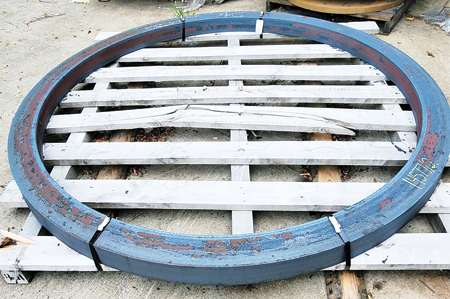
Raw material 4340 alloy steel
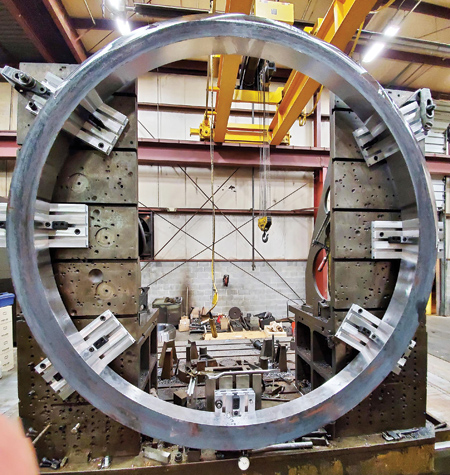
Operation 1 with Mitee-Bite T-Slot Plates and HD T-Slot Clamps. Each Pitbull Clamp develops 12,000 lbs. of pressure.
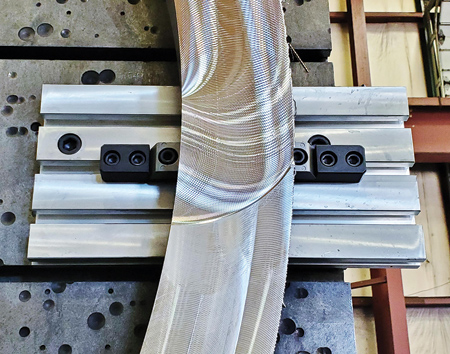
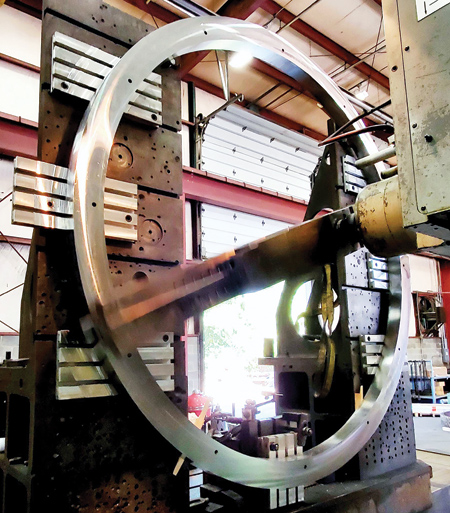
Operation 2 finish pass. Access to I.D., O.D. and face.
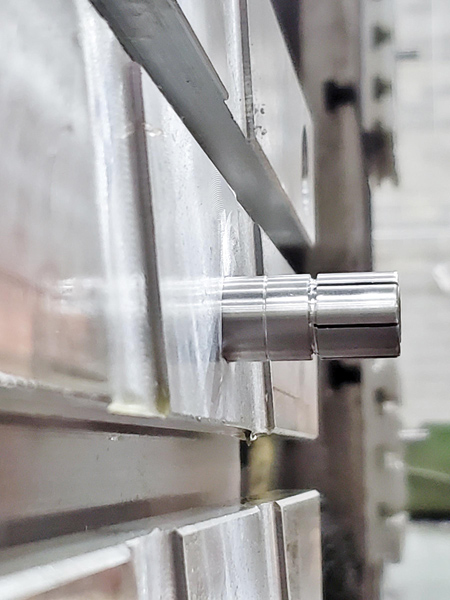
Operation 2 solution using 16 mm Threaded XYZ Xpansion Pins.
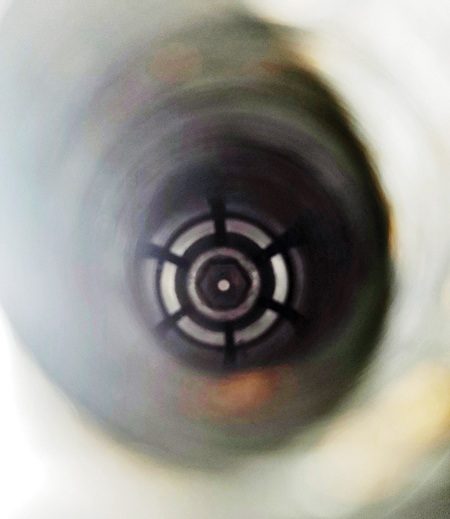
Close up view of Pin expanded in one of seven bores.
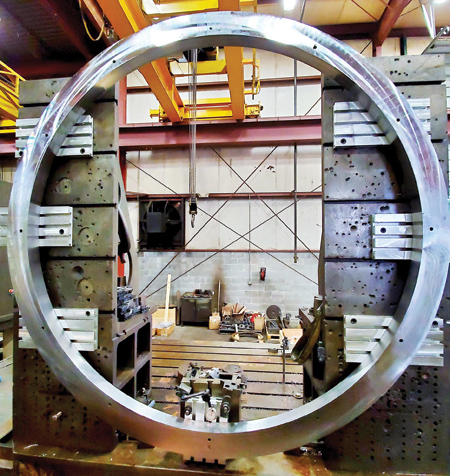
Operation 2 located and secured with XYZ Xpansion Pins.
