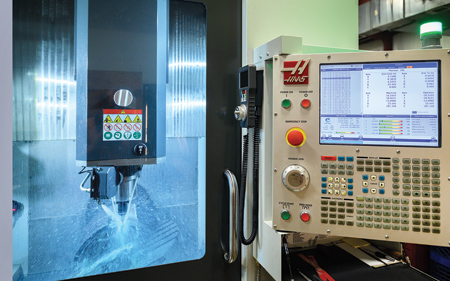
Profiling a calibration block using Mastercam Swarf toolpath on a Haas UMC 1000.
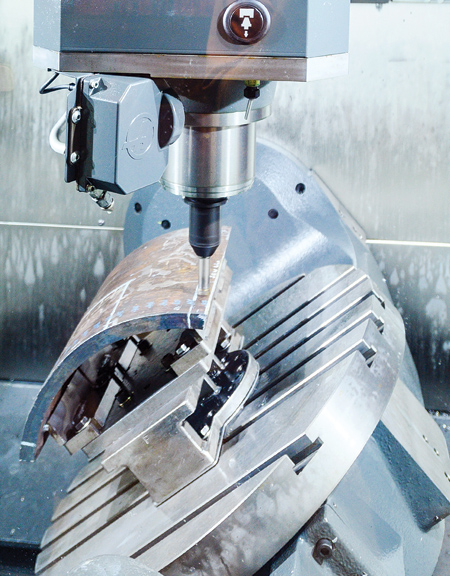
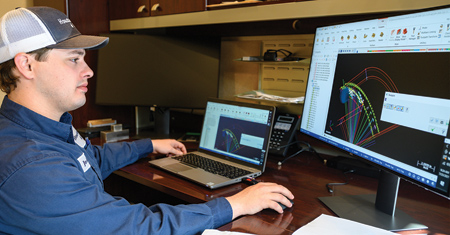
Josh Bennatt, Houston Mold & Tool General Manager, uses Mastercam to ensure generation of proper toolpaths for optimum machine efficiency.
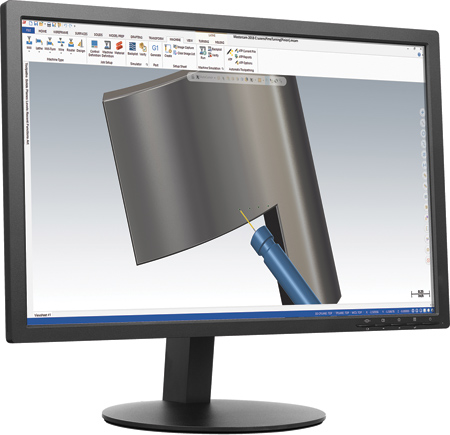
Mastercam machine simulation verifies toolpaths and any clearance problems.
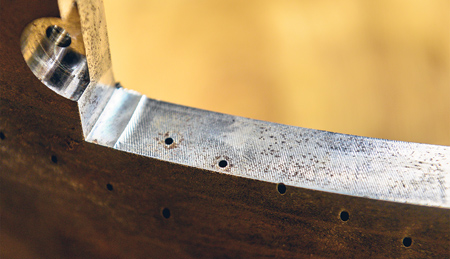
Houston Mold & Tool uses Mastercam C-Hook technology to set heights, polarize depths and choose tools for drilling holes in pipeline calibration blocks.
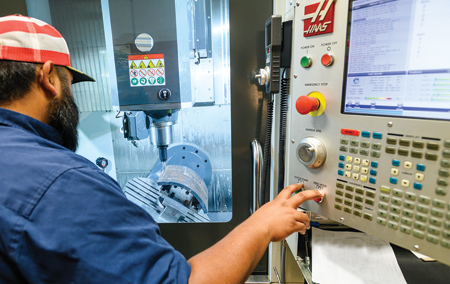
Joseph Meza, Houston Mold & Tool Machinist, machines a calibration block on a Haas machine programmed with Mastercam CAD/CAM software.
