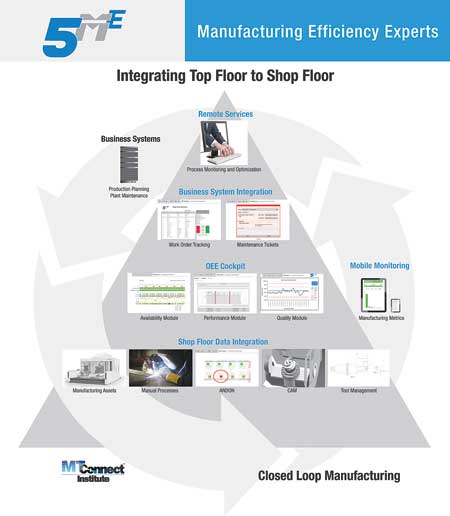
5ME addresses the five "M's" of man, material, machines, methods and metrics to improve a manufacturing enterprise's efficiency (the "E").
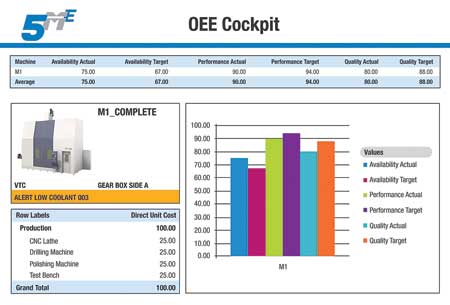
The Freedom eLOG software makes manufacturing assets - and their production potential - transparent in real time to all levels of management, complete with performance metrics.
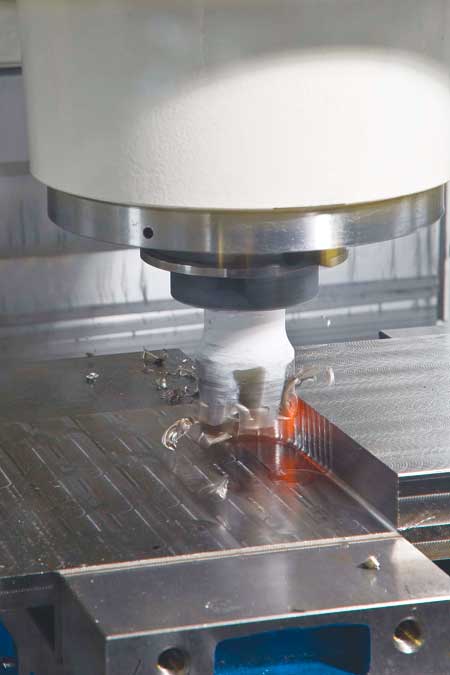
5ME's cryogenic machining process is designed to provide higher cutting speeds for increased material removal and longer tool life by transmitting liquid nitrogen at -321°F through the spindle/turret and tool body, direct to the cutting edge.
5ME, a newly developed business comprised of the non-machinery units of the former MAG IAS, has been launched to help manufacturers, regardless of size, find hidden profits in production operations.
Led by President Bill Horwarth and other top managers, engineers and employees from the former company's tooling, services and software businesses, 5ME offers capabilities focused on increasing customers' manufacturing efficiency as a means of building profitable, competitive and sustainable businesses. The company has management operations in Cincinnati and Detroit. Detroit is also the home of 5ME's new technology center that features cryogenic machining, tooling/fixturing, process development, asset monitoring and enterprise software, as well as embedded assistance.
5ME addresses five critical components - the five "M's" of man, material, machines, methods and metrics - to improve a manufacturing enterprise's efficiency (the "E"). "Its suite of technologies, hardware, software and services is applied as an all-inclusive solution," said Pete Tecos, 5ME's Executive Vice President for Marketing and Product Strategy. "This is a comprehensive, analytical approach to manufacturing that results in higher productivity, improved quality and lower working capital. We are brand and process agnostic, and therefore able to work with all types of machinery and manufacturing systems. This gives us the independence to render our best solution and work freely with different system suppliers upstream, as well as end users downstream.
"As an independent business, we will be able to offer our cryogenic technology to a larger base of machine tool OEMs and end users in an effort to cast a wider net in our marketing, particularly to the energy, agriculture, construction, aerospace, automotive and medical device industries, where efficient machining of challenging materials - such as titanium, stainless and hardened steel, composites, nickel-based alloys, and nodular or compacted graphite iron (CGI) - is a chronic issue.
"Our eLOG software has made Caterpillar's manufacturing assets - and its production potential - completely transparent in real time to all levels of management, complete with performance metrics. Freedom eLOG's technology is also fully integrated and supported on mobile devices such as smartphones and tablets. The software's initial installation at Caterpillar's Aurora facility produced generous productivity gains on targeted assets. Likewise, our cryogenic machining technology has been instrumental in meeting cost reduction goals for the F-35 Joint Strike Fighter. The benefits of cryogenic machining technology that have already been realized by heavy industry (cycle time reduction and extended tool life) can also be leveraged in other industries, such as medical devices, where additional advantages may emerge due to its inherent residue-free cleanliness.
"Our target customers will be those working with expensive or difficult-to-machine materials, employing a large number of assets, with high costs for consumables and energy, and committed to cultural/organizational change. Our successes to date prove there is vast potential for us to improve the competitiveness of North American manufacturers."
5ME's cryogenic machining process is designed to enable higher cutting speeds for increased material removal and longer tool life by transmitting liquid nitrogen at -321°F through the spindle/turret and tool body, direct to the cutting edge. "In addition, customers will see a significant environmental ROI from the elimination of water-soluble or oil-based coolants," said Tecos. "Energy consumption is reduced due to the elimination of the associated coolant pumps. Furthermore, the cryogenic machining process produces dry chips versus wet, which eliminates the need for centrifuge management systems. Cryogenic technology makes new installations less expensive, reduces energy consumption and provides an improved working environment for worker health and safety."
Among 5ME's core technologies are cryogenic machining, Freedom eWARE Asset Monitoring Software, CYCLO CUT brand tooling, CYCLO COOL brand cutting fluids and Lean/Six Sigma implementation.
For more information contact:
Pete Tecos
Executive VP Marketing and
Product Strategy
5ME
586-202-3285
info@5ME.com
www.5ME.com