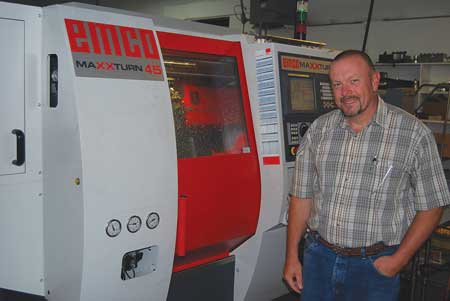
Robert Dubowsky, Owner, ANMOR Machining.
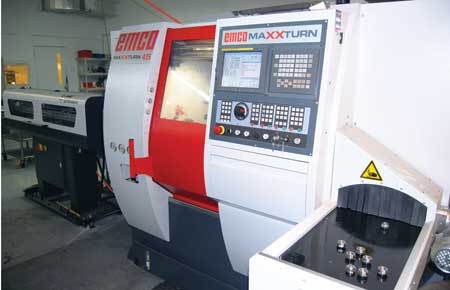
The EMCO Maier MaxxTurn at ANMOR Machining.
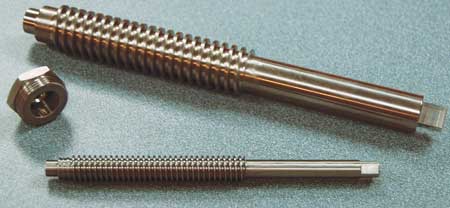
Sample parts include two valve spools, one of which was the first part off the machine.
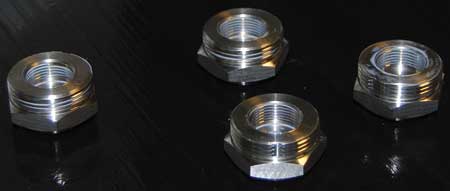
Parts ANMOR produced on the MaxxTurn.
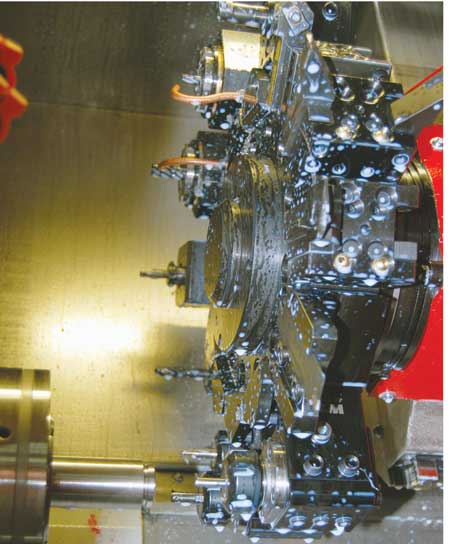
Established in 1984, ANMOR Machining Company in New Britain, CT, has been a stainless steel machine shop primarily for high-end commercial valve components. In 2011, Bob Dubowsky, long experienced in the tool and die business, purchased the company and saw that the same old machining methods were not going to move the firm to the next level of success.
"Our shop is mostly turning with nine lathes plus four machining centers for secondary operations," said Dubowsky. "Parts are tough materials, mostly stainless, Inconel and Hastelloy, from 1/2 inch diameter to 10 inches diameter, and 20 x 30 on the VMC. For our size shop, we have a wide range of capabilities. Over a year, we handle about 150 different part numbers, lot sizes from 10 parts to 3,000 parts with tolerances to +/- 5 tenths and sometimes to 1 tenth."
A MAXXTurn 45 universal lathe from EMCO Maier with 12-position all-live tool turret, subspindle and LNS bar loader, has recently added a new capability to the 10-person shop.
"I looked at several suppliers, but I felt that the MAXXTurn, even though it was higher-priced, would hold tolerances well on our material with very good rigidity," said Dubowsky. "It has the quality of a Swiss machine, but in a larger package. It also offered very good ergonomics for tool change and attention to the collets and chucks and spindles as needed. We are using the FANUC 18 CNC."
