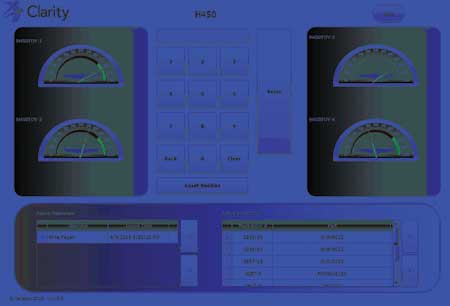
An Operators Dashboard Display is located at each work center and provides live feedback.
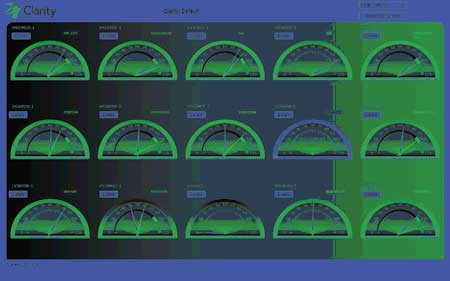
The Manager's Dashboard displays the gauge for each work center, driven by live data.
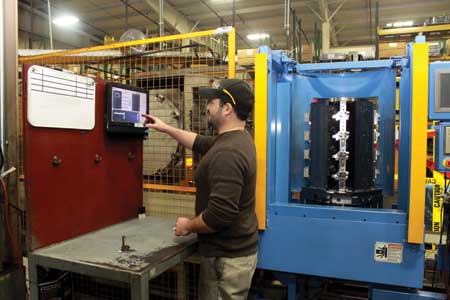
Dashboard Display at the work center.
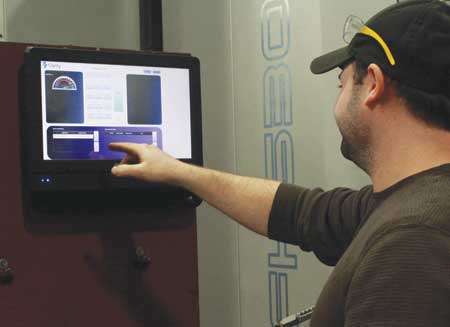
Dashboard Display at the machine.
Clarity Live Production Monitoring was developed by a team of factory owners to address ways to manage operators and their managers with live production data feedback.
With Clarity Live Production Monitoring, operators are getting live feedback as to how they are producing compared to the production standards. This is displayed on the Operators Dashboard, which hangs at each work center. This instant feedback gives them the opportunity to meet or exceed expected standards and allows productive operators the opportunity to achieve maximum throughput and be recognized for it. Each of the work centers is directly connected to the Clarity server. Clarity then reads each cycle directly from the equipment. Stored in the Clarity database or shop ERP, all production standards are stored by part number. As each cycle of the equipment produces a part, Clarity compares production pace to the standard and displays how the operator is doing (gauge, 0-120%) compared to these predetermined standards. Therefore, operators can know within the first hour of their shift if they will make the more or less than the acceptable number of parts for their shift. This leaves them hours to pick up the pace if they see they are not measuring up to expectation. "No longer is an employee judged by yesterday's production reports when there is nothing that can be done about inferior production quantities," said a company spokesperson. "Now, operators are empowered to achieve their target, with instant feedback."
Managers can also see how each work center is performing right on their desk. The Manager's Dashboard, driven by live data, displays the gauge for each work center. If mangers see one work center not achieving acceptable levels of output, they have the instant knowledge to determine if they want to go and see if improvements can be made. In most cases, a manager can correct the issue and help the operator get back up to the correct rate.
"With Clarity, not only can operators and work centers be held accountable to standards, but also departments, cells and shifts," said the spokesperson. "Any combinations of work center gauges can be rolled up into one gauge. This will enable higher level managers to get a quick, live snapshot of performance."
There are additional features that Clarity offers the entire organization. Clarity offers 40 user-defined Reason Codes to enable operators to indicate what issues are stopping their equipment. Each event is stored and can be tallied up to review what top issues are affecting a plant's overall production. Any of these Reason Code buttons can also be used as a call button to call for a supervisor, material or any other personnel. Each button can initiate a text or e-mail to a designated employee.
Also, set-up times are now stored by part number and displayed at both the Operator Dashboard and the Manager's Dashboard. When the standard set-up time has been passed, management knows to go lend a hand to get the job running.
In addition, Clarity is a web-based application and can be viewed from anywhere.
"These are just a few of the features Clarity offers," said the spokesperson. "Each of these features aims to bring accountability to an entire production floor and yield greater production on average. No manufacturer that has installed Clarity, has seen less than a 10% gain and as high as 25% across the entire plant. Managing a production floor with live data is the only way to keep all personnel focused on the goal of the organization - to produce as many parts as processes can achieve."
For more information contact:
Clarity Monitoring
800-770-4229
info@claritymonitoring.com
www.claritymonitoring.com