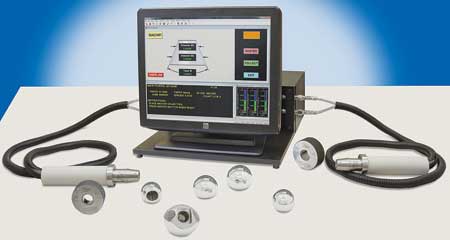
Mahr Federal's orthopedic taper measuring system allows the manufacturer to have a universal gauging station that can be used in completely different manufacturing cells.
A manufacturer of orthopedic implants needed to improve measurement and documentation proficiency of parts with literally hundreds of configurations. "Air gauging from Mahr Federal was chosen because it could quickly and accurately measure precision tapers, along with being simpler and cheaper to engineer than any mechanical gages," said a company spokesperson. "Air gauging does not require linkages to transfer mechanical motion, so the contacts (jets) can be spaced very closely and at virtually any angle. This allows air to handle tasks that would be difficult or extremely expensive with mechanical gauging.
"Gauging the taper of a bore is a basic application that benefits from close jet spacing. All it takes is a single tool with jets at opposite sides of the gauge's diaphragm. The gauge registers only the difference in pressure between the two sets of jets, directly indicating the amount of taper.
"But because air gauging is custom made for the application, there can be just as many air tools as there are part variations - a logistics nightmare when there are thousands of component combinations."
To reduce the number of tools, Mahr Federal designed a master air tool with multiple jetting and a series of spacers that allowed one tool to be used on all the various tapers, regardless of length. The gauge could be zeroed on a single master spacer and the operator could measure parts by selecting the appropriate spacer.
The manufacturer also wanted to use the gauge in different work cells in order to measure multiple parts from different machines. Mahr Federal created a custom touch screen-based gauging computer that was able to: 1) store all part files and select the right tool by part number; 2) pull the proper calibration offsets; 3) document measurements and print customer reports; and 4) store data for future documentation. Finally, separate air gauging inputs allowed monitoring of different parts being machined on two different machines by different operators.
"This innovative orthopedic taper measuring system allows the manufacturer to have a universal gauging station that can be used in completely different manufacturing cells," said the spokesperson. "It provides superior measuring capabilities, automated part and gage selection, and any process documentation that may be required."
For more information contact:
Mahr Federal Inc.
1144 Eddy Street
Providence, RI 02905
800-343-2050 / 401-784-3100
information@mahr.com
www.mahr.com