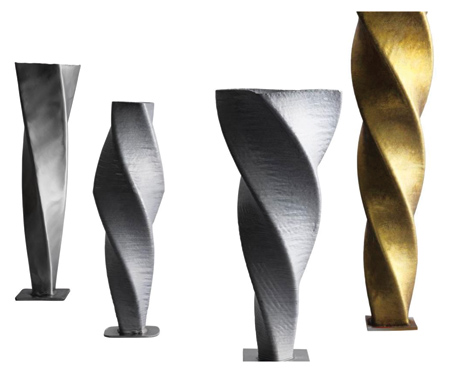
Different filler metals can be used for WAAM, such as steel, aluminum, chrome-nickel steel or bronze.
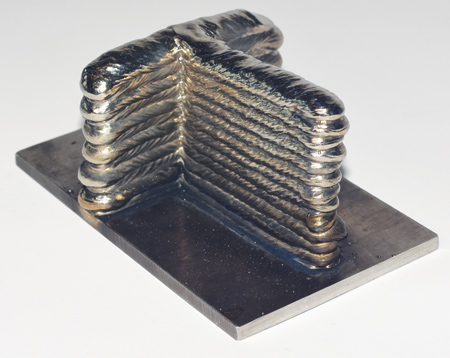
With wire arc AM, components are "welded up" layer by layer before being mechanically reworked. In the example here, a component is being produced from titanium.
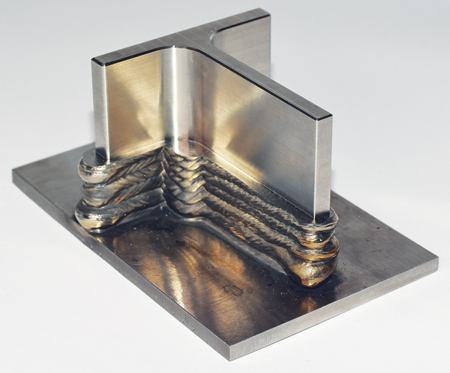
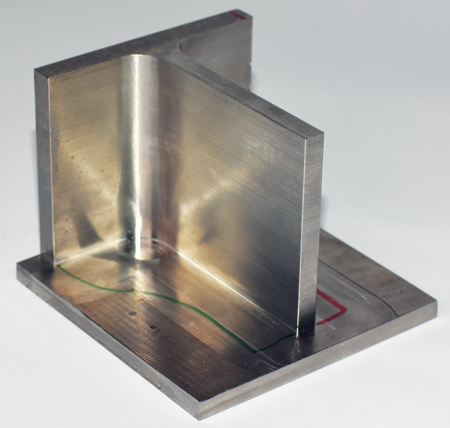
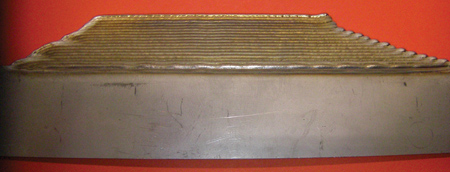
"Milling thin fan impellers from nickel-based alloys for the electronics industry is an expensive business, while casting is rarely an option. WAAM is an economical alternative," said a company spokesperson.
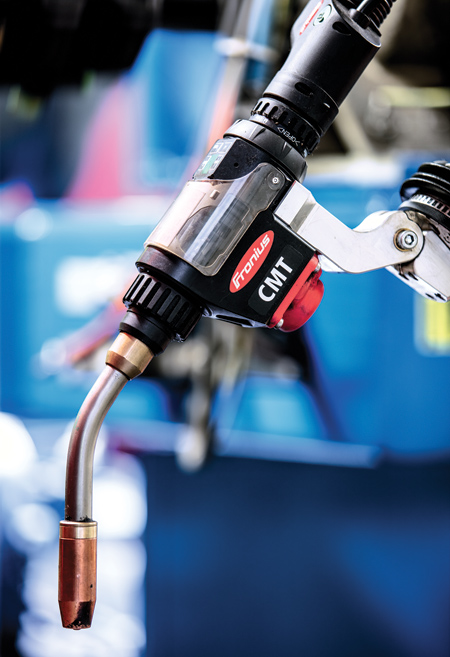
"The key factors determining the quality of a component produced using WAAM are the stability of the welding process and low heat input-the Cold Metal Transfer GMAW process from Fronius fulfills these requirements," said a company spokesperson.
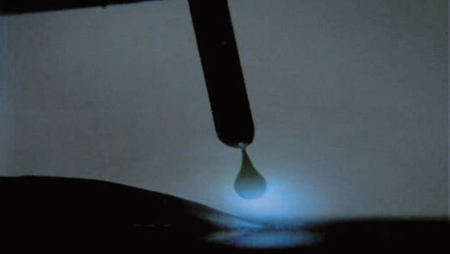
The reversible wire electrode used in the CMT welding process mechanically supports droplet detachment. This means that less energy is needed and long short circuit times are achieved-for a "cold" welding process.
