
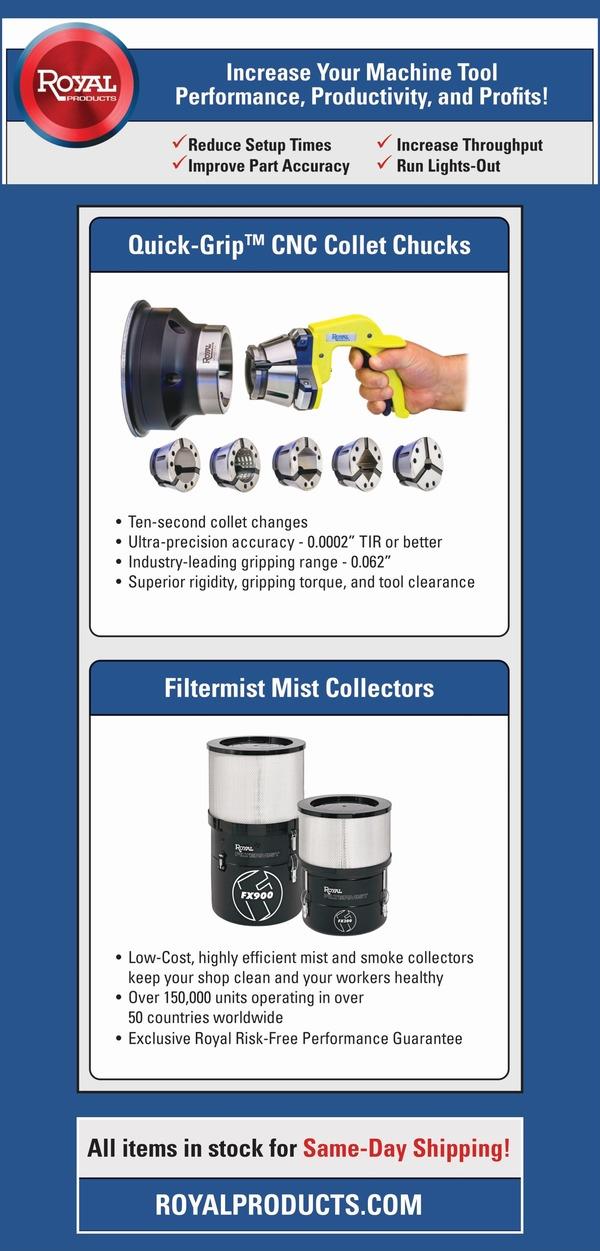
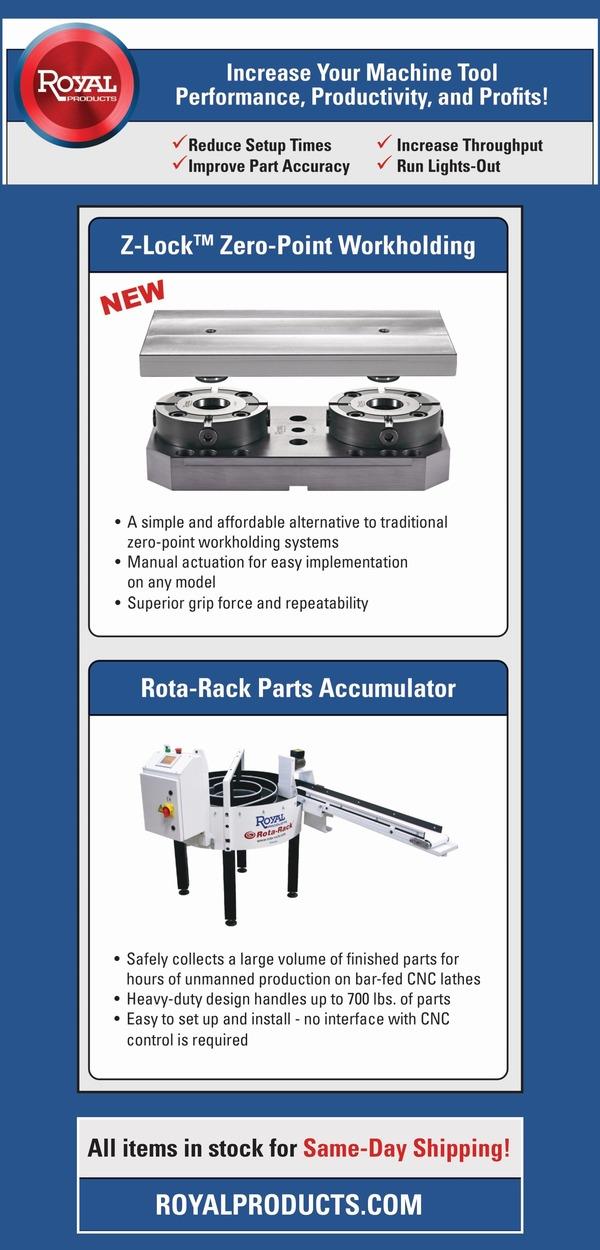

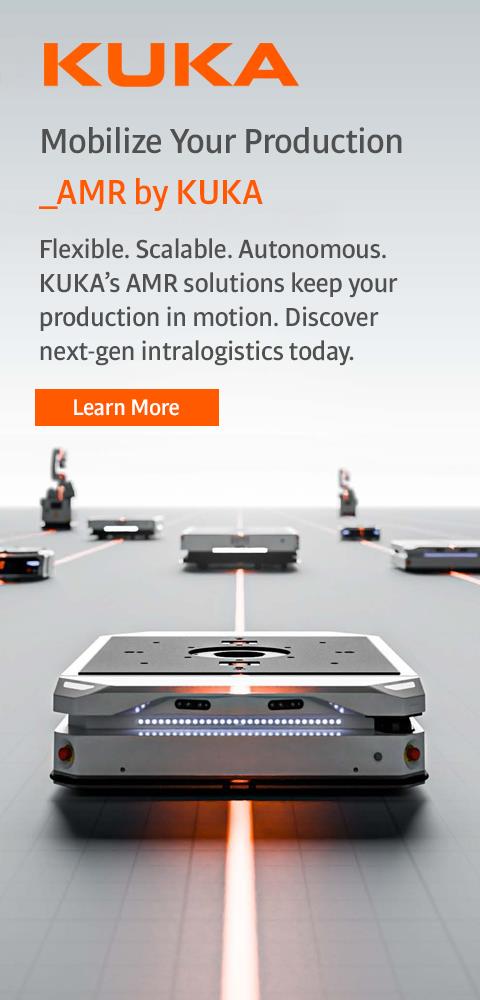
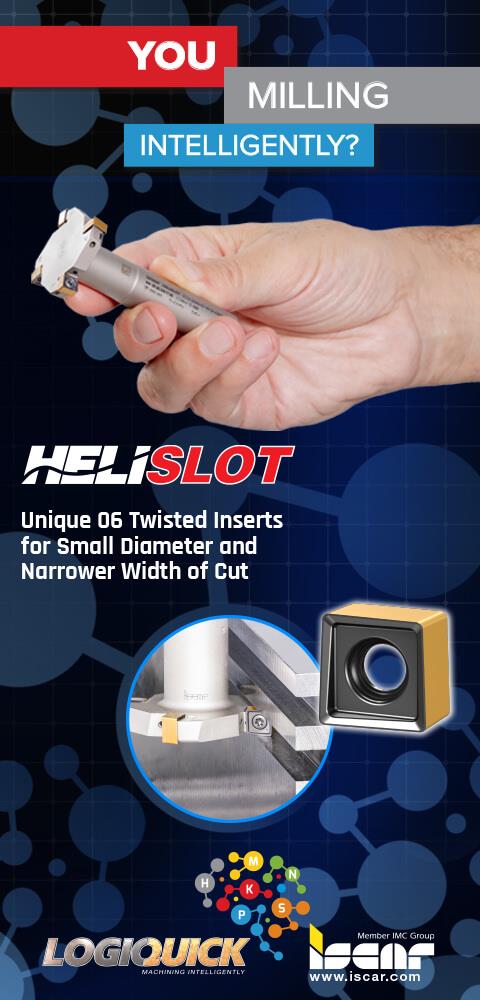
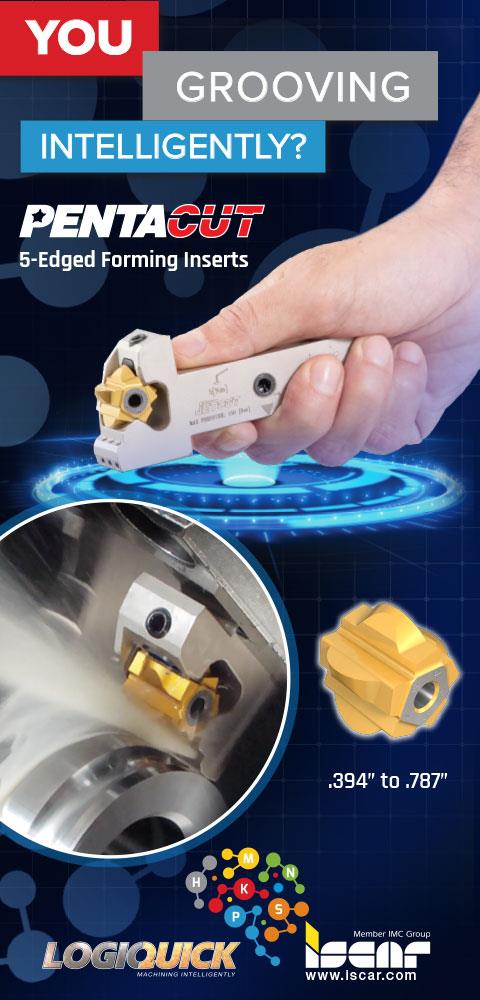
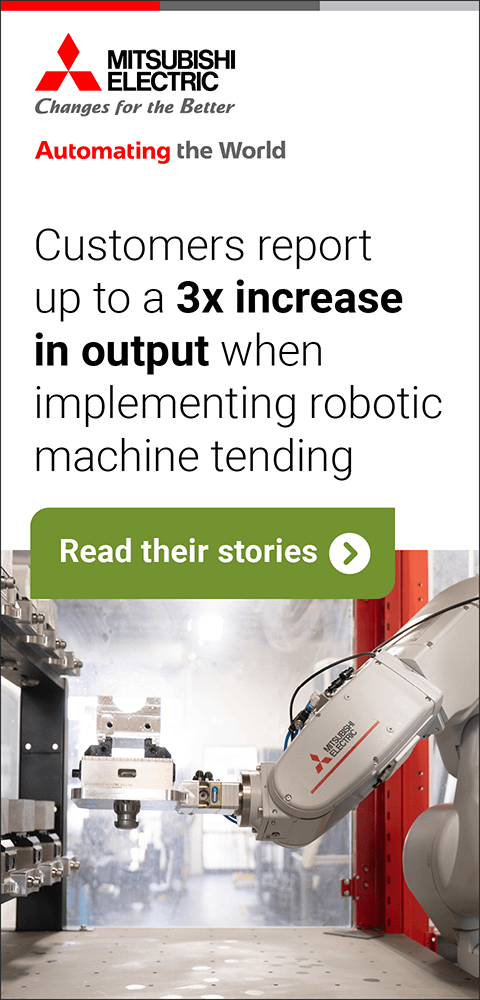
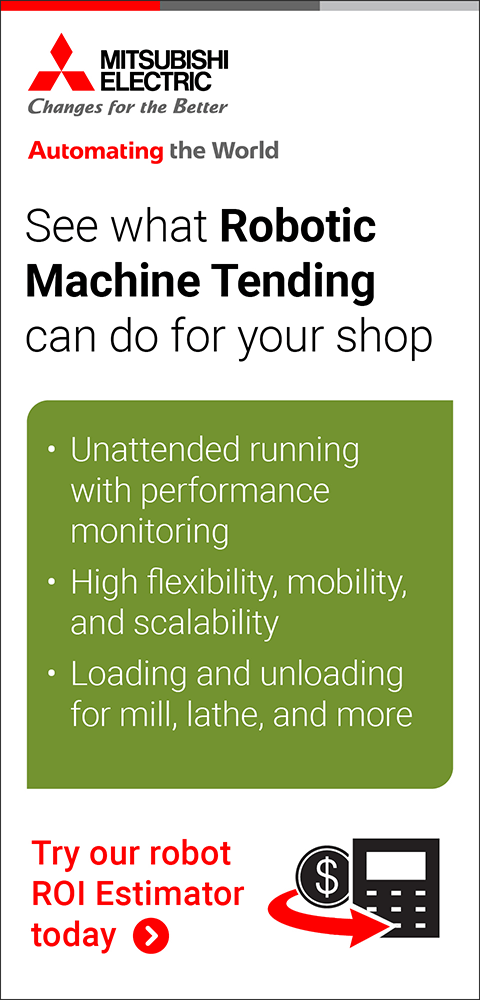
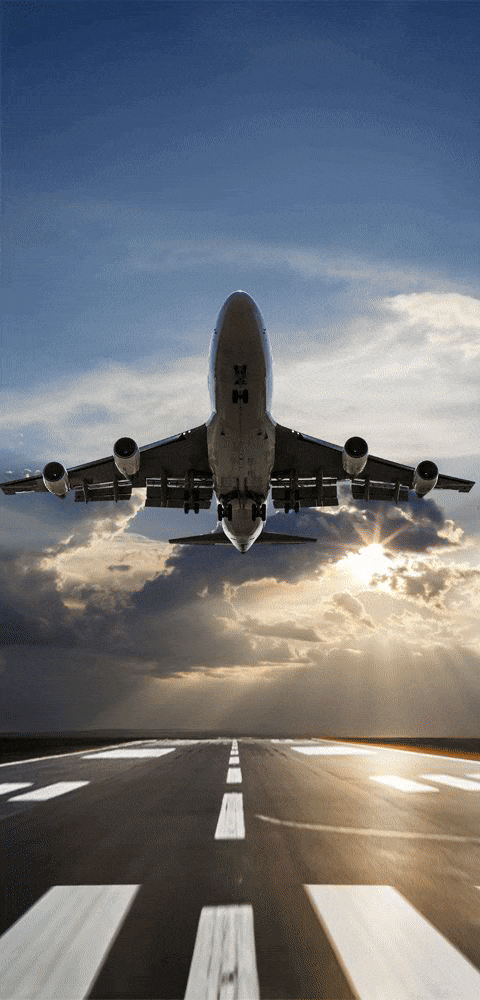
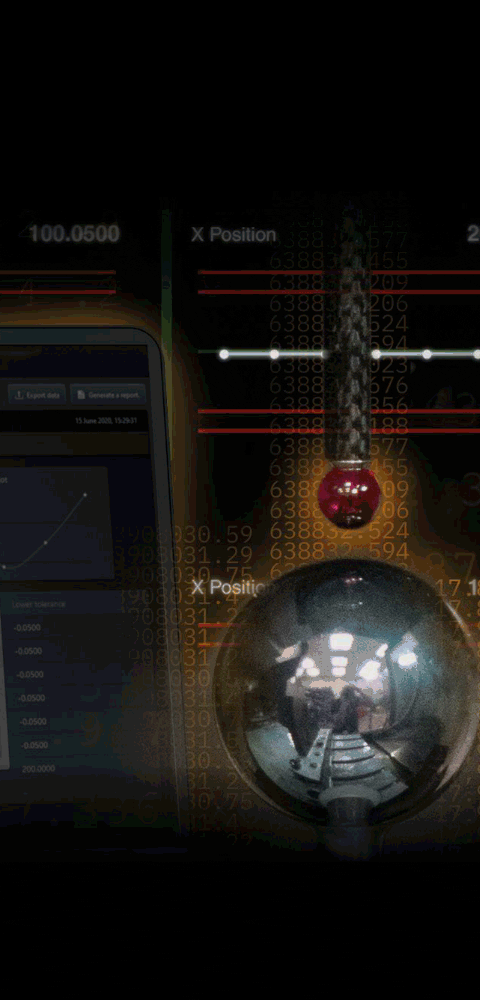
Indexable Milling Grade for Enhanced Productivity
May 1, 2018
"Customers have been asking for a new carbide grade to machine Titanium 6Al4V at higher cutting speeds compared to increasing feedrates or increasing depth of cuts in that result in increased cutting forces imposed on the workpiece, fixtures and machine spindles. The KCSM40 grade has an advance cobalt binder that provides exceptional thermal