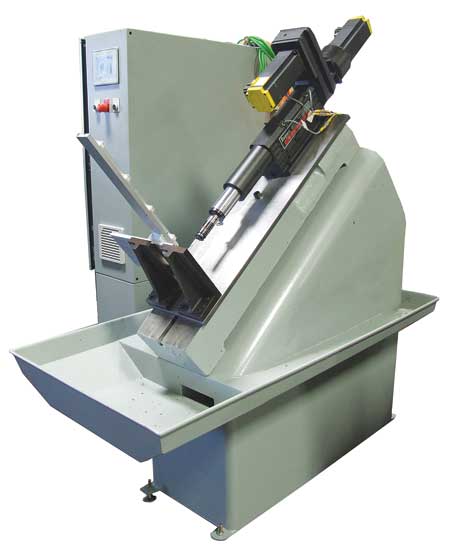
The Zagar high-speed, slant bed tapping / drilling machine provides consistent productivity for high volume, mass production hole making.
Zagar Inc. presents its high speed CNC tapping and drilling machines for mass production, for high volume threads and drilled holes. The newly engineered machine features a Zagar MQ150 CNC ballscrew-actuated, quill feed unit with an in-line spindle motor mount to minimize inertia at reversal when tapping (< .5 second tap cycle capability).
Each machine is supplied with a Zagar turn-key, two-axis, motion control system. The precision ground ballscrew and zero backlash ballscrew nut, enable true rigid pitch, CNC tap cycles. Controls are fully programmed for tapping any inch or metric pitch, as well as left or right hand threads.
Turn-key controls include an HMI interface touch screen, allowing standard machine cycles and positioning programs to be set up through the HMI or downloaded off-site over an Ethernet connection. Machines are optionally equipped with re-circulating, filtered flood coolant systems, metered coolant disbursement or high-pressure coolant fed through the spindle and tool.
Turn-key, automatic material handling systems are available for un-attended part production. Inter-changeable automatic part load / unload fixtures, vibratory feeder bowls, storage bins, and conveyors are designed, interfaced, and tested for automatic, mass production of tapped or drilled holes in high volume parts.
Machines are available with multiple adjacent or opposing units and can also be supplied with multiple spindle heads for single pass machining of hole patterns. All are engineered by Zagar Inc. in 3D using Solidworks. The software for viewing files is a free download, enabling concurrent design and interchange of drawings with end users. Assembly drawings include exploded views and bills of material that are accessible online to maintenance personnel.
For more information contact:
John Zagar
Zagar Inc.
24000 Lakeland Boulevard
Cleveland, OH 44132
216-731-0500
www.zagar.com