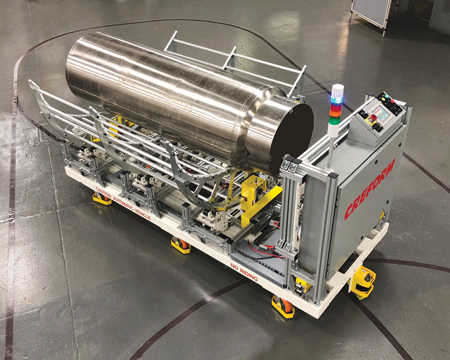
Creform designed and built this AGV to handle large cylinders.
Creform Corporation engineers have designed and built a custom AGV to handle the transport of large pressure fuel cylinders during manufacturing. The one-vehicle, bi-directional AGV will be used by the customer to move the cylinders between five assembly and two finishing stations.
Creform designed and built the AGV on a custom frame that measured 8.2' long x 3.28' wide (2.5 M x 1 M). The company also designed the system controls as well.
The AGV features a custom designed cradle, lined with plastic to avoid damage, to hold and position the cylinder. The cradle features a locking pin that rises automatically to ensure the cradle's position during transport. It features electrically-powered 100° rotation travel with three stop positions - one to load, one to transport and one to unload. Loading is operator initiated and route-directed with the use of an HMI screen all intended to ensure safe handling, while the unloading is automatic. The AGV was purposefully designed to replace a manual cart and to enhance production efficiencies of automation and safe handling for both the product and the associate handling.
The FH-C25100, bi-directional AGV, designed and fabricated with a steel frame for strength and durability, comes equipped with a Creform bolt-on drive unit. Each end of the AGV follows a peel and stick magnetic tape guidepath to help ensure accurate and repeatable tracking. This is particularly useful for space restrictive areas and allows repeatable alignment for the consistent transfer of loads. The guidepath is easily and quickly installed and allows for easy path change or when a repair is needed. The unit is able to travel at speeds up to 82 FPM (25 M) and has a load capacity of 2,200 lbs.
The 24-volt AGV is powered by two 12V, 160AH, AGM batteries. The unit contains side mounted opportunity-charging shoes that help to automatically maintain battery level. There is no need to cut into the floor for charging plates and the shoes are less expensive to install and more flexible if there is a need to reposition. The AGV has a powered engage/disengage to raise/lower drive wheels. When the drive wheels are elevated, AGV can be easily repositioned by an associate.
For this customer, the AGV follows an approximate 100' guide path. The main path is a straight line but can travel laterally, in places, to position for transfer.
The unit features complete safety equipment for safety category 3. The safety equipment includes: Laser obstacle scanners front and rear with 16 settable zones; E-stop buttons at each end of the AGV; safety light and audible warning. It features cylinder position photo eyes for cradle control and to detect an unexpected load shift during transport.
The Creform System is used to create an array of material handling and efficiency enhancing devices and is a proven component in continuous improvement and Lean Manufacturing programs. The company partners with customers in developing and implementing these programs.
For more information contact:
Creform Corporation
P.O. Box 830
Greer, SC 29652-0830
800-839-8823
SCsales@creform.com
www.creform.com