
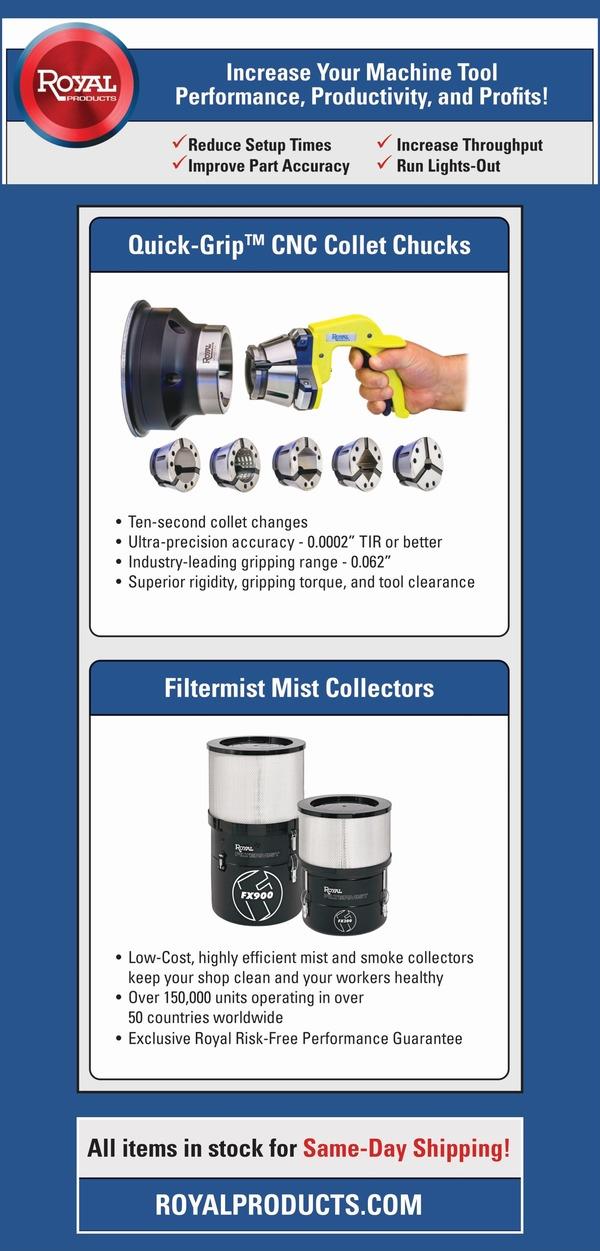
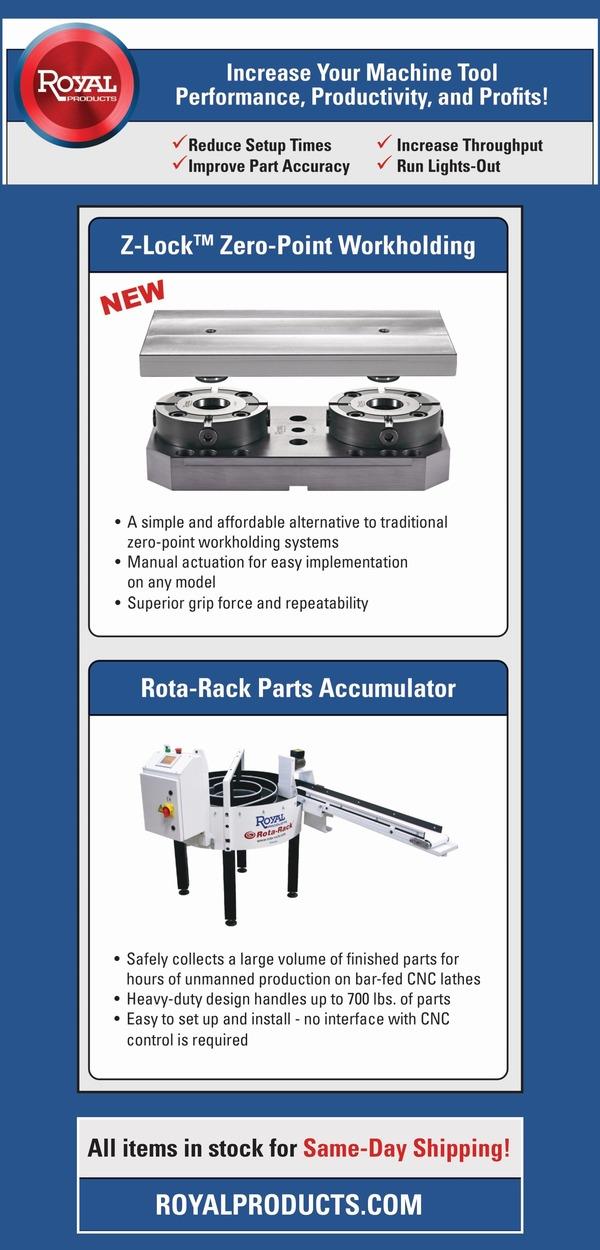