Dubowsky learned of the EMCO line from Andrew Creed of Realm Machine Co., who showed him what another large New Britain machine shop was doing with its complement of EMCO turning machines. Bob liked what he saw, and it meant a lot to him that the large shop had invested in and was running a number of EMCO's.
"Even though setups can be a little longer for sub-spindle work, live tools and other features the MAXXTurn offers, it is well worth it on longer runs, reducing cost per part on our longer run jobs," said Dubowsky. "Since a lot of our parts are suitable for live tools and backworking, I wanted to take a look at this type machine."
"A high performance CNC lathe, the MAXXTURN 45 is an ideal solution for economic complete machining from bar or blanks," said an EMCO Maier spokesperson. "It has just the right features to guarantee significant increases in productivity. Highly dynamic drive systems help to achieve this plus it offers the required precision and rigidity for the production of complex turned and milled parts.
"The high power of the 13 kW, 6,300 RPM spindle drive combined with optimal torque curve ensures economic efficiency in cutting steel, as well as high-speed cutting of aluminum. The main spindle provides a bar capacity of up to 45 mm and is supported with extra large precision bearings. These allow for a wide range of speeds with good running precision. A symmetrical headstock with fitted cooling fins helps ensure optimum thermo stability."
"A lot of the parts we do have been multiple operations, which is why I looked for the capabilities the EMCO has," said Dubowsky. "I spent many years in the Swiss machining industry, so when I first bought the company I recognized the potential benefit of a multi-tasking lathe, which would allow us to drop parts complete rather than through three machines - especially longer run parts.
"Previously, a stainless nut for the pump industry had been set up in three machines, including two lathes for a total of nine operations. The machining cycle is similar with the EMCO, but the part is done complete in one setup, eliminating handling and saving at least 10 minutes per part. Plus, the operator can attend to other tasks while the EMCO shapes the parts.
"The EMCO has also allowed us to open up capacity. Instead of tying up three machines, we drop the part complete on the EMCO and then have the three others to take on other work. At times, our backlog has been extended, but now we can reduce that time and keep our customers happier."
One of the leading features of the entire MAXXTURN line is the Y-axis integrated in the body of the machine. This is intended to ensure maximum stability and precision. The wide distances between the guides provide stable turning and offer the operator additional possibilities for complete machining.
The compact sub spindle permits reverse side machining and the potential to drop parts complete in one handling. This avoids the need to clamp workpieces a second time.
The 12-station tool turret with single motor engineering offers space for live VDI25 tool holders in each position. A servo motor powers the driven tools and the swivel movement. The turret can be used on both spindles and switches with direction logic. This means that it always takes the shortest way when swiveling to the next tool. The tool holders, equipped with EMCO joggling plates, allow easy tool insertion with repeatable accuracy without the need for time-consuming adjustments, according to the company.
The machine is working out so well, Dubowsky is thinking about adding another later this year.
"I also cannot say enough about the techs," said Dubowsky. "They were very professional, very knowledgeable and showed my guys how to make things go better to get the most out of the machines. I would put EMCO among the best I have ever worked with in terms of knowledge and speed of work - and I have worked with a lot machine tool builders over the years."
Outlook for business has been pretty steady over the last couple of years at ANMOR, and from what Dubowsky hears from his customers in aerospace and direct government work, he does not see that changing. "With the support of EMCO Maier, I am confident in our ability to handle the work," he said.
For more information contact:
EMCO Maier Corporation
46850 Magellan Drive
Unit 160
Novi, MI 48377-2448
248-313-2700
www.emcomaier-usa.com
www.emco-world.com
NORTHEAST ONLY
Andrew Creed
Realm Machine
12 Crossroads Plaza
P.O. Box 370554
West Hartford, CT 06137
800-625-8559
acreed@realmachine.com