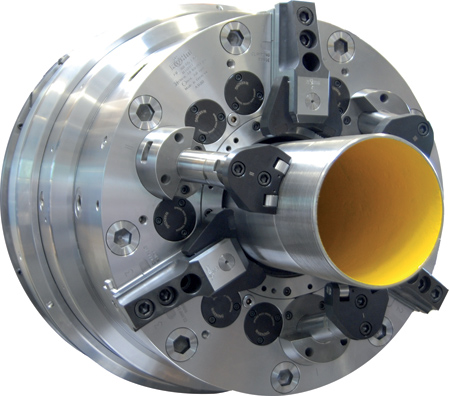
RÖHM LVE pipe chuck for machining the ends of large and long pipes
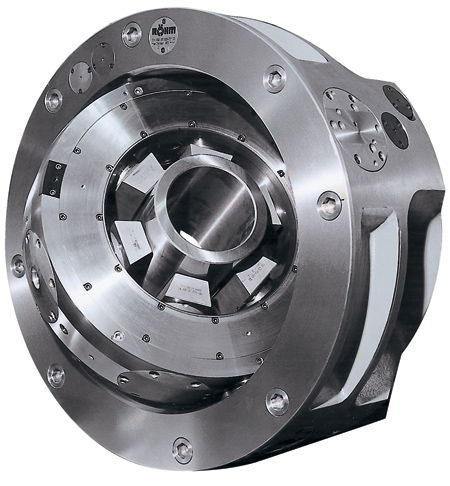
RÖHM HSFZ swivel chuck for machining bushings or connection pieces on both sides
Transformation is nothing new to the oil and gas industry. We all know about hydraulic fracturing, advances in unconventional oil extraction, and other big technological changes that have created new avenues of risk and opportunity in the 21st century. There are also smaller transformations. These transformations may not make the news, but they can have a profound effect on what oil and gas industry companies need to do to survive and thrive in the face of constant uncertainty.
Take the threading of the bent pipes used in upstream extraction, for instance. Historically, American piping companies have used slow, labor intensive, dangerous processes to machine threads. The operator needs to make constant adjustments to keep the pipe on center, which sometimes requires bypassing safety switches and reaching into a machine without doors to shim and re-indicate the pipe over and over again. The operator also runs the constant risk of getting cut by small, stringy chips. Even with a skilled operator and no mishaps, laying threads on a single pipe would take around 15 minutes.
"RÖHM Products of America offers the oil and gas industry timely, relevant solutions," said a company spokesperson. "These solutions answer some of the most pressing challenges faced by manufacturers today: access to skilled labor, safer working environments to adhere to OSHA regulations and higher machine spindle utilization." For the large bent pipes described above, RÖHM has developed a chuck that makes the process much safer for the operator while reducing pipe-threading time from 15 minutes to 12 seconds. In addition, RÖHM offers swivel chucks that reduce the number of operations of the machining process by affording the ability to produce complete couplings in one clamping, therefore reducing operators, machines and handling systems needed. "In sum, RÖHM chucks are made to help manufacturers ramp up production, combine operations, control labor costs, reduce scrap and improve product quality," said the spokesperson.
Following is a brief synopsis of these oil and gas workholding solutions.
RÖHM LVE Pneumatic Chuck
RÖHM's pneumatic six-jaw front-end LVE chucks are suitable for threading the ends of pipes, in particular the large and long pipes used in oil and gas extraction. These chucks are mounted to the front with a supporting 3-jaw chuck to the rear sides of the machine spindle to allow for heavy-duty chip-cutting performance at high turning precision. On the front chuck, three pendulum arms center the pipe while the three jaws clamp down and compensate. During the machining process the pendulum arms retract, offering uninhibited clearance for the threading operation. The rear chuck stabilizes the pipe, thus offering a firm and precise clamping solution.
LVE chucks are available in a variety of configurations to handle common oil and gas machining situations, such as the machining of bent pipe. Configuration examples include: ES versions with rapid stroke and clamping stroke, versions featuring retracting clamping arms for pre-centering the workpiece and versions with spring clamping and pneumatic release. Additionally, LVE chucks are suited for machining couplings in two set-ups.
RÖHM HSFZ Swivel Chucks
RÖHM's swivel chucks allow machining of bushings, connectors and adaptors from both sides, maximizing radial and axial accuracy while minimizing set-up time. Designed for fully automatic workpiece positioning, the swivel axis rotates 180° on centerline.
In the hydraulically-operated HSFZ chuck, a combination of three concentric clamping jaws with three compensating clamping jaws ensures low-deformation clamping. In the power-operated KSFZ swivel chuck, the workpiece is clamped at six points via three centering jaws and three compensating jaws. Concentric clamping swivel chucks are available from diameters of 210 mm to 820 mm and according to individual application requirements.
Authored by RÖHM Products of America
For more information contact:
RÖHM Products of America
2500 Northlake Drive
Suwanee, GA 30024
770-963-8440
sales@rohm-products.com
www.rohm-products.com