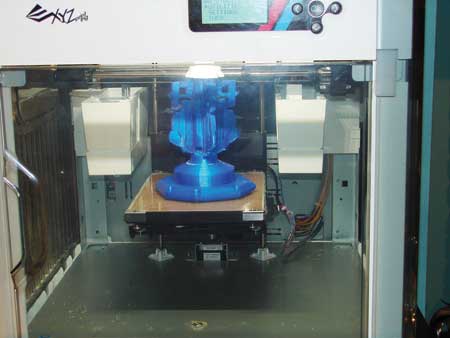
One of Royal Machine's DaVinci 3D printers produces a model of a workholding fixture.
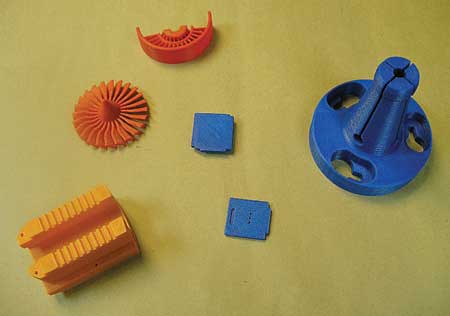
Chuck and collet components are produced using Royal Machine's DaVinci 3D printers to make parts and components prior to actual manufacturing.
Since the beginning of manufacturing, craftsmen have honed their skills in fitting jaws or work nests to securely grip a part. Handed down from their predecessors, these special craftsmen's skills were developed though years of experience.
Unfortunately, throughout the years these specialized types of work skills have diminished, resulting in specialized craftwork not having been handed down from one generation to the next. This created a large void in the workholding industry in continuing shortfalls in finding skilled craftsmen.
3D printing has taken on the role of the craftsmen. Today, we can develop a solid model of the part and the workholding simply by downloading the data and creating a plastic model.
This alone eliminates a combination of highly unprofitable time, trial and error that usually takes place in the fitting of chuck jaws or a work nest on a machining center fixture.
Through success and failure, Royal Machine & Tool has learned the benefits of this new technology and how to apply it to our workholding processes. Taking a series of "baby steps" approaches, our engineering and manufacturing initially learned to grasp 3D technology and understand its processes. Then we looked at products made of plastics that could be manufactured using 3D technology.
The next step was to produce actual parts made of plastic. Royal Machine's engineers had also been developing prototype chuck jaws and workholding fixtures from concept to actual configurations. This development process has shown the many benefits of the 3D printing and how it could apply to the design and manufacturing of workholding products.
Workholding Design and Manufacturing Benefits
Intricate chuck jaws for very difficult forgings or castings can now be manufactured in plastic and tested for fit before going to the expense of machining. In the past, this operation was done in the final fitting and, in some cases, required welding up the jaws to fit after initial machining. With the aid of 3D printing, development time is greatly reduced. Any corrections in the design can be remedied prior to manufacturing.
Everything can look great on paper, but once manufactured, a number of problems can be exposed. Correcting them can be costly and time consuming. Making a 3D model allows you to see how well the part will hold, resolve any interferences that may occur with tooling, and look at the integrity of the chuck jaws.
Royal Machine has also experimented in making plastic models of machining center fixtures. Again, the benefits of making a mock-up version in plastic has exposed the fixturing to modifications earlier in the process, reducing costs and time in the development stage. The plastic mock-up also helps detect interferences with loading/unloading, clearance for adjustment, chip evacuation and tool clearances.
These are many of the factors that may not show up in the design process. However, once the fixture is manufactured, and delays in assembly and alterations to existing components occur, waste and costs are quickly added to the project.
There is still much more to learn as far as applying this 3D technology to our major workholding products and our everyday manufacturing processes. Moving forward with continuous improvements and keeping up with the latest advancements in our industry, Royal Machine is now looking at a new 3D scanner to complement our 3D printing applications.
Authored by Bernie McAloon, Vice President, Royal Machine & Tool
For more information contact:
Bernie McAloon, Sales Manager
Royal Machine & Tool Corp.
P.O. Box Y
4 Willow Brook Drive
Berlin, CT 06037
860-828-6555
royal@royalworkholding.com
www.royalworkholding.com