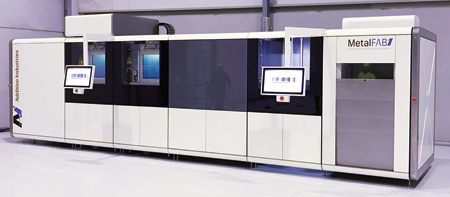
MetalFab1 on the day of installation in ArcelorMittal R&D facilities in Avilés, Spain.
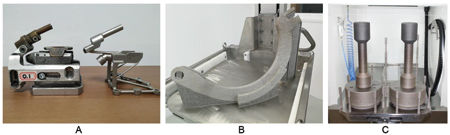
3D-printed spare parts used in ArcelorMittal facilities: Example of part consolidation application with 316L original part on the left and additive manufactured part on the right (A); example of functional large parts with internal lattice structure made with 316L above 500 mm (B); lightweight (hollow) functional spare parts made with Maraging Steel with ArcelorMittal's optimized parameters (C).
Through metal 3D printing, ArcelorMittal has been able to print on-demand ready-to-use spare parts. Collaboration with Additive Industries in recent years has resulted in an improvement in process performance and quality. This outcome has enabled ArcelorMittal to print large and challenging components for its facilities.
"In 2017, ArcelorMittal and Additive Industries joined forces to explore the opportunities of 3D metal printing for the steel industry using one of the largest 4-laser 3D metal printing systems available on the market: the MetalFAB1," said a spokesperson. "3D printing of spare parts is practical because it offers on-demand, on-location production, which reduces the need for stocks. It also shortens the production cycle as well as affording flexibility to ArcelorMittal plants." Since the installation of the first metal 3D printer in ArcelorMittal R&D facilities, several 3D-printed spare parts have already been used while others are still running in ArcelorMittal facilities.
"The MetalFAB1 is a unique metal printer that has automated the manual steps of conventional powder bed fusion (PBF) printers to ensure the highest productivity, resulting in the lowest cost per printed part," said the spokesperson. "At the same time, its build volume (420 mm x 420 mm x 400 mm) enables the production of large steel spare parts for steelmaking or mining operations. The system is designed to be the safest on the market, contributing to ArcelorMittal's focus on operator safety as well as environmental goals since the system recycles all material and generates hardly any production waste."
"Steelmaking operations are usually faced with very challenging and demanding conditions for their spare parts," continued the spokesperson. "During the initial stages, the most challenging aspect faced was to achieve these requirements both for quality as well as for the size of the components, limiting the potential uses of spare parts. The last two years of collaboration have enabled those involved to improve both quality and reliability, as well as an up to fourfold increase in the size of components. Due to this improvement, the number of applications increased from small size part consolidation applications to applications where large, complex, functional and strong parts are required."
Harry Kleijnen, Key Account Manager Additive Industries, said, "We are proud to work together with ArcelorMittal, jointly driving the business case for 3D-printed parts in the steel industry. ArcelorMittal's typical applications have enabled us to further adapt the MetalFAB1 system to print high density, high volume parts. We are looking forward to expanding the range of applications and materials in this intense and strong collaboration".
Daan A.J. Kersten, co-founder and CEO, Additive Industries, added, "ArcelorMittal has helped us to stress-test our MetalFAB1 system for critical spare part production. This enabled us to expand our experience to the steel industry from our main application markets in aerospace and automotive. It has become clear that metal 3D printing is a serious alternative for a large variety of cast parts."
Jose López Fresno, Head of the Additive Manufacturing Department, ArcelorMittal Global R&D, concluded, "Additive Manufacturing is an exponential technology, moving very fast. Our collaboration with Additive Industries is a clear demonstration of our ability to remain at the cutting edge of this technology: we started by printing small specimens and have now progressed to large sized and complex parts."
For more information contact:
Additive Industries North America, Inc.
1250 Avenida Acaso, Unit H
Camarillo, CA 93012
805-427-0019
www.additiveindustries.com