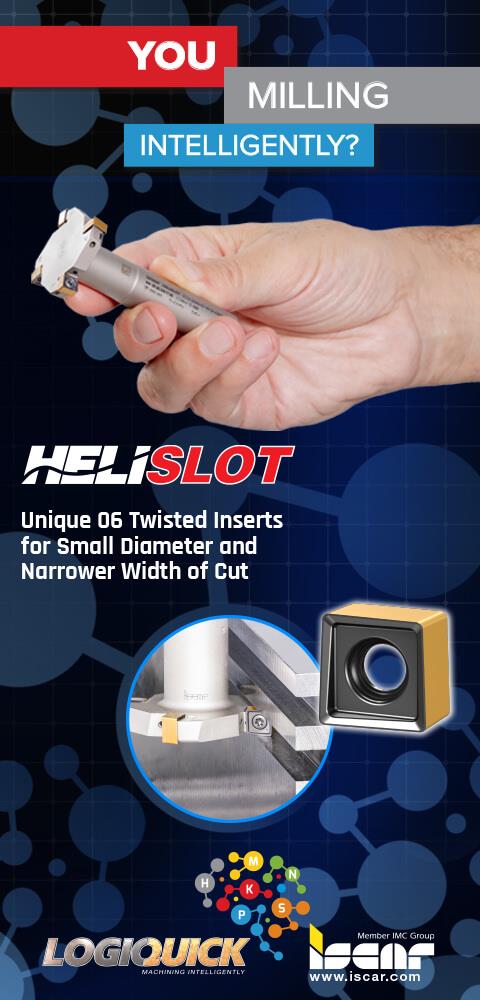
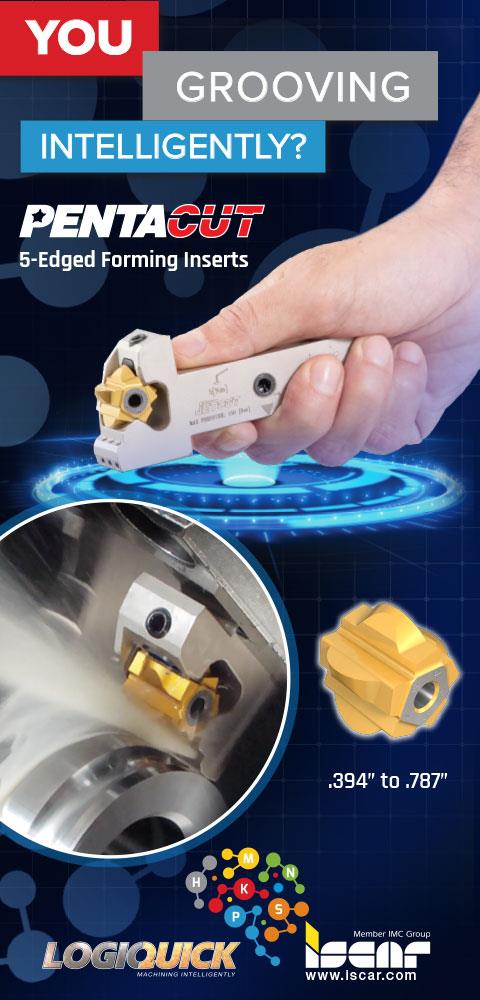
New Generation Control Offers Forward-Looking Technology
August 1, 2020
"HEIDENHAIN is bringing to market the new Gen 3 version of its high-end TNC 640 control for machine manufacturers and end users looking for forward-thinking manufacturing capabilities," said a company spokesperson. This control is designed for machines ranging from 3-axis milling to 5-axis simultaneous machining with milling, turning and grinding operations and up to 24 axes.
"With its new Gen 3 drives, HEIDENHAIN's TNC 640 features powerful inverters and controller technology that are key components in the complete system of its control package," said the spokesperson. "Now providing even higher spindle and axis dynamics during the manufacturing process, these drives also require less space in its electrical cabinet and result in reduced storage, mounting costs and servicing time."
With Gen 3 drives serving as the new system foundation, the new TNC 640 offers high availability and surface quality with shortened machining times, as well as any other upcoming path-breaking functions of HEIDENHAIN controls.
Highlights of this latest generation TNC 640 control include new jig grinding functions, Extended Workspace Compact, Optimized Contour Milling (OCM) within its Dynamic Efficiency package, as well as the ongoing option of a Dynamic Precision package. Also, HEIDENHAIN's new StateMonitor 1.3 makes it easy to remotely monitor efficiency improvements and ROI of these new CNC functions.
Highlights of the TNC 640 Gen 3 control functions include:
- Functions for grinding operations-The TNC 640 now supports jig grinding and dressing of grinding tools. In addition, it can superimpose the tool axis with an optional reciprocating stroke, which is necessary for many grinding applications.
- Extended Workspace Compact-The new 24" wide screen features a divided screen for two work areas, allowing users to display additional applications alongside the control screen. The integration of HTML5 applications as well as capabilities for displaying cameras in the work envelope have been added.
- OCM/Dynamic Efficiency-The term "Dynamic Efficiency" encompasses HEIDENHAIN TNC package functions that result in significant improvements in heavy machining. The new Optimized Contour Milling (OCM) expands the trochoidal milling method in this package to include any pocket shape and island. It allows for the use of high cutting values without overloading the tool and can be programmed directly on the control. "Compared with conventional machining, OCM allows workpieces to be manufactured at up to 3x faster and with 2/3 reduction in tool wear," said the spokesperson.
- Dynamic Precision-The term "Dynamic Precision" encompasses HEIDENHAIN TNC functions that significantly improve the contouring accuracy of machine tools, even with high feedrates and complex contour paths. This is available on Gen 3.
For more information contact:
HEIDENHAIN Corporation
333 E. State Parkway
Schaumburg, IL 60173-5337
847-490-1191
www.heidenhain.us
< back