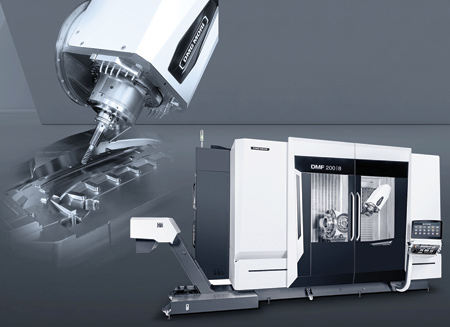
The DMF 200|8 provides 5-axis machining of long workpieces up to 2,300 mm.
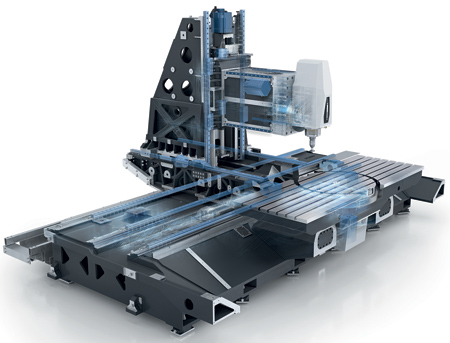
Extensive cooling measures as standard help ensure high thermal long-term accuracy.
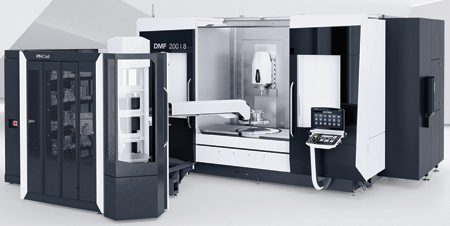
The DMF 200|8 is equipped with an interface for automated production, for example for PH Cell pallet handling.
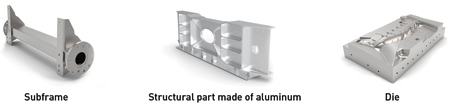
The machine concept of the DMF 200|8 offers enhanced flexibility and productivity in key industries such as die & mold, the aerospace sector and engineering.
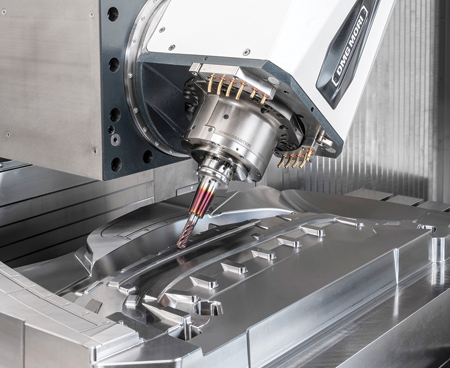
Precision machining of a die
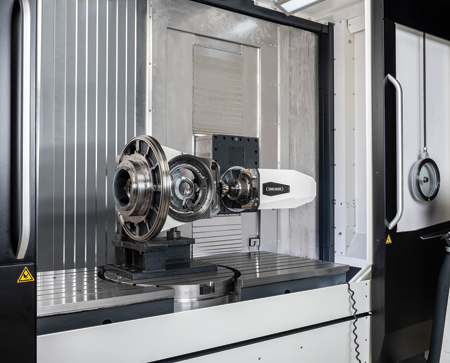
Production of a table console
"With the DMF 200|8, DMG MORI has succeeded in continuing the success story of travelling column machines in the 5-axis range, with over 2,700 machines installed in the market to date," said Markus Rehm, Managing Director DECKEL MAHO Seebach.
Rehm continued, "With a rigid table measuring 2,300 mm x 850 mm and traverse paths of 2,000 mm x 800 mm x 850 mm, the DMF 200|8 offers users in die & mold and aerospace sufficient scope to flexibly machine even long structural components or mold inserts."
The table load is 2,000 kg. During the development of the new machine concept, the working area of the machine was optimized by the tool change feature. This takes place behind the work table, fast and collision-free, so that the entire clamping surface can be used. Compared to the predecessor model, the working area of the DMF 200|8 is over 50% larger, creating new possibilities for machining complex components.
A main feature of the travelling column machines from DMG MORI is their stability. The DMF 200|8 has been designed in such a way that the cantilevered Y-axis provides constant rigidity over the entire travel path. The three linear guides in the X-axis reinforce the stability of the machine and create the necessary basis for precise and productive machining, according to the company. Even with the Y-slide fully extended, maximum spindle power can be accessed without the machine swinging up, noted DMG MORI. Extensive cooling measures as standard help ensure thermal accuracy with the smallest tolerances, while direct-driven ball screws in the Y- and Z-axes provide enhanced surface finishes.
The DMF 200|8 travels at rapid traverse rates of up to 50 m/min as standard. With the optional linear drive in the X-axis, it reaches up to 80 m/min for dynamic and productive machining. The B-axis milling head with maximum clamping torque of 6,000 Nm offers a swivel range of +/-120°. A speedMASTER spindle with 15,000 RPM is integrated as standard. A high-torque version with 200 Nm is available in the modular spindle system as well as a 20,000 RPM spindle.
The DMF 200|8 is equipped with CELOS and SIEMENS and comes with the latest version of CELOS as standard. Rehm referred to the future-oriented and competitive production on the travelling column machine: "The DMF 200|8 offers an interface for automated production, for example with our PH Cell pallet."
For more information contact:
DMG MORI - Americas Headquarters
2400 Huntington Blvd.
Hoffman Estates, IL 60192
847-593-5400
Service Hotline:
855-DMG-MORI (364-6674)
us.dmgmori.com