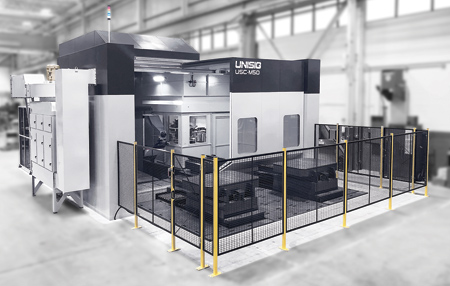
USC-M50 with pallet changer
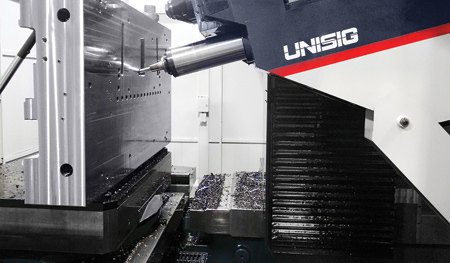
USC-M50 milling operation
UNISIG's USC-M38 and -M50 Milling and Drilling centers provide deep hole drilling and milling on the same machine platform, allowing mold builders to reduce part handling and set-ups. Having fewer set-ups improves repeatability and shortens lead times, addressing a common challenge for mold builders.
These machines have dedicated spindles for BTA + gundrilling and for milling, with 7-axis dynamic performance. These dual-range geared headstock machines provide strong milling performance and a wide speed range for rough and finish cuts. Mold builders can also easily access five sides of their parts with UNISIG's 5-axis positioning and rotary table, allowing them to perform complex machining and deep hole drilling at compound angles.
With its CAT 50 machining spindle and dual-range geared headstock, the USC-M385 and M50 offer 4,500 RPM machining speed and 5,000 RPM BTA drilling/gundrilling. Servo and drive systems are integrated to allow moldmakers to optimize feedrates without risk and maximize deep hole drilling, utilizing the latest gundrilling and BTA drilling technologies.
These UNISIG milling and drilling centers also have improved machine geometric accuracy, allowing accurate compound angle machining, intersecting bores and complex surface milling.
"These features, with the reduction in part set-ups, allow mold builders to take weeks out of production schedules," said a company spokesperson.
USC-M38 and M50 machines from UNISIG feature robust tables built to handle large molds, with heavy weight capacity from a reasonably sized table-as high as 23 tons on the USC-M50. Dual pallet loaders are available to allow automatic workpiece exchange and improve machine utilization. Automatic tool changers with up to 120 positions help to streamline manufacturing processes, adding to productivity.
UNISIG machines are engineered and manufactured in the USA.
For more information contact:
UNISIG
N58W14630 Shawn Circle
Menomonee Falls, WI 53051
262-252-5151
sales@unisig.com
www.unisig.com