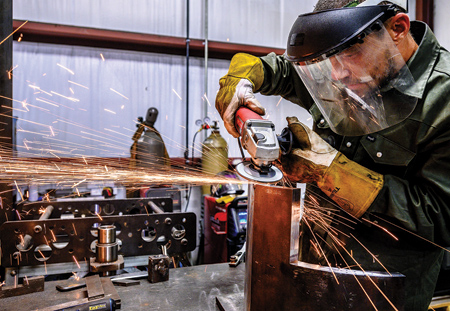
Sparks fly as Paul Manners, Houston Mold & Tool Machinist, fabricates two halves of a calibration block and grinds off the excess weld.
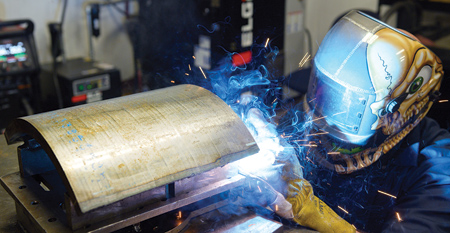
Chris Jesse, Houston Mold & Tool Machinist, welds a section of pipe onto a jig that will later be run through a CNC machine.
Southeast Texas machine shop Houston Mold & Tool, Inc. receives most of its incoming business from the oil and gas industry. Though based in a town named Humble, the six-man shop earned bragging rights for its efficient production of rugged, carbon-steel calibration blocks for oil pipelines.
"We use 5-axis CNC machining centers to produce calibration blocks for offshore and land pipelines, whether they are for a rig out in the Gulf of Mexico or a large land job," said Jeff Stott, owner of Houston Mold & Tool.
The blocks are used for nondestructive testing (NDT) and evaluation of pipeline flaws and cracks. After pipelines are welded and placed underground or offshore, a scanner on the pipe exterior sends ultrasonic sound beams and examines the weld, testing it for flaws. Houston Mold & Tool's calibration blocks are used for the set-up of scanners, simulating the bevel shape of the pipe before it is welded. The application can get tricky since not all pipe is in pristine condition.
"The pipe is always twisted or warped," said Stott. "If you have a 48-in. diameter pipe, the spot you might be machining could be 47 in. in diameter because it is twisted. So, I made my own software that probes the pipe, figures out where it is and takes the theoretical position and moves it to the pipe automatically using the software. Once I run it and save it in our program, it produces a data sheet that we bring into Mastercam."
In the past, Houston Mold & Tool machined calibration blocks by hand using jigs. However, the process proved tedious and inaccurate, leading Stott to develop his own CNC program for the calibration block application. After investing in a 5-axis machining center, Stott spent several years of trial and error perfecting his programming in Microsoft Visual Basic Script. Eventually, he integrated his program into Mastercam, but as versions of the CAD/CAM software progressed, the VBScript application was no longer usable.
In 2005, Stott sought help from Mick George, Software Engineer at CNC Software Inc., to help automate the lengthy programming process for calibration blocks. Together, the colleagues developed a C-Hook, a utility program designed to extend Mastercam.
C-Hooks function as apps for the CAD/CAM software. While many are available from third-party developers, Mastercam includes an extensive library of C-Hooks, including the Gear C-Hook, which can create a single tooth or all teeth of an involute spur or internal gear. It computes the roll measurement for checking the gear. Other examples are the Hole Table Parameter C-Hook, which creates a table that categorizes, counts and labels holes or circles, while Check Holder tests a toolholder against part geometry for clearance.
"The C-Hook developed specifically for Houston Mold & Tool's calibration block application yields huge time savings for the manufacturer," said a spokesperson. "Consider that a typical block might have 26 holes per side and four operations for each hole. For each operation, the programmer must set the top of stock, depth and choose a tool. The C-Hook simplifies the process by importing all geometry and operations, including overrides, speeds, feeds and depths. Depending on the diameter of the tool angle, the top of stock will change considerably; the C-Hook automatically overrides the top of the stock."
"If programmers had to go in there manually, it would be an overwhelming amount of work," said Stott. "Not only that, they would also have to pick all the vector lines to generate the 5-axis toolpath, then regenerate it. If they made a mistake, forgot one step or changed one depth, the part would be scrapped."