Additive production methods generate components by building up material layer by layer. "The most well-known example of an additive method is 3D printing," said a Fronius spokesperson. "WAAM, which is based on the arc welding process, also produces metal parts layer by layer, with the layers formed by the melting wire electrode. This generative method is particularly advantageous when complex component geometries have to be produced, since the design options are virtually limitless. In addition, parts can be manufactured at low cost and extremely quickly-which makes WAAM a very attractive option for prototype construction and/or small production batches."
What is WAAM?
There are a number of generative production methods for metal. Essentially these can be divided into two fundamental types: powder-based processes and wire-based processes. In powder-based processes, the layers are built up using molten metal powder. "The most common method, the powder bed process, produces extremely precise results, but is somewhat slow in production," said the spokesperson. "Wire-based processes, on the other hand, build up the component by melting a wire-shaped filler metal, requiring the use of a laser, electron beam or arc. These processes have a high deposition rate and therefore help to cut production times."
Wire arc additive manufacturing (AM) is a wire-based process, and uses the gas metal arc welding process (GMAW). "WAAM itself offers a number of advantages besides its high deposition rate of up to 4 kg per hour with steel materials," said the spokesperson. "In the future, multi-wire solutions could give rise to even higher deposition rates. Equipment and material costs are also important criteria, which is another strength of WAAM: all you need is a suitable welding system. There is no requirement for costly special equipment, such as the vacuum chambers needed for the faster electron beam process."
"In comparison to powder-based processes, WAAM benefits from the immediate availability of a range of certified wire types," continued the spokesperson. "There are relatively few powder-based materials to choose from-it can take years to acquire the necessary certification and to produce data sheets, since the use of metal powder is a relatively new technology.
"Cold" Welding Process for Strong Layers
A stable welding process and effective heat dissipation are essential for WAAM. The welding process needs to be sufficiently low energy such that when a new layer is applied, the existing layers do not melt again. In other words, the process needs to be as "cold" as possible. Furthermore, the weld layers need to be continuous, spatter-free and consistent. If any flaws were to occur, these would be replicated in each subsequent layer.
"The CMT GMAW process from Fronius and its process control variants meet these requirements," said the spokesperson. "They produce a stable arc and a controlled short circuit with long short circuit times. This means that the heat input is lower and the material transfer is practically spatter-free, which helps to prevent flaws."
Two process control variants of CMT are particularly suited to WAAM. One is the CMT additive process characteristic, which has been optimized for WAAM. "It achieves high deposition rates while transferring very little heat into the component," said the spokesperson. "The CMT Cycle Step variant reduces the arc power even further through the controlled deactivation of the arc during the process phase. However, this particularly `cold' process does need longer to build up the layers, since the deposition rate is lower."
Real World WAAM Applications
A variety of WAAM components have already been produced using welding technology from Fronius in a variety of sectors. These include fan impellers for the electronics industry, which are made from high-grade materials. "Milling the workpiece is very expensive due to the high rate of material consumption, while casting is not always able to meet the critical metallurgical properties required for walls just 1.5 mm thick," said the spokesperson. "With WAAM based on CMT Cycle Step, these fan impeller blades can be produced from a nickel-based alloy using an additive approach. It is even possible to repair components using WAAM."
Fronius has also implemented another application with a partner in the aviation sector. Titanium is a frequently used material in aircraft construction due to its tensile strength, resilience, corrosion resistance and low weight. "The majority of the components are manufactured using subtractive methods, whereby up to 90% of the material is milled away," said the spokesperson. "This causes high costs, long machining times and costly tool wear. Components produced using WAAM only need reworking to produce a smooth surface. The titanium components produced using the CMT additive process do not exhibit any problems with lack of fusion and have impressive metallurgical properties. Tool costs, machining times and wear can be reduced, meaning that overall machining costs can be brought down. This makes WAAM a cost-effective and flexible alternative for component production. The additive process can be adopted with relative ease using welding technology from Fronius and the CMT solution."
Fronius Perfect Welding Business Unit
Fronius Perfect Welding provides solutions for arc and resistance spot welding and robot-assisted welding. As a systems provider, the Fronius Welding Automation division also implements customized automated complete welding solutions, for the construction of containers or offshore cladding for example. The range is rounded off by power sources for manual applications, welding accessories and a spectrum of services.
For more information contact:
Fronius USA LLC
6797 Fronius Drive
Portage, IN 46368
219-734-5500 / 877-FRONIUS
sales.usa@fronius.com
www.fronius.com