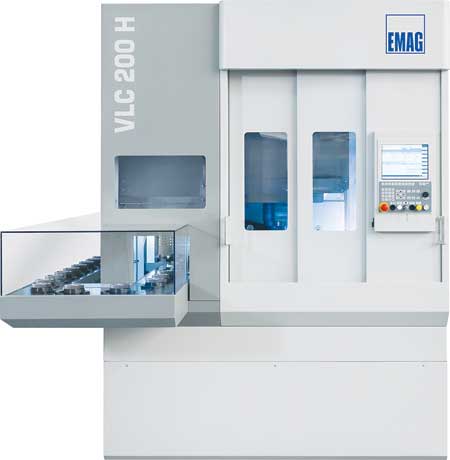
VLC 200 H vertical pick-up hobbing machine for workpieces of max. 200 mm diameter.
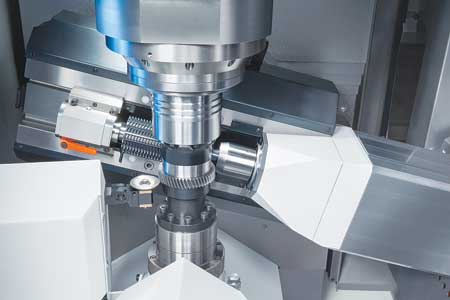
The VLC 200 H is designed for the machining of gear-type workpieces of maximum 200 mm diameter and module 4.
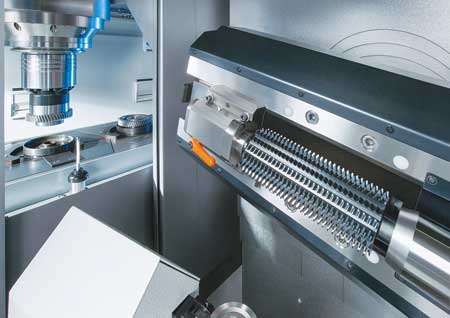
The machine is loaded and unloaded using the pick-up work spindle. In the milling of gear shaped workpieces this intelligent system is designed to be of benefit to production levels.
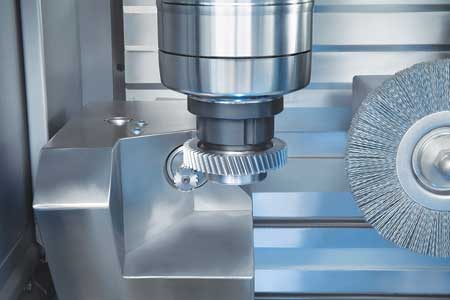
The VLC 100 D is an automated deburring machine that loads and unloads itself using the pick-up spindle. According to the company, it is the ideal companion to the VLC 200 H hobbing machine and can be used for the deburring/chamfering of external gearings, helical gearings and similar geometries.
Drivers are already used to the sixth gear - and the development continues. There are plans afoot for an automatic gearbox for a nine-gear transmission system. The reason is obvious, since it allows the car to be driven at optimal speeds for longer intervals and that saves fuel. Together with the continuing pressure to optimize, high-volume gear production must become faster and cheaper. The EMAG Group has demonstrated its solution: the VLC 200 H vertical hobbing machine that adds a new dimension to productivity levels.
Transmission technology accounts for a large percentage of research costs in the automotive industry, according to experts.
"KOEPFER, a subsidiary of EMAG, is no stranger to this dynamic," said a company spokesperson. "Not just a supplier of machines for the high-quality gear production, KOEPFER is also a competent partner for anything to do with the gear. For decades now they have invested heavily in industry developments. A product of close collaboration within the EMAG Group, the VLC 200 H is the latest result of these efforts." The VLC 200 H vertical hobber is the first KOEPFER machine based on the new modular standards of EMAG, bearing the name of the new standard machine platform that represents a new generation of machine tools for use in a range of greatly varying applications.
