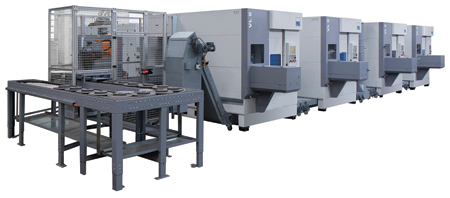
Production line for brake disc machining: users benefit from a robust solution with short downtimes.
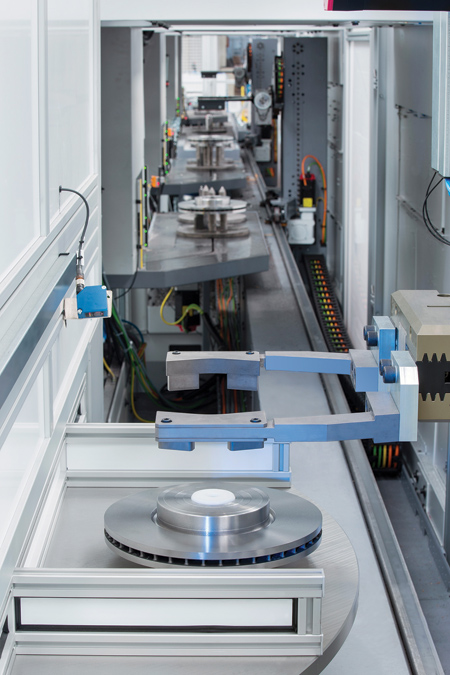
Machines are interlinked by TrackMotion. It is possible to switch out a machine from the process if not all steps of the operation are required for the workpiece.
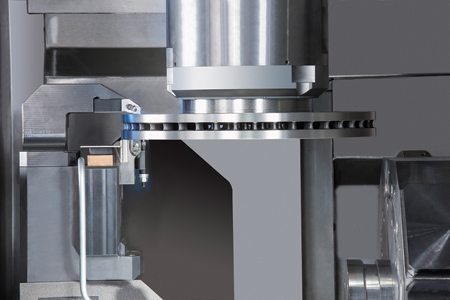
Fine machining of friction ring faces is done by parallel processing of both surfaces with a straddle tool.
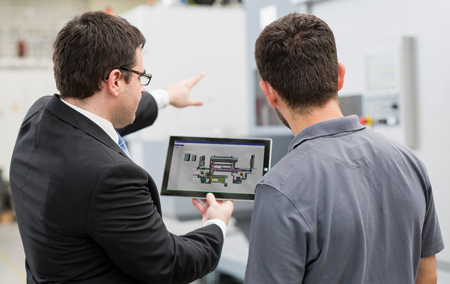
Industry 4.0 technology plays an important role at EMAG. For example, the "EMAG Fingerprint" software can diagnose wear of the axis drives at an early stage.
Manufacturing car brake discs is challenging: on one hand, these safety-relevant components must be produced both reliably and with extreme precision. On the other hand, there is immense pressure on minimizing costs. The changing production batches must run through the turning centers at high speed and with short set-up times. How can quality, productivity and process reliability be combined in this application?
"This has been demonstrated for decades by the EMAG specialists," said a company spokesperson. With its pick-up turning centers of the VSC and VL Series, it offers production solutions that provide, in combination with the TrackMotion automation concept, performance leaps in brake disc machining. Another relevant fact is that some EMAG machines have been in operation for decades. Users benefit from a robust solution with short downtimes. This means that unit costs are also decreasing."
The rapid technological advancement in automotive manufacturing has also been benefiting the brake disc, one of the important safety-relevant components in the car. For example, the quality of the cast blanks has significantly increased in recent years. In addition, compound brake discs are being used increasingly. They consist of a gray cast iron friction ring and a steel or aluminum bowl, which helps to reduce overall vehicle weight. As a result, the machining process is changing as well. Therefore, users in the spare parts market in particular are looking for very flexible machining units that can be retooled for new workpieces without long downtimes. At the same time, OEMs are experiencing heavily increasing unit volumes in brake disc production due to platform strategies. The costs per piece in large-volume production are especially in focus.
How can machinery manufacturers respond to all these different demands? "First of all, by having an extremely flexible machine and automation concept available," said Martin Abendschein, Technical Application Manager for the brake disc business unit at EMAG. "Our main focus of attention is the VSC and VL machine series with vertical pick-up spindles. Their modular technology can be configured to custom-fit any requirements, and can be easily combined in a production line. Customers end up with a highly flexible overall solution that they can retool for new parts in a very short time, resulting in a massive decrease of downtimes. For brake discs in particular, this is a decisive factor since the actual machining times can hardly be improved anymore due to the physical limits of the clamping devices, in spite of higher performance potentials of the cutting materials."