When Houston Mold & Tool receives raw pipe from the field that is slated for placement offshore or on land, the C-Hook utility imports the job file, geometry and operations. Once a data sheet is imported, the programmer simply clicks on it. The C-Hook sets all heights, polarizes depths and chooses tools. The programmer is then able to put all numbers on the print that is supplied to clients on an Excel spreadsheet. The C-Hook takes those numbers and creates a 3D model. Corresponding toolpaths are uploaded, providing everything an operator will need to program the part. The software utility regenerates all hole operations, deletes duplicate lines and regenerates all operations.
"All our operators have to do is confirm that the data came in correctly," said Josh Bennatt, Houston Mold & Tool General Manager. "Because there are so many holes and features on a calibration block, to program it and set all the toolpaths would take at least 8 to 10 hours per block. With the C-Hook, Mastercam completes the programming in seconds."
Automating multiaxis programming is a major benefit for Houston Mold for several reasons, one of which is because the shop does not employ many experienced 5-axis programmers.
"They are kind of hard to find," said Bennatt. "The C-Hook allows us to take operators with minimal programming skills and give them the ability to program their own parts."
Depending on customer specifications, each calibration block differs regarding pipe diameter, wall thickness, number of holes and hole size; therefore, C-hooks vary. Some customers design calibration blocks in three pieces, while others use one or two blocks. Pipe thickness varies as well.
When Houston Mold purchased Mastercam 2021, programmers discovered a change in the way 5-axis holes were generated, rendering Houston Mold's VB files unusable. Stott contacted Bo Rohde, Applications Expert at Mastercam Reseller MLC CAD Systems, Houston, TX, to help solve the dilemma.
"Bo and his team at MLC CAD Systems worked with us and created a new C-Hook that can import vector lines and operations," said Stott. "For people who are doing repetitive work with different parameters, the C-Hook technology really is something. It is the reason why we do this process so accurately and consistently. Our blocks are all machined and probed on a Hass UMC 1000, UMC 750 and Haas trunnion 5-axis mill."
Stott estimates that, due to the CAD/CAM software and C-Hook technology, Houston Mold & Tool is saving at least six hours of programming time per calibration block. According to Bennatt, who has been with the company for three years, since using Mastercam for calibration block production, he has never had a scrapped piece. Just one scrapped pipe would cost between $1,000 and $6,000. The company can now produce an average of three to 10 blocks per week.
"To do this by hand, you could have up to 20 tools and 20 to 60 holes with four different operations per hole," said Stott. "That is 80 to 240 different operations with approximately 20 different tools, 80 to 240 different depths and 80 to 240 different top of stocks. You could easily make a mistake or forget to fill one in on any one of them."
Now that Houston Mold is using the latest version of Mastercam software, the shop is accepting complex jobs that require 4- and 5-axis machining. The user-friendly software offers new high-speed toolpaths, including Chamfer Drill. Using tools with a tip angle, the toolpath chamfers holes after calculating the correct depth based on the desired width or depth. A programmer can select holes of different diameters or sizes-or that lie in different planes-and machine them in a single operation with a single tool.
"I really like this new version of the CAD/CAM software," said Bennatt. "It is simplified and has even more options. As far as toolpaths go, we can do much more when it comes to high-speed machining and 4- and 5-axis applications."
For the calibration block application, most of the toolpaths employed by the new version of the CAD/CAM software remain the same. The main difference relates to 5-axis applications.
"For fifth-axis holes with the old CAD/CAM version, we would either have to create a plane or do lines by geometry," said Bennatt. "Now, with the latest version of the software, all we have to do is click on the hole and the actual solid model of the hole, and the program will do the correct tool construction plane."
For more information contact:
Houston Mold & Tool, Inc.
290 Derrick Drive
Humble, TX 77338
281-548-0155
CNC Software, Inc.
671 Old Post Road
Tolland, CT 06084
800-228-2877
info@mastercam.com
www.mastercam.com
SOUTHWEST ONLY
MLC CAD Systems
10777 Northwest Freeway
Suite 175
Houston, TX 77092
www.mlc-cad.com