"This modular approach is of great advantage when it comes to establishing a highly efficient production system for the transmission industry, as it allows for the individual processes used in the soft machining of a gear, from turning of the raw part to hobbing and deburring, to be combined with perfection and without any great outlay for automation. The machines are easy to interlink, as they are perfectly coordinated and work at the same transfer height," said Jörg Lohmann of KOEPFER.
"A closer look at the VLC 200 H hobbing machine reveals a technology that offers the user great economic advantages, even in its stand-alone version," said the spokesperson. "The machine features high-performance drives offering top main spindle and hobbing speeds. Gears of a maximum diameter of 200 mm and module 4 can be dry-milled at greatly shortened cycle times. Removal of the hot chips generated by the process is of no concern on vertical machines, as they fall unhindered into the chip conveyor below. The typical EMAG pick-up design principle also minimizes idle times. The main spindle removes the raw part from the conveyor belt, transfers it to the tailstock - where it is firmly supported during machining by a tailstock flange - and removes it from the machining area after completion of the hobbing cycle. This integrated automation concept with short travels not only makes for efficient speeds, but also guarantees a high degree of machine availability."
According to Lohmann, the VLC 200 H also guarantees exceptional and consistent component quality. "This it owes, in part, to the vibration-resistant polymer concrete MINERALIT machine base," he said. "An optional measuring probe can be integrated into the machining area and used for either positioning tasks or the measuring of finish machined components. It even allows us to carry out adjustments in the machining process. In fact, the whole machine provides added value with its integrated production process quality control."
Designed on the basis of a modular platform, production planners have a choice where this automated high-efficiency package is to be integrated into a manufacturing system. They can choose directional component flow, recirculating automation or the chaku-chaku principle. A processing concept planned by EMAG experts helps ensure the lowest cycle times: after turning of the raw parts on an EMAG VL 2 the gear cutting process is carried out on the VLC 200 H, with the final deburring and single-sided chamfering process following on the VLC 100 D. All these machines are designed on the modular standard basis from EMAG. "The gearing is generated in a single cut and followed only by chamfering, in comparison to alternative production solutions that rely on a second cut after chamfering," said the spokesperson. "Cycle times for the machining of gears will drop dramatically with modular EMAG solutions and KOEPFER technology."
For more information contact:
Peter Loetzner
EMAG LLC
38800 Grand River Avenue
Farmington Hills, MI 48335
248-477-7440
info@usa.emag.com
www.emag.com
Southwest
AR
Ken Pope
EMAG LLC
256-642-6842
kpope@emag.com
www.emag.com
TX, OK, LA
Ric Lorilla
EMAG LLC
248-595-1530
rlorilla@emag.com
Southeast
VA, NC, SC, GA, FL
David Fitzgerald
EMAG LLC
248-595-1117
TN, AL, MS
Ken Pope
EMAG LLC
256-642-6842
kpope@emag.com
www.emag.com
Northeast
PA, NY
Kirk Stewart
EMAG LLC
248-996-4703
kstewart@emag.com
ME, NH, VT, MA, RI, CT, NJ, DE, MD
Jonathan Chomicz
EMAG LLC
248-497-8526
jchomicz@emag.com
WV
Ken Pope
EMAG LLC
256-642-6842
kpope@emag.com
www.emag.com
Midwest
IN, OH
Kirk Stewart
EMAG LLC
248-996-4703
kstewart@emag.com
MI
Geoff Fuller
EMAG LLC
248-632-2021
gfuller@emag.com
ND, MN, WI, SD, NE, KS, IA, MO, IL
Bill Konetski
EMAG LLC
612-804-0857
bkonetski@emag.com
KY
Ken Pope
EMAG LLC
256-642-6842
kpope@emag.com
www.emag.com
West
Arnie Sugiyama
Caltec International
19801 Hamilton Ave
Torrance, CA 90502
310-527-4110
arnie@caltecusa.com