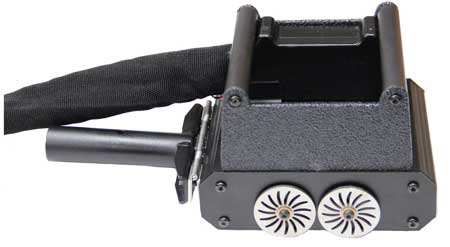
Miller Electric Mfg. Co. has introduced the ProHeat 35 Rolling Inductor technology for preheating and post weld stress relief in rolled pipe welding applications.
Miller Electric Mfg. Co. has introduced the ProHeat 35 Rolling Inductor, an induction technology for preheating in rolled pipe welding applications. "When connected to the Miller ProHeat 35 induction heating power source, this system provides pipe fabrication shops with increased productivity, improved safety and consistency in heating," said a company spokesperson.
"Many ASME-certified shops weld pipe spools for the refinery, petrochemical, power and HVAC industries and the majority of those jobs are roll welded for improved productivity," said Kristi Endries, Heating Solutions Specialist for Miller Electric Mfg. Co. "However, rotating pipe while welding limits a welding operator's options for preheating and maintaining interpass temperatures to non-electrical methods, such as flame. The new ProHeat 35 Rolling Inductor released by Miller solves these issues by combining the benefits of rotating pipe and electrical preheating into one."
Pipe assemblies that are chrome alloy, heavy wall or stored in cold environments require preheating because of code and quality control requirements. Jobs that benefit from rolling induction technology include applications using carbon steel that is colder than 50 degrees F, carbon steel over 1 inch thick; or any chrome alloy steels.
The ProHeat 35 Rolling Inductor is compact and portable to configure around various pipe sizes throughout the shop. This non-contact method of heating while rolling the pipe assembly also eliminates wrapping cables and allows for continuous fabrication.
The ProHeat 35 Rolling Inductor and its hinged arm are mounted on a standard pipe stand, allowing the welder operator to align the induction head on the top or side of the pipe. The power source then recognizes the attachment, so users must only set maximum output and time. The Rolling Inductor can easily be removed from or put back on to the pipe, mirroring the simplicity of turning a torch on or off.
"Because the ProHeat 35 Rolling Inductor sits directly on the rotating pipe and provides steady, continuous output, hot and cold spots are eliminated, minimizing risks of weld failure due to cracking," said a company spokesperson. "The Rolling Inductor greatly improves efficiency versus flame heating, because the heat is generated within the part. Direct heat transfer also results in a cooler shop environment and reduced fume levels. Elimination of open flames significantly reduces burn potential and welder fatigue, as well as the need to store explosive gases used for heating."
In addition to induction technology used while rolling pipe, the ProHeat 35 power source is capable of other applications including hydrogen bake out, shrink fit and post-weld heat treatment.
For more information contact:
Miller Electric Mfg. Co.
P.O. Box 100
Lithonia, GA 30058
800-4-A-Miller (800-426-4553)
info@millerwelds.com
www.MillerWelds.com