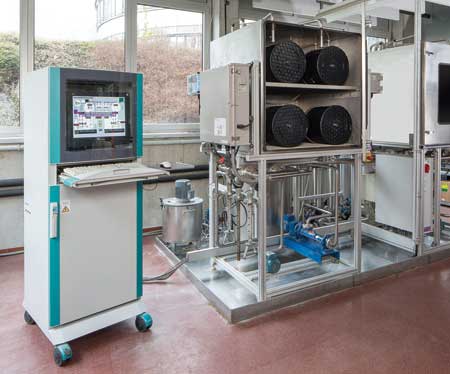
The filter is loaded with a high equal load of standardized test dust. Then the long-term properties of the filter medium itself and the structure of the filter such as the end caps and outer casing are tested.
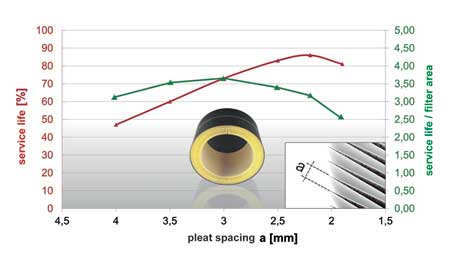
The diagram shows that as expected a higher packing density lengthens the service life and when the pleat pitch is too small the service life shortens again (red curve in the diagram).
There are a number of different factors that complicate an absolute comparison of EDM filters in relation to dirt holding capacity, filter fineness, service life and installation space. MANN+HUMMEL is working on a concept to classify EDM filters according to efficiency classes.
In recent years EDM technology has enabled an ever higher surface finish quality of the parts produced. This is due to improvements in the process and machine, including improved filtration of the dielectric fluid. Various factors and their interdependency make it difficult for the user to identify the efficiency of a filter and to use the filter in the respective process to achieve the required surface finish quality. Thanks to standardized measurement procedures, the separation efficiency, for example, of air cleaners and fuel filters is known, whereas up to now in the field of EDM clearly defined comparison methods have been missing. One solution would be to introduce efficiency classes on the basis of the measured dirt holding capacity under consideration of the installation space available to the filter.
The dielectric fluid has several tasks to manage during the erosion process. It insulates the workpiece from the tool (electrode), provides the necessary cooling during the machining process and flushes away the removed metal from the erosion gap. If the finish quality of the workpiece deteriorates, the reason is usually that the purity level of the dielectric fluid has gone down due to insufficient filtration. A further complication is that with new power generators the gap size is reduced. This improves the finish quality but the particles removed are becoming smaller. The introduction of efficiency classes for EDM filters will make it easier for end users to select the right filter for the respective requirements. A service life measurement procedure already used internally at MANN+HUMMEL GMBH indicates which criteria are relevant for the efficiency classes and what a standardized solution might look like.
Online Monitoring of the Turbidity Level
The influence the filtration of the dielectric fluid has on the EDM process is shown by parameters which are directly or indirectly influenced by the filtration. One of these is the separation efficiency and a measure of the particle sizes retained by the filter. It has a direct effect on the purity of the dielectric fluid and therefore also on the creation of the sparks in the working area. The separation efficiency can only be determined by a complex measurement process, as it is necessary to select and count the particles which have passed the filter. It is considerably easier to measure the turbidity level of the fluid. The turbidity level directly reflects the number and size of the particles in the fluid. At MANN+HUMMEL the turbidity level is currently measured using an optical process which has already proven itself in the online monitoring of water quality. It measures the ratio of reflected to introduced light. The result is given in nephelometric turbidity units (NTU).
The filtration which takes place in the filter media is usually a deep-bed filtration where solids penetrate the filter material and are retained. In standard filters the full performance is only achieved after a corresponding amount of dirt has been taken in and embedded. The aim is therefore to achieve the required separation performance, i.e., the required quality, as quickly as possible after a filter has been changed. On the other hand the continual build-up of the filter cake increases flow resistance. This increases pressure and also results in a difference in the pressure between upstream and downstream of the filter. This in turn increases the power consumption of the pump.
Improving the Deep-Bed Filtration
The differential pressure depends on the composition of the embedded dirt and also on the filter medium itself and its structure. With an efficient filter, the differential pressure increases slowly over the service life during the deep-bed filtration process in spite of the volume of dirt increasing. After the start of surface area filtration, there is an exponential increase in the differential pressure up to the maximum load. With lower quality filters, this transition takes place significantly earlier.
Further parameters which influence the dielectric fluid are the ion induced and the dirt holding capacity. The ion induce results from the impregnation of the filter medium and the decomposition products from metal filters (rust). It changes the conductance value of the dielectric fluid which has to be compensated by the addition of deionizing resin. This increases costs. The dirt holding capacity describes the volume of dirt which a filter medium can absorb in relation to a square meter and forms the basis for the service life and therefore the operating efficiency of a filter.
