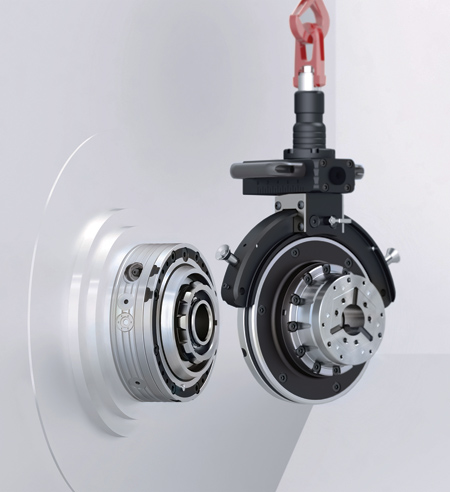
Hainbuch's new centroteX S facilitates manual or robotic loading.
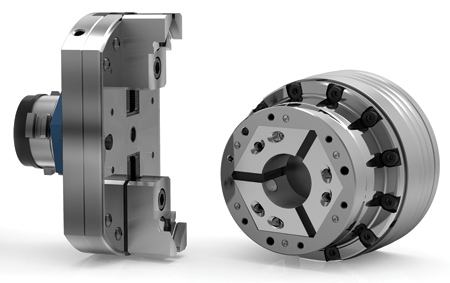
Hainbuch's 2-jaw module with TOPlus is designed for both prismatic and rotational parts.
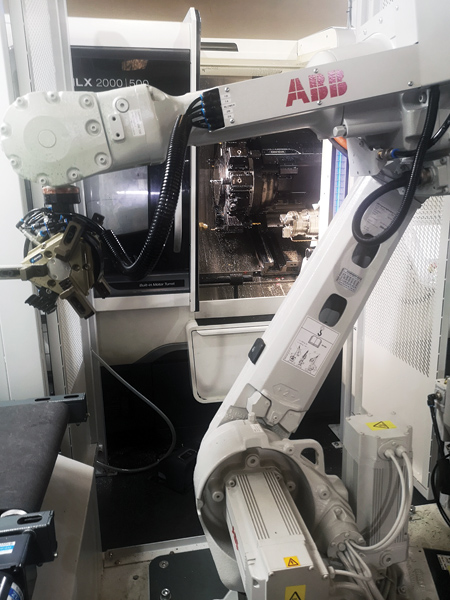
New production cell at Parker-Hannifin Sheffield incorporates a DMG MORI Dual Spindle Lathe, an ABB robot and a Hainbuch quick-change workholding system.
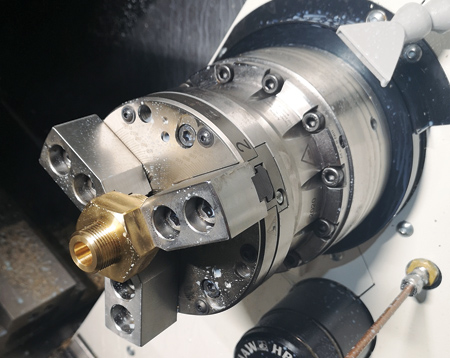
Parker-Hannifin parts include both rotational and hexagonal configurations.
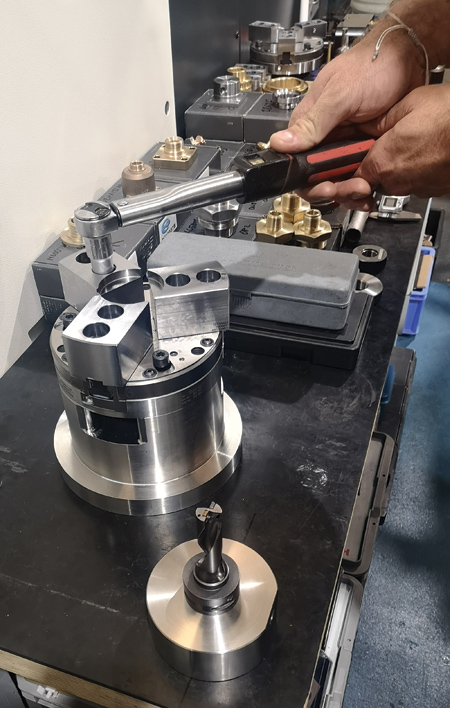
The Hainbuch modular adaptations are easily removed and quickly set up.
"A real game changer" is the way Lloyd Cooper, Production Manager at the Parker-Hannifin Sheffield UK plant, described their newly assembled manufacturing cell. The large-scale investment, which is part of an ongoing effort to revitalize manufacturing in the UK while expanding the customer base, is expected to pay back the cost in under two years.
