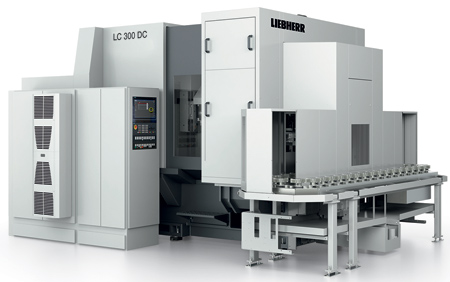
Gear hobbing machine LC 300 DC with integrated ChamferCut unit
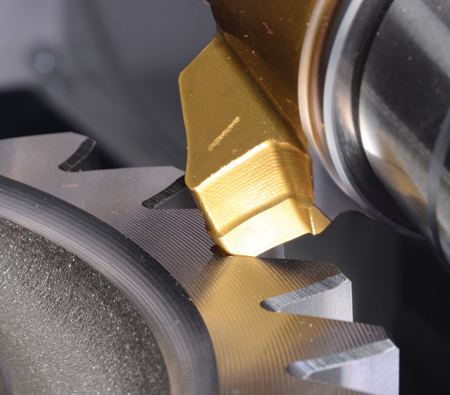
The Liebherr solution: simultaneous chamfering
"For years, ChamferCut has been a suitable and efficient solution for deburring and chamfering. In addition to the LD 300 C, the new stand-alone solution LD 180 C from Liebherr offers new opportunities for introducing the method in existing production lines," said a company spokesperson.
Clean-edge gear teeth prevent damage during workpiece transport, hardness cracks and gear wear. They also facilitate the assembly process and improve the tool life. "Chamfering using ChamferCut delivers high-quality edges with reproductive accuracy, and is more cost-effective than press deburring and chamfering with tapered end mills," said the spokesperson. "Chamfering is popular among car and commercial vehicle manufacturers as well as in gear and engine manufacturing."
Solution for Existing Production
"When planning new production lines, our customers generally decide on an integrated solution of gear hobbing and ChamferCut to save installation space," said Dr.-Ing. Oliver Winkel, Head of Application Technology. "However, many users also want to incorporate this efficient method into their existing production. We therefore developed the LD 180 C and LD 300 C for them." This way, every user can use this technology: the version with workpiece diameter up to 180 mm is designed for the automotive area. Machines with a diameter up to 300 mm are generally more suitable for contract gear manufacturers and the truck sector.
The developers paid special attention to minimal size and maximum flexibility of the new machines. Because the installation area is restricted in existing lines, the machine and control cabinet can be positioned separately as an option. "This increases the set-up possibilities in halls with limited space," said Dr.-Ing. Hansjörg Geiser, Manager of Development and Design of Gear Cutting Machines. The machine can also be operated from the right or left. "This mirror image version enables an even better integration option in existing production lines," he said.
Automation
The developers were careful with the automation to ensure that the machine can be integrated in every environment. The loading can be effected by belts, robot cells or other automation solutions. "During the development stage, we listened to our customers and customized the machine to their requirements," said Winkel.
Similar to all Leibherr solutions for the ChamferCut method, the LD 180 C also works with maximum productivity in order to provide very short cycle times. It can machine small to medium workpieces with a diameter up to 180 mm and length of 200 mm. "Although precise chamfers are created with the ChamferCut method, the lowest tool costs are still incurred, which shortens the amortization period considerably," said the spokesperson.
The LD 180 C and LD 300 C can handle both wet and dry machining, and have a high tool life with both machining types. The machines have simple and intuitive controls, which can be easily programmed with the user prompts.
Advantages of the method include:
For more information contact:
Liebherr Gear Technology, Inc.
1465 Woodland Drive
Saline, MI 48176-1259
734-429-7225
info.lgt@liebherr.com
www.liebherr.com