Standardized Test Procedures for EDM Filters
In order to identify the named influences on the EDM process and make them comparable, MANN+HUMMEL has developed two standardized tests. The objective is to determine in a reproducible process the efficiency of an EDM filter on the basis of the measured dirt holding capacity under consideration of the filter installation space. During the service life test, the filters are tested on an EDM machine up to a defined differential pressure. In order to make the loading process comparable, steel is continuously cut using the same wire material, the same workpiece metal and fixed machine parameters. This results in a given volume of dirt which is the condition for a comparison of the service life of different filter systems. Furthermore, the turbidity level of the dielectric fluid after the filter is measured online to allow a conclusion to be made about the separation efficiency.
In the second test, the load test procedure, the filter is loaded with a high equal load of standardized test dust. Then the long-term properties of the filter medium itself and the structure of the filter such as the end caps and outer casing are tested.
Advantages of Progressive Pleating
The selection of a suitable filter medium and the best use of the available installation space are important factors to increase the service life of a certain filter size. For this purpose a series of tests is carried out to establish the ideal distance between the pleats and the resulting packing density of the filter medium. As expected, a higher packing density lengthens the service life and when the pleat pitch is too small, the service life shortens again. Therefore, if the pleats are packed too tightly, the filtration performance goes down again.
If one examines the complete filter area, which on the market is frequently given as the main factor for the efficiency of the filter, against the determined service life, the ideal pleat distance is clearly visible. This means that the filter area alone, which depends on the distance between the pleats, does not indicate a long service life. In this respect the question has to be asked how one can integrate the largest possible filter area with ideal pleat partition in a given installation space.
The optimization of the pleats was a long process. The first step was a single bellows, followed by an M and W shaped pleating. Then came the double bellows which was followed by the latest development from MANN+HUMMEL, the triple bellows with progressive pleating. The installation space here is filled with three areas each having a different pleat length. This enables excellent exploitation of the installation space. In addition, standard service life tests indicate better results than achieved by bellows with other geometries. MANN+HUMMEL is currently the only company which offers this pleating arrangement for the field of EDM. In order to further avoid the influences of metal materials, the end caps and outer casing are made from plastic.
Influence of the Fiber Structure
In addition to the ideal pleating, the fiber material used represents an important factor with regard to the quality of the filtration. In the field of EDM filtration mainly cellulose fibers have been used. However, these are disadvantageous as due to their impregnation against the effects of water and oil, they increase the ion penetration of the dielectric fluid. This is not the case with synthetic filter media. They also have other advantages due to their small fiber diameter and their typical uneven distribution. Firstly, with the same flow resistance and same load thin synthetic fibers with an irregular structure, i.e., small and large pores separate more particles than thick fibers do with an even structure. Secondly, very small particles are separated quicker, which considerably reduces the initial turbidity when the filter is changed. This means that with a synthetic material the dielectric fluid is clear again shortly after the filter has been fitted. The filtration performance therefore depends not only on the filter fineness, but also significantly on the type of fiber and its structure.
The fully synthetic filter medium used by MANN+HUMMEL consists of a carrier layer on which a thin synthetic filter layer is placed. The result of combining triple progressive pleat geometry with this synthetic medium is an EDM filter with a service life up to 60% longer than a standard filter medium with a single pleat.
Efficiency Classes for Each Installation Space
Measurements show that each filter with a certain type of fiber, structure and bellows geometry has its own optimum performance in terms of dirt holding capacity and therefore the service life. A desired characterization of EDM filters for certain applications only based on filter area and filter fineness is therefore not possible. In other industrial fields, on the other hand, efficiency classes were introduced a number of years ago to offer a method of comparison. For example, for fridges this is already standard and has led to the development of more efficient products. The same is true for the automotive industry. The CO2 efficiency of a car is based on the measured emissions under consideration of the mass. If this concept is transferred to EDM filtration, then the efficiency of an EDM filter is based on the size of the filter installation space and the measured dirt holding capacity.
A first idea for the classification, for example, is as follows: 90% of 1 to 2 um particles are separated with filter efficiency B and 90% of 3 to 5 um particles are separated with filter efficiency A. With the introduction of efficiency classes for the different separation efficiencies of EDM filters under consideration of the installation space, it is now finally possible to compare filters. The condition is a standardized service life measurement process which is similar to the one already used at MANN+HUMMEL internally. This enables the end user to select an EDM filter especially for his or her requirements and determine the service life and costs himself or herself.
The Next Step
MANN+HUMMEL is currently working with RWTH Aachen University on a possibility to transfer these tests to a number of machine types and manufacturers. The objective is to create a general guideline for EDM filter tests which will enable classification according to the efficiency classes.
Authored by MANN+HUMMEL
For more information contact:
MANN+HUMMEL Purolator Filters LLC
801 Corporate Center Drive, Suite 128
Raleigh, NC 27607
919-926-4200
info-us@mann-hummel.com
www.mann-hummel.com