According to James Utting, Senior Production Engineer, "We made the decision to replace three older lathes with an automated production cell capable of handling our high-mix/low-volume runs. The parts we make are typically secondary (internal) valve components for a wide variety of uses, including mining, industrial, marine, refrigeration and others. Parts are both rotational and hexagonal and are made from brass, 316 and 304 stainless and other metals. The raw material is both bar stock and billet."
The cell is composed of a DMG MORI NLX 2000 | 500 dual spindle lathe, a bar feeder and an ABB SC3000 Flexloader robot. At the heart of the system is a Hainbuch quick-change precision workholding system equipped with 12 clamping heads and four 3-jaw chuck modules with soft jaws.
"We have thousands of part numbers, and our runs generally range from five to 100 or so parts," said Utting. "Formerly, it would take over an hour to set up for a 10-minute run. Now, thanks to the flexibility of the Hainbuch quick-change system, we can accomplish a collet change in as little as 15 seconds. When we have to move from the collet to the 3-jaw module, we simply remove the collet and clip in the module and then screw in three bolts. The set-up is done in two to three minutes. Because it is a precision system, the accuracy is spot on and consistent. The clamping force is as high as 100 kN, so push back is eliminated without marring the part. In fact, it is faster to change the jaw module entirely than to leave it and make any jaw changes on the machine."
Nick Peter, General Manager, Hainbuch Workholding Technology UK, stated, "When the Parker-Hannifin team was in the planning stages, they initially asked us about chucks. As we started working together, we realized how our quick-change clamping system could help them reduce their changeover times appreciably. Due to our extensive size range of both chucks and clamping heads, we were able to supply everything they needed with standard components-thereby saving them both time and money. We look forward to working with them as they move forward and increase their customer base."
The size and scope of the Hainbuch line is noted by Hainbuch America President Tim Wachs: "The Hainbuch product line ranges in size from 26 mm to the 160 mm and up to 400 mm with a centroteX configuration, which can be utilized with either a Hainbuch supplied chuck or the customer's existing chuck. We are continually augmenting our lines with new and advanced products. For instance, our centroteX S system, which can be secured or removed by actuating only one bolt, was designed to enable a robot to quickly change the clamping device. Our new 2-jaw module can be used in both turning and milling operations to secure prismatic parts with speed and precision. Customers such as Parker-Hannifin Sheffield are seeking to optimize their processes. This requires a leadership mentality that is agile in its approach and willing to adapt to new methods."
"Our experience with our new manufacturing cell has extended our capabilities in several directions," Utting said. For instance, we can customize legacy products, as well as easily assimilate new designs. The fact is that it is just as profitable to automate small batches as large batches when you can cut changeover times. The flexibility inherent in the Hainbuch system has helped us to advance significantly in Parker-Hannifin's lean manufacturing efforts."
Sidebar
"It's not the part. It's the technology."
Hainbuch America President Tim Wachs brings a philosophical approach to working with customers and defining the systems that best serve their needs. "We have to take the long view of the customer's processes-and even his business. For instance, in defining the best possible workholding system for a particular mix of rotational parts, how the part is held before it is clamped is crucial. By providing the knowledge and the means to correctly load the part, we can achieve precision and repeatability."
The importance of ancillary components to the operation is a value-added that Hainbuch brings to its customers. "We can get really creative with end stops, and, in some cases, have developed tiered systems for key applications. Part sensing is another area of our expertise, especially in high-mix/low-volume situations," said Wachs.
On occasion, Hainbuch sales engineers have saved customers significant amounts of money with out-of-the-box thinking. Wachs explained: "The correct workholding system, when mounted on an older legacy machine, can improve accuracy and repeatability to the level of a much newer model. We have had instances where customers will begin with one Hainbuch system on a newer machine and then proceed to retrofit their older units. Likewise, where capital expenditure budgets are limited, we have assisted customers in purchasing a new, less costly machine, which-when retrofitted with a Hainbuch system-performs at the level of a much more expensive unit.
"The combination of big picture thinking and an ever-expanding product line is providing our customers worldwide with the flexibility to meet the challenges that are defining manufacturing in an age of new materials, complex parts and ever tighter tolerances."
For more information contact:
HAINBUCH America
W129 N10980 Washington Dr.
Germantown, WI 53022
800-281-5734 / 414-358-9550
sales@hainbuchamerica.com
www.hainbuchamerica.com