TrackMotion Offers Flexibility
A closer look at the line structure reveals the exact function of the highly flexible EMAG production solutions: inside-ventilated front-axle brake discs are usually machined in four clamping operations - performed by four spindles, or machines. These machines are interlinked by the proprietary EMAG TrackMotion system. In this automation system, a track-mounted gripper unit moves in a linear fashion. It transports the workpiece from the blank infeed via the individual machines and process steps to the finished part outfeed. A special advantage is that users can modify the overall system at any time. Time-consuming retooling for different clamping devices is reduced to a minimum. On the other hand, EMAG can integrate several machines into the chain to perform the same operation in parallel. In this case, the TrackMotion system distributes the workpieces to the machine that is free at the moment. Tooling work on a machine never means downtime for the entire production line.
Features for Finish Machining
Further benefits are provided by the individual VL and VSC machines, which can also be combined in different sizes, e.g. if different components such as a gray cast iron friction ring and an aluminum bowl are processed in the same production line. Short cycle times are ensured by quick loading with the pick-up working spindle, along with high linear feedrates and short turret indexing times. All models also have machine bases made of Mineralit with enhanced vibration damping.
The fine machining of the friction ring faces is generally done by parallel processing of both surfaces with a straddle tool. This tool has to be integrated into the process with maximum possible stability in order to prevent vibrations at the tool, which would result in loss of quality. "Here we have a very special feature," Abendschein stated. "In addition to the classical mounting of the straddle tool on the tool turret, EMAG offers the alternative option of placing it on a special console inside the machining area. This results in perfect damping and, consequently, high surface qualities and minimized thickness variations." In addition, an SPC station for statistical process control is available as standard on every EMAG VL machine. With this station, the user can check the quality of the parts directly at the machine. In the meantime, the production line keeps running. EMAG offers a wide range of configuration options and variable detail solutions. In addition, many accompanying processes, such as marking, balancing or measuring, can be easily integrated into the line design. In addition to the TrackMotion system, other concepts for automation are available, including pick/flip and place units, or line gantries.
Intelligent 4.0 Solutions
Industry 4.0 plays an important role at EMAG - for example, when it comes to maintenance. The "EMAG Fingerprint" software can detect wear of the axis drives at a very early stage and with little effort, so that necessary maintenance tasks can be planned in advance. Lifetool-Analytics allows checking the condition of driven tool units via smartphone app.
"Flexible, fast, precise and highly productive at the same time - on the basis of these criteria, EMAG has achieved an excellent market position in the area of brake disc machining over the last few decades," said Abendschein. "Another relevant fact is that these machines are extremely robust. Some have been in operation for decades. This is a decisive advantage, and our customers know and appreciate it. In addition, we have a worldwide service network. Whenever needed, we are quickly on site with our own service engineers. We want to continue to target these benefits to the market in the years to come."
For more information contact:
Kirk Stewart
Sales Director
EMAG L.L.C.
38800 Grand River Ave.
Farmington Hills, MI 48335
248-996-4703
kstewart@emag.com
www.emag.com
SOUTHWEST
TX, OK, AR, LA
Eric Klenner
Regional Sales Manager
EMAG L.L.C.
248-595-1530
eklenner@emag.com
SOUTHEAST
MS
Eric Klenner
Regional Sales Manager
EMAG L.L.C.
248-595-1530
eklenner@emag.com
NM
Shane Cross
Regional Sales Manager
EMAG L.L.C.
248-207-5365
scross@emag.com
VA, NC, SC, FL, GA, AL
Dave Fitzgerald
Regional Sales Manager
EMAG L.L.C.
248-595-1117
dfitzgerald@emag.com
TN
Mark Comeaux
Regional Sales Manager
EMAG L.L.C.
248-938-2097
mcomeaux@emag.com
NORTHEAST
WV
Mark Comeaux
Regional Sales Manager
EMAG L.L.C.
248-938-2097
mcomeaux@emag.com
ME, NH, NY, PA, MA, RI, CT, NJ, DE, MD, VT
Kevin Gadde
EMAG L.L.C.
248-938-2430
kgaddet@emag.com
MIDWEST
OH, KY
Mark Comeaux
Regional Sales Manager
EMAG L.L.C.
248-938-2097
mcomeaux@emag.com
ND, SD, NE, KS, MN, IA, MO
Bill Konetski + Cat/John Deere
Regional Sales Manager
EMAG L.L.C.
612-804-0857
bkonetski@emag.com
IL, N. IN
Tod Petrik
Regional Sales Manager
EMAG L.L.C.
248-470-2646
tpetrik@emag.com
MI
Mark Ashworth
AAM, MPG
EMAG L.L.C.
248-826-4242
mashworth@emag.com
WI
Joe Thompson
Regional Sales Manager
EMAG L.L.C.
248-880-0233
jthompson@emag.com
WEST
WA, OR, CA, NV, ID, MT, WY, UT, CO, AZ
Shane Cross
Regional Sales Manager
EMAG L.L.C.
248-207-5365
scross@emag.com