fatigue resistance without sacrificing the toughness customers have experienced with KC725M or X500. In addition to the new material substrate Kennametal's proprietary AlTiN/TiN coating enhances the wear resistance at the cutting edge," said a company spokesperson.
"We took the toughness of our most popular milling grades KC725M and X500 and increased the thermal crack resistance and wear resistance that will enable our customers to machine at higher cutting speeds without sacrificing toughness," said Scott Etling, Director of Global Product Management, for Indexable Milling at Kennametal.
The target cutting speed for KCSM40 in Ti6Al4V was 175 SFM (53 m/min) while achieving a greater than 20 cubic inches per minute (327 cm^3/min) metal removal rate for 60 minutes. Not only has KCSM40 achieved this but has results milling titanium at speeds up to 270 SFM (85 m/min) at a lower radial depth of cut.
Etling said the radial engagement of the milling cutter to the
workpiece is one key component when optimizing the cutting speed. "At higher radial engagements, the insert is cutting the material for longer time, which creates more heat at the cutting zone. The heat will not go into the titanium chips like when milling steels so controlling the heat is critical. Lower cutter speeds at higher radial engagements is a good practice. At lower radial engagements, higher cutting speeds can be achieved."
Recent internal testing with the new HARVI Ultra helical milling platform achieved over 100 minutes of tool life running at 155 SFM (47 m/min) with a .0067 ipt (.12 mm/t) chip load. The radial depth of cut was 1.0" (25 mm) and the axial depth of cut was 3" (76 mm). Etling stated, "The edge condition on the KCSM40 grade still looked great. In one face milling operation on a hardened steel wear plate the number of passes was reduced from 234 to just 22."
The development of KCSM40 was targeting Ti6Al4V but it will perform well in other high temperature / heat resistant materials. The KCSM40 is suitable for aerospace (aero structure and engine components), energy (turbine blades and parts made from duplex stainless steels) and transportation (turbo chargers) segments.
For more information contact:
Kennametal Inc.
1600 Technology Way
P.O. Box 231
Latrobe, PA 15650
724-539-5000
www.kennametal.com
< back