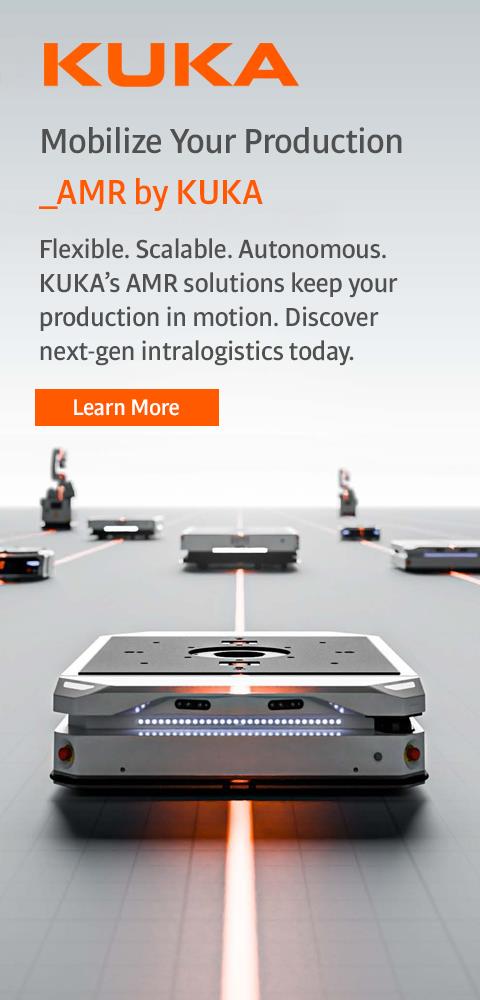
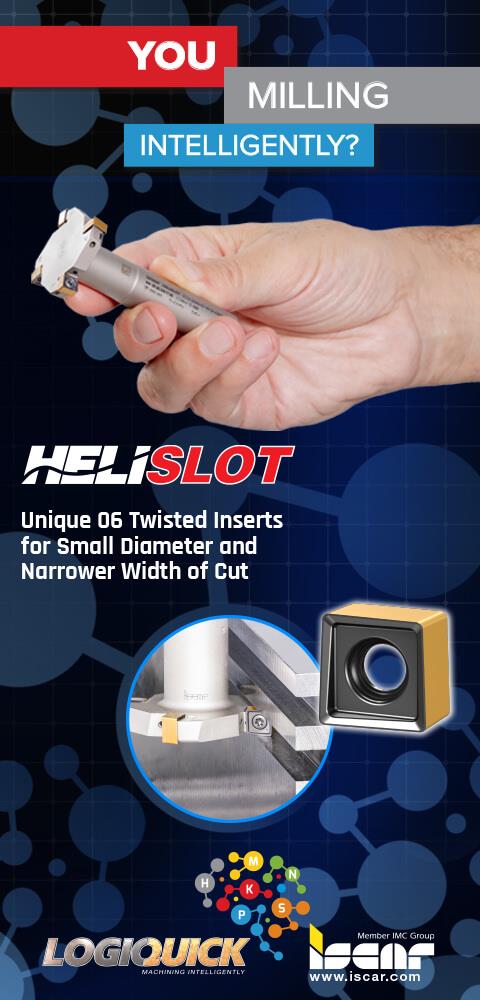
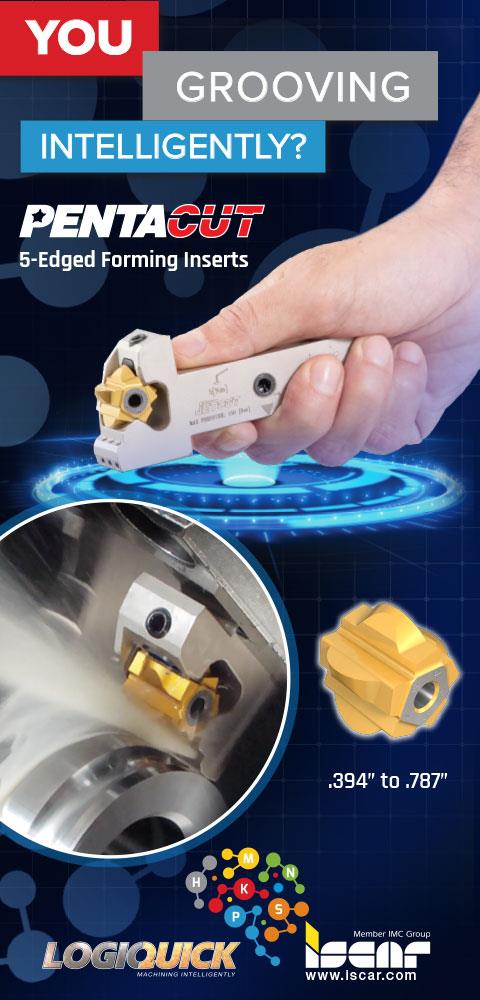
