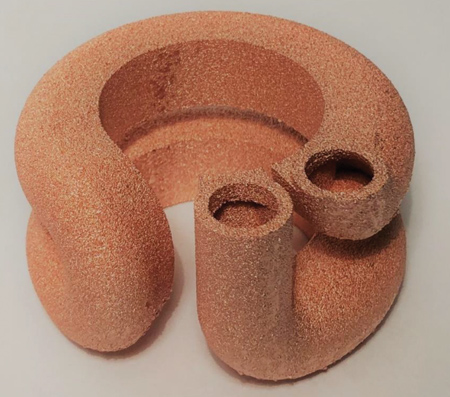
GE Additive Arcam EBM-pure copper induction coil
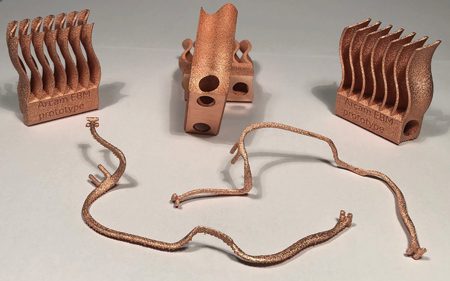
GE Additive Arcam EBM-pure copper parts
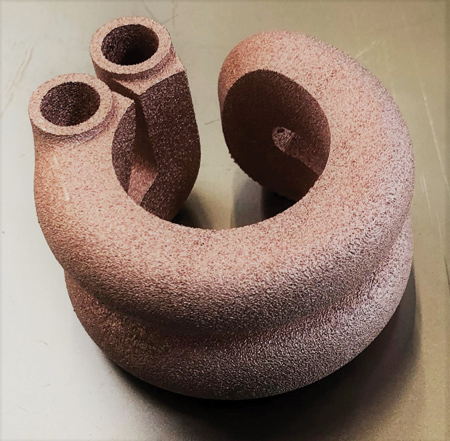
GE Arcam EBM pure copper induction coil close up
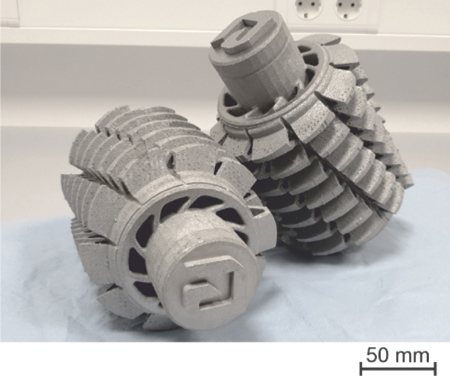
GE Additive Arcam EBM-tool steel parts
GE Additive Arcam offers development material (D-material) support for pure copper and highly alloyed tool steel. According to the company, this collaborative approach further unlocks the potential of electron beam melting (EBM).
Offered to all customers as a general release on both pure copper and tool steel, a D-material describes the maturity of process parameters for a specific material of family of materials. D-materials meet mechanical requirements for test bars on a limited build envelope to relevant industrial standards.
Obtaining the same properties for complex geometries requires additional development, resulting in an industrialized material (I-material) with process parameters optimized for production on specific customer applications with mechanical and chemical properties.
"This general release of D-material support for pure copper and tool steel is an exciting development and opens up EBM to a wider range of industries and applications. We have opted to take an open, collaborative approach and will review feedback from customers using the D-material, and gauge their long-term interest, before considering how we approach industrializing the materials," said Karl Lindblom, General Manager, Arcam EBM.
Benefits of Pure Copper and EBM
"EBM can be used to produce electrically pure copper in geometries that would not otherwise be possible with traditional manufacturing," said a company spokesperson. "The ability to produce novel geometries allows for the removal of process steps, such as soldering, joining or bending, where each of these steps compromises the conductivity, and possibly the lifetime, of the component. The result is a higher performance component at reasonable cost."
Copper's ability to absorb energy varies with the wavelength of the energy source. "Pure copper absorbs 80% of the energy from an electron beam, compared to only 2% of the energy from a red laser beam. This provides EBM with an advantage in terms of the ability to melt and ultimately productivity gains," said the spokesperson.
The vacuum environment in which EBM operates minimizes the oxygen pick-up in copper, allowing for high conductivity copper to be produced. Oxygen reduces the conductivity of copper, while also embrittling the component.
"Other additive manufacturing (AM) techniques increase productivity in copper production through the addition of alloying elements. Adding alloying elements decreases copper's ability to conduct," noted the spokesperson. "Compared to other AM techniques, only EBM can provide the combination of geometrical freedom, high productivity and high conductivity. While other technology providers claim to have copper processes, these are inevitably alloyed to improve laser absorption and productivity and cannot reach the same purity, and thereby conductivity, as EBM."
The ability to produce unique, complex geometries in pure copper without compromising the high electrical or thermal conductivity is suited to a range of sectors, including the automotive industry, or customers looking at applications for electrical connectors, induction coils and heat exchangers, the company noted.
Benefits of Tool Steel and EBM
"EBM is the only commercial available technology for AM of crack prone alloys," said the spokesperson. "Higher levels of carbon in the steel mix increase the material's propensity to crack during production with large temperature gradients. This makes high carbon level steels unsuitable for AM process with cold ambient temperatures such as laser powder bed fusion (PBF).
"EBM technology can process high crack-prone alloys due to high build temperature and achieve the design complexity, which cannot be achieved with conventional production processes. The EBM's vacuum environment is perfect for material protection and mitigates the introduction of impurities."
The Arcam EBM Spectra H system is especially suited for materials that require hot processes because of their crack prone nature while also having a large build volume capable of stacking many parts per build and high power, increasing productivity. "This results in a significant reduction of process steps going from powder to complex part, in both product development and the production process," said the spokesperson.
For more information contact:
GE Additive
www.ge.com/additive