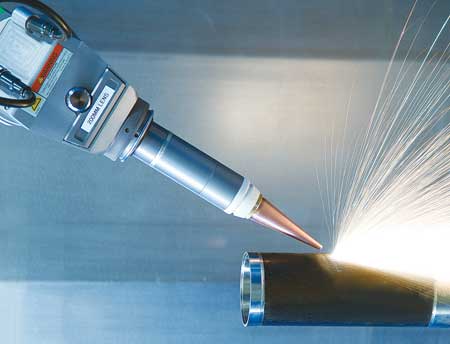
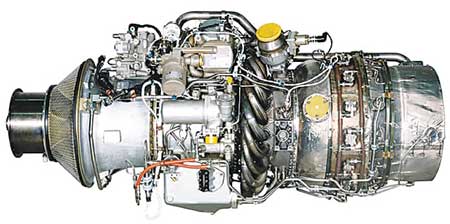
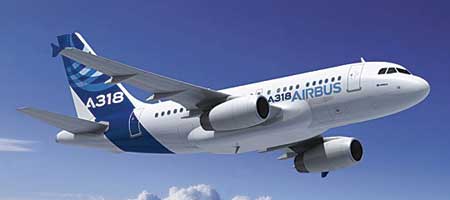
Avio's Laserdyne 430BD laser system is equipped with a fiber laser. A rotary table will be processing components for aerospace engines like the PW 100 engines used in many commercial aircraft such as the Airbus A318. The system is capable of cutting, drilling and welding and has distinct advantages over older systems as described in this article.
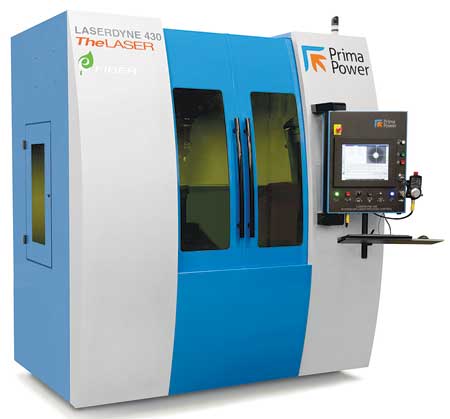
The Laserdyne 430BD laser system is designed for processing 3D aerospace components with a fiber laser.

The motion required for a multi-axis laser is very complex. Laserdyne's AFC feature makes trepanning, percussion drilling and drilling on the fly fast, precise. The photo shows this complex motion simulation made possible by dual processors.
"The latest laser development from Prima Power Laserdyne LLC, the multi-axis Laserdyne 430BD, opens new aerospace design and manufacturing possibilities for laser cutting, drilling and welding at Avio S.p.A," said a Prima Power Laserdyne LLC spokesperson.
Avio S.p.A. is developing advanced manufacturing technology as it expands its laser manufacturing capabilities. This expansion continues Avio's advances in the design, development and manufacturing of aerospace propulsion components for both civil and military aircraft. The newly acquired Laserdyne 430BD with the latest BeamDirector laser beam positioning capability and rotary table gives Avio a six-axis system and the means to create new manufacturing processes while improving existing ones.
For more than a century, Avio has tackled the technological and business challenges of producing high-performance aerospace propulsion components. With over 5,000 employees and operations based in Italy, Avio now supplies customers across four continents. The engine applications include turbine components for business jets to medium and long-range commercial aircraft. Among Avio's current programs are the Pratt & Whitney PW100 family of engines. Users of this series of engines include Airbus, Boeing, Bombardier, Canadair, Embraer and Superjet. Among Avio's many new aerospace engine initiatives is a 14,000 lb. turbofan for the EJ200 engine, a collaborative engine between Rolls-Royce, MTU, Avio and ITP.
In particular, the Pomigliano D'Arco (NA) plant is the center for the manufacturing of combustors, exhaust and re-heat modules. The most important programs that involve the D'Arco Combustor Center of Excellence are:
- EJ200 - Afterburner module
- PW800 - Exhaust Module
- Sam146 - Combustor Module
- T700 - Turbine and Exhaust Module
- PW100 and PT6 - Combustors.
