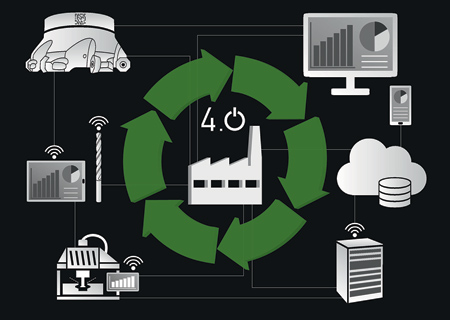
The Tool-ID solution from Walter is designed to save the user time and improve process reliability.
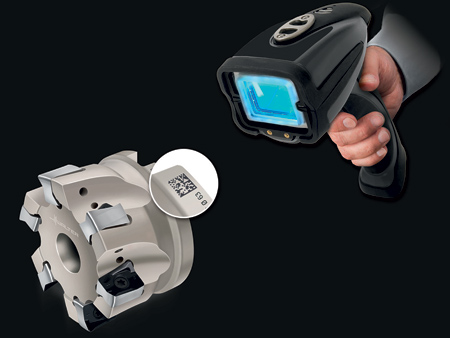
The Tool-ID data is assigned via an identifier, for example, a laser-engraved data matrix code on the tool.
Aimed at keeping machine downtime and processing times to a minimum, this Tool-ID solution allows the user to transfer tool data from the pre-setting device to the machine tool, and to evaluate the parameters that are run on the machine. The data is assigned to the tool via an identifier, for example a laser-engraved data matrix code on the tool.
The data is called up using a scanner and automatically transferred to the machine control unit.
"It is an essential component for communication between the tool and the machine. The tool also provides production information in a form that can be read by the machine. Using this information, tool life or presetting data, as well as the individual production steps can be monitored and controlled. Due to this comprehensive overview, it is possible to detect potential problems early on and remedy them promptly, bringing us a step closer to the smart factory of the future," said the spokesperson.
In the smart factory, production and operating sites are linked in such a way that all processes can be coordinated centrally and controlled automatically. Walter is currently developing a "System of Systems" in addition to Tool-ID that takes the company even closer to the smart factory. This solution allows all the accessible data within the production environment to be viewed and processed according to the user group.
"The aim of this new development is to digitize all relevant information relating to the production process and make it available for analysis and optimization," said Holger Langhans, Director of Walter Multiply.
This universal, fully integrated "System of Systems" digitally links all production units involved in the process via a shared server. This means that the user can, for example, quickly call up and view all changes made in the machining programs. In the future, users will be able to view, combine and evaluate data at the touch of a button from a workstation, or by using apps on a smartphone or tablet. This gives them a complete view of the processes in real time. Downtimes and processing times are reduced, and damage to components and equipment is minimized, all of which has a positive impact on productivity. The solution is aimed primarily at facilities that have ten or more CNC machines.
For more information contact:
Walter USA, LLC
N22 W23855 Ridgeview Pkwy. West
Waukesha, WI 53188
800-945-5554
www.walter-tools.com/us