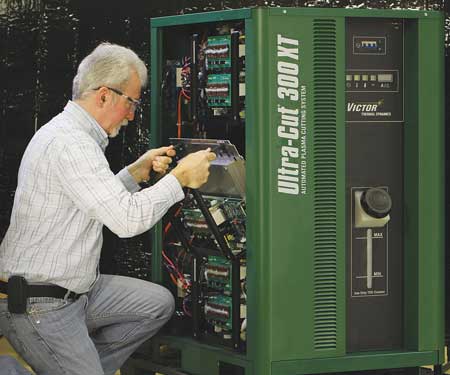
Victor Thermal Dynamics' new Ultra-Cut XT systems feature a modular design that enables end-users to increase cutting capacity. Shown here, a technician installs a 100-amp inverter block to create a 400-amp system.
Victor Technologies has launched the Victor Thermal Dynamics Ultra-Cut XT Series of power sources for automated plasma cutting as part of its integrated system of components.
"The Ultra-Cut XT systems' cut quality enables parts to go directly from the cutting table to welding, painting or assembly without expensive secondary operations. The Ultra-Cut XT delivers ISO Class 3 or better cuts on any material from gauge to 2-inch thick, noticeably reducing bevel and the need for post-cut finishing," said a company spokesperson.
On non-ferrous materials, the Ultra-Cut XT uses the Water Mist Secondary (WMS) process, which incorporates nitrogen as the plasma gas and ordinary tap water for shielding. "On stainless steel, the WMS process cuts up to 300 percent faster and lowers cost per cut by 20 percent or more compared to systems that use Argon-Hydrogen for the plasma gas," said the spokesperson.
With the ability to cut 1-inch thick steel at 80 inches per minute (IPM) and 2-inch thick steel at 30 IPM, the Ultra-Cut XT 400 can lower the cost per cut. The Ultra-Cut XT also uses HeavyCut consumables for cutting at 300 and 400 amps. These consumables use multiple hafnium inserts as opposed to a single insert and feature a two-piece tip that runs cooler.
Compared to previous models, Ultra-Cut XT systems draw 20 percent less primary current and have an average electrical efficiency of 92%. They meet EU Level Five efficiency standards.
The Ultra-Cut XT series is available in 100 to 400-amp configurations for cutting plate up to 2" (50 mm) thick. For added flexibility as needs grow, users can StepUP power and expand a 100-amp system into a 200-, 300- or 400-amp system by adding inverter blocks through an upgrade kit. All models feature a common cabinet and components. An LED error display indicates machine status to accelerate troubleshooting, and should an inverter block malfunction, cutting can continue with the remaining blocks.
The Auto-Cut XT conventional automated plasma systems do not have modular capabilities but do have the capability of cutting with the WMS process, as well as air-air, O2-air and other dual-flow processes. The Auto-Cut 200 XT and Auto-Cut 300 XT have 200- and 300-amp outputs, respectively, both rated at 100% duty cycle.
For more information contact:
Victor Technologies International, Inc.
16052 Swingley Ridge Rd., Ste. 300
St. Louis, MO 63017
636-728-3000
www.victortechnologies.com