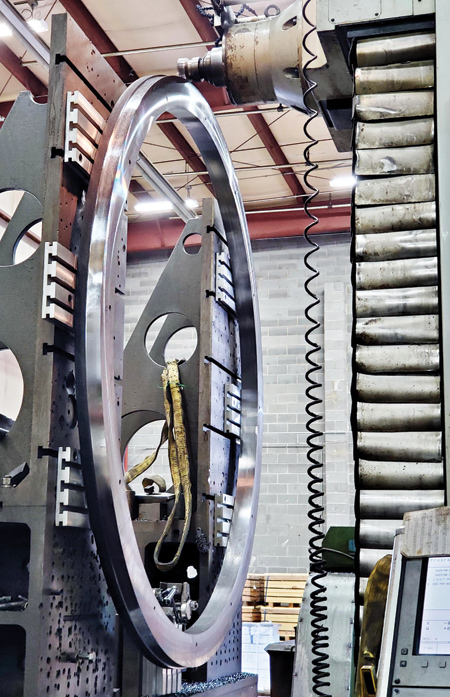
Operation 2
Akron Gear & Engineering had a problem to solve: how to vertically hold a large 1 ton ring (4340 alloy steel). Adding to the dilemma, Akron's VTL was being updated and rebuilt and the customer needed the part as soon as possible.
Akron Gear is no stranger when it comes to large part production. It considers itself to be much more than a gear shop, and has the machining capability to handle from 1/2" diameter shafts and spindles up to 50,000 lb. bases.
Dennis Miller, Akron Gear & Engineering, said, "To the best of my knowledge, this is the largest part the customer has required in the U.S. Right now this is a one-time piece. In order to keep the work in-house while our VTL is being updated, we worked with Rich Jones from Atwood Industries and Mike Witzgall from Mitee-Bite Products to find the ideal workholding solutions."
David Bishop, General Manager at Mitee-Bite Products, said, "There was a lot to be considered with this project. By going vertically as opposed to using the VTL, all the stress from the weight of the part is working against you, and the machining forces are applying even more pressure on the pins and clamps."
After discussions with Michael Witzgall, Senior Applications Engineer at Mitee-Bite, a modular solution mounted on T-slot sub plates was recommended. The solution entailed the use of new Mitee-Bite Heavy Duty T-Slot Clamps with Blunt Edge Pitbull Clamps and large Multi Fixture Stops for Op 1, and then Modular XYZ Xpansion Pins for the I.D./O.D. and facing operations-leaving the part completely free from any clamp interference.
Miller explained how the project took shape: "The top section had no real support, and the only issue encountered was the span between the top supports due to the position of our angle plates. It created a lot of vibration. Initially, I was using a 6 inch face mill to cover the entire face in one pass. The crust was much harder than the material under the surface, so machining this unsupported portion of the ring resulted in chatter marks. I switched over to a 4 inch face mill to get through the surface. Once below the crust, I was able to go back to the 6 inch mill, which I ran at a .060 depth of cut and 90 IPM feedrate. It still had a very slight vibration during machining." To take a final pass for the finish, Miller used a 6 foot boring bar with a single point insert that produced a nice finish and cleaned up all of the vibration.
"With the XYZ Xpansion Pins, which I believe had less vibration, we can do three sides in one set-up-saving a load of set-up time from moving clamps and indicating the bore in countless times. Now we are set up with the XYZ 16 mm Xpansion Pins and I am roughing the O.D. down close to size where it will be finished using an O.D. turning set-up," said Miller.
Miller added, "I cannot say exactly how much time was saved on the set-up, but it was significant since I did not have to keep changing the clamping set-up and indicating it in. It just goes to show that you do not need the biggest clamp to hold the bigger parts."
In less than 10 days after the initial call, Akron Gear was making chips and more efficiently than in the past. "Imagine if this job had to be routed overseas. Correspondence can be difficult, not to mention two-month transit time for ocean freight delivery-that cost alone could exceed manufacturing expenses. We are proud to help keep this job in the U.S.," said Bishop.
Bishop added, "Akron contacted us looking for a solution to hold a large heavy ring vertically, and we provided a low cost modular solution using some of our newer products. What really impressed me was how quickly they put the plan into action. As the old saying goes, if you are not making chips, you are not making money. This is a perfect example of what we strive to provide our customers."
Akron Gear & Engineering provides parts and service to a wide range of industries. It has the equipment and knowledge to handle some of the largest machining jobs and the ability to supply large industrial gears.
Mitee-Bite Products is an innovator of compact, low-profile edge clamps geared towards improving productivity and providing solutions for difficult workholding applications.
For more information contact:
Akron Gear & Engineering
501 Morgan Ave.
Akron, OH 44311
800-258-6608
www.akrongear.com
Mitee-Bite Products LLC
340 Route 16B
P.O. Box 430
Center Ossipee, NH 03814-1430
800-543-3580
miteebite@miteebite.com
www.miteebite.com