In the manufacturing processes of these parts the intensive use of the laser micro drilling technology is essential to meet the requirements of the project.
"To meet aerospace customers' changing needs, Avio has continuously innovated with its manufacturing processes and facilities. This is especially true in the area of laser material processing. Avio was an early adopter of laser drilling of effusion cooling holes in combustion liners and other high temperature engine components," said an Avio spokesperson.
Avio's history with laser processing dates back to the 1990's when it began using Laserdyne systems at its manufacturing location in Pomigliano d'Arcon (Naples) Italy. The company now will use seven Laserdyne systems with the addition of the Laserdyne 430BD. This will be Avio's first fiber laser equipped system. The new system replaces a Laserdyne 550 with Nd:YAG laser used primarily for sheet metal trimming. The Laserdyne 430BD will continue to be used for these cutting operations, but with its flexible laser machining platform in a compact layout and the integration of the fiber laser, it is equally useful in drilling and welding operations with little changeover effort and time required.
The Laserdyne 430BD integrates a IPG 9kW QCW fiber laser with a wavelength of 1070nm, similar to that of a Nd:YAG laser. "Laserdyne's testing at its Champlin, MN U.S.A. applications lab and at installations around the world has shown that fiber laser systems provide the potential for improved cutting and drilling applications. In addition, fiber laser technology is more energy efficient requiring lower input power for a given level of average output power and also requires less cooling," said the Prima spokesperson.
"In addition to introducing the fiber laser at Avio, the Laserdyne 430BD combines tested and proven Laserdyne motion and process control capabilities in a new, smaller and more space-efficient platform. With higher velocity and acceleration, the third generation BeamDirector (BD3Y) used on this system has the exclusive Laserdyne contouring head design with C-axis (rotary) motion of 900 degrees, and D-axis (tilt) motion of 300 degrees. Among its many features are optical encoders for improved accuracy and repeatability, higher assist gas air-flow, adjustable mirrors for easy and accurate beam alignment and cassette mounted lens and cover slides for quick, accurate changeover," said Mark Barry, Vice President of Sales for Prima Power Laserdyne.
According the Mr. Barry, "Avio's new 430BD system will use the LASERDYNE S94P control which includes a full complement of standard hardware and software features. These include Automatic Focus Control for capacitive part sensing; patented Optical Focus Control (OFC) for sensing of thermal barrier coated surfaces; ShapeSoft software for programming shaped holes; Breakthrough Detection for drilling clean, consistent holes with the minimum number of pulses; mapping and numerous additional software and hardware features. This control will also allow the customer to use programs created for different Laserdyne systems with little or no modification."
The Laserdyne 430BD operates at speeds up to 800 inch/min. in all axes (0-20 m/min) with bidirectional accuracy of 0.0005 inch (12.7 micrometer). This accuracy is throughout the system's 585 x 408 x 508 mm work envelope. Accuracy of the new 430 system is certified to ISO 230-1:1996 and 230-2:2006 in accordance with Prima Power Laserdyne's standard accuracy and repeatability test procedures.
The Laserdyne Automatic Focus Control (AFC) feature has been used by Avio in its earlier Laserdyne systems. Avio has provided feedback to Laserdyne engineers who have refined the hardware and software through the years. AFC guides the motion system, maintaining critical focus position and following the contour of the part regardless of slight surface irregularities. With AFC, all machine axes react to sensing of the part surface, creating unlimited motion along the axis of the beam (called the R-axis). "AFC allows top machine speeds so productivity is maximized without downtime or scrapped parts," said the Prima spokesperson.
"Our approach of combining the motion and process control capability associated with Laserdyne products with the beam quality and control of fiber lasers will no doubt yield further advances in cutting, drilling and welding processes," Mr. Barry said."
For Laserdyne's report on fiber laser drilling, go to http://www.primapowerinterface.com/fldp/index.html.
For more information contact:
Avio S.p.A.
Via 1 Maggio 99
10040 Rivalta di Torino
(Turin) - Italy
39-011-004171
www.aviogroup.com
Prima Power Laserdyne
8600 109th Ave. North, #400
Champlin, MN 55316
763-433-3700
LDS.sales@primapower.com
www.primapower.com