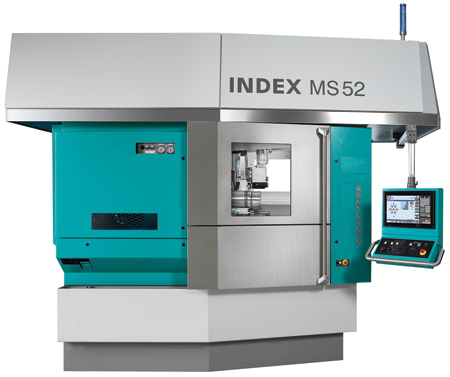
The INDEX MS52C
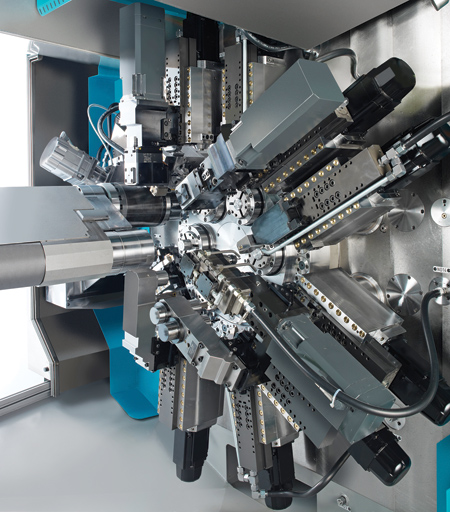
Flexibility with system: Different tools for different machining operations per spindle position can be installed on the cross-slides.
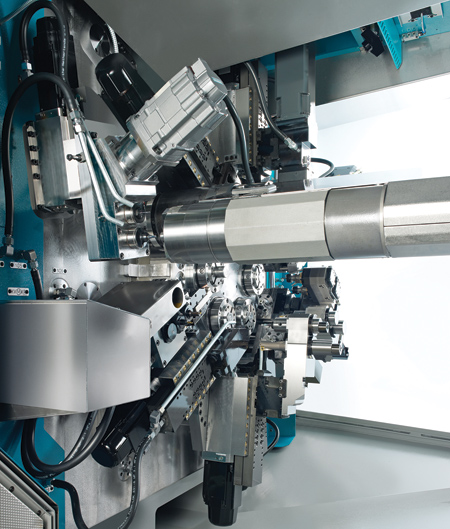
Comprehensive rear end machining on the back-boring slide with the swiveling synchronous spindle
The enhanced INDEX MS52C3 CNC multi-spindle automatic lathe with a spindle clearance of 52 mm features expanded performance functions.
The fluid-cooled spindle drum keeps the thermal growth in the spindle carrier to a minimum. The six spindles, which are stored in a newly developed spindle drum, are cooled according to need. "The advantage compared to the previous air-cooled approach is the higher power density in the spindle drum and the option of energy recovery from the heated cooling fluid," said a company spokesperson. In addition, the spindle bearing temperature can be kept at a low level, which also prolongs its service life and improves thermal stability. Each of the six spindles are assigned two cross-slides, which can be operated both on the X as well as on the Z-axis. Each cross-slide can be additionally equipped with a Y-axis. Tool holders with up to two stationary tools or a turret can be mounted on each cross-slide. The turret holds up to three stationary or live tools. Furthermore, drive units can be installed on the cross-slides for additional machining, such as milling or cross-drilling.
The cross-slides with integrated motor have a low-mass design with hydrostatic bearing support. "They have a low moment of inertia and the resulting high dynamics, which facilitates acceleration in practical application," said the spokesperson. "The advantage of a hydrostatic sliding guide in the feed axis (Z) is its damping characteristics that prevent the transfer of the machining vibrations to the adjacent slide via the headstock." This helps to mitigate vibration and rattling while workpieces are being machined - even when diverse machining processes are being performed concurrently by the six spindles. For example, one spindle can be used for heavy-duty roughing while precision finishing takes place on another spindle without the risk of chatter marks or other impaired surface quality. "In addition, the hydrostatic bearing is wear-free - there is neither friction nor a stick-slip effect," said the spokesperson.
Another of the machine's highlights is its workpiece rear end machining capability, which is achieved using a swiveling synchronous spindle that is locked into the end positions by means of a three-part Hirth coupling. "The high level of stiffness that this achieves also guarantees that even with bar diameters up to 52 mm, rear end machining operations with high cutting volumes and simultaneously high machining precision can be performed," said the spokesperson.
"The swiveling synchronous spindle stands out due to its dynamics; for example, it swivels to the rear end position in less than 0.4 s," said the spokesperson. For rear end machining, three stationary and up to two live tools are available. The advantage of the three-part Hirth coupling is that the operator no longer has to electronically compensate the end position. The mechanical lock is designed to ensure optimal stiffness and increase the positioning accuracy. At the same time, highly complex components that require complex cut-off side machining can also be reproduced with the help of the swiveling synchronous spindle.
"The INDEX engineers were able to achieve a considerable productivity boost due to a smart speed control system in the spindles," said the spokesperson. After each indexing operation, a three-part Hirth coupling positions the spindle drum; however, the speed of the spindles can now be increased or decreased to the speed required in the next machining position even during drum indexing. This means that after each drum indexing operation, correct machining speed is available, which helps reduce cycle times. Due to the fixed electronic connection of the spindles to the transformers in the control cabinet (no wear on the slip ring), no mechanical wear develops in the energy supply system.
The newly designed, low mass synchronous motors have a lower moment of inertia compared to previous synchronous spindles. "In addition, there is the gain in space due to the optimized geometry of the rotor, which results in higher acceleration," said the spokesperson.
The modular INDEX MS52C3 CNC multi-spindle automatic lathe can be operated both as a handling machine and a classic bar lathe. In the handling version, blanks or semi-finished parts are fed into the machine by an integrated robot that picks up the parts from the external handling unit and also discharges the machined parts. There are also options with integrated handling units without the robot. The machine can also be operated as a bar lathe with fully automated bar loaders.
The advantage of the front-opening design for the operator is the accessibility during setup and tooling. Moreover, there is the free chip flow down into the chip discharge chute. To save space, the INDEX engineers placed the machine's control cabinet on the machine. Along with its compact size, the machine also comes with a higher power density.
An advantage of INDEX multi-spindle machines is the fact that two slides can complete one independent external and internal machining operation on the assigned spindle - this means that the production sequence is not determined by the machine concept, but by the user. The MS52C3 can also handle a variety of technologies for turning centers, such as turning, drilling, milling, multi-edge turning, tooth milling, hobbing or slotting.
For shaft machining, the benefits of this machine are that any spindle position with two tool carriers arranged in a V shape can be achieved so that one tool carrier can be equipped with a tailstock center in order to support the workpiece and the other tool carrier can simultaneously perform any type of machining operation.
"The INDEX MS52C3 CNC multi-spindle automatic lathe has many areas of application, ranging from the automobile industry to medical technology. It can also produce small batches efficiently and economically," said the spokesperson. Another benefit for the user is that all standard toolholders and toolholder system interfaces can be used with the appropriate adapters (Capto, HSK, VDI, INDEX systems).
"Catering to current market demands, which dictate that workpieces be discharged damage-free from the work area and at the same time have to be placed on pallets in the right position for later treatment, the Esslingen multi-spindle specialists offer elegant solutions: for example, machine-integrated handling with an external stacking unit that ensures both destruction-free removal of parts from the machine - with connected measuring operations for the workpieces if needed," said the spokesperson. "The current workpiece data can be reported back via the relevant interfaces without any time loss so that the machine control can automatically correct its machining parameters.
"For years, all INDEX machines have met the demand for reduced energy consumption," continued the spokesperson. The INDEX MS52C3 offers the following benefits: weight-optimized components for reducing energy consumption and for increasing the dynamic response; energy recovery by means of regenerative drives; energy shutdown of units that consume large amounts of energy after a user-defined time (standby mode); minimized friction based on optimally paired materials and low-friction bearings (hydrostatic circular guide); and intelligent cooling principles for targeted cooling of the machine and economical use of waste heat. The INDEX cooling concept is designed to ensure that the spindles, hydraulics and control cabinet are cooled constantly and that the heat can be supplied to a different application via a "cold-water interface," e.g., for service water heating or as process heat for other manufacturing steps.
For more information contact:
INDEX Corporation
14700 North Pointe Blvd.
Noblesville, IN 46060
317-770-6300
sales@index-usa.com
www.indextraub.com
Southwest
N. TX
Hillary Machinery, Inc.
1825 Summit, #207
Plano, TX 75074
972-578-1515
www.hillaryinc.com
S. TX
PD Browne South
440 Brenmar
Houston, TX 77060
281-405-9378
www.pdbrownesouth.com
OK
Gage Machine Tool
10668 Widmer Road
Lenexa, KS 66215
913-894-1233
www.gagemachinetool.com
Southeast
AL, GA
Applied Machine Solutions, Inc.
2200 Airport Industrial Dr., Suite 300
Ball Ground, GA 30107
678-880-0893
info@appliedmachine.com
www.appliedmachine.com
NC, SC, VA
Advance Machinery Sales, Inc.
416-C Gallimore Dairy Rd.
Greensboro, NC 27409
336-665-9114
www.am-sales.com
FL
Arthur Machinery
5903 Johns Rd
Tampa, FL 33634
813-887-4455
www.arthurmachinery.com
Northeast
DE, MD, E. PA, NJ, NYC, Long Island
Automation Solutions, Inc.
2 Hagerty Blvd., Ste. 300
West Chester, PA 19382
610-430-3670
inquire@asi-pa.com
www.asi-pa.com
N. NY
Britton Machinery Sales
P.O. Box 709
Pittsford, NY 14534
585-924-9335
www.brittonmachinery.com
W. PA
Marcus Machinery
106 Bellefield Court
Gibsonia, PA 15044
412-862-0803
info@marcusmachinery.com
www.marcusmachinery.com
MA, CT, RI, ME, NH, VT
Northeast CNC, LLC
36 Bartlett Rd., Unit 1
Gorham, ME 04038
207-775-5510
sales@necnc.com
www.necnc.com
Midwest
KS, W. MO
Gage Machine Tool
10668 Widmer Rd.
Lenexa, KS 66215
913-894-1233
www.gagemachinetool.com
E. WI
Iverson & Company
441 North 3rd Ave.
Des Plaines, IL 60016
847-299-2461
sales@iversonandco.com
www.iversonandco.com
MI
Methods & Equipment Associates
31731 Glendale Ave.
Livonia, MI 48150
734-293-0660
sales@methods-equipment.com
www.methods-equipment.com
MN, IA, ND, SD, E. NE, W. WI
Hales Machine Tool, Inc.
2730 Niagara Lane North
Plymouth, MN 55447
763-553-1711
sales@halesmachinetool.com
www.halesmachinetool.com
West
OR, WA
Ellis Machinery & Equipment, Inc.
6225 20th Street E.
Fife, WA 98424
253-926-6868
sales@ellismachinery.com
www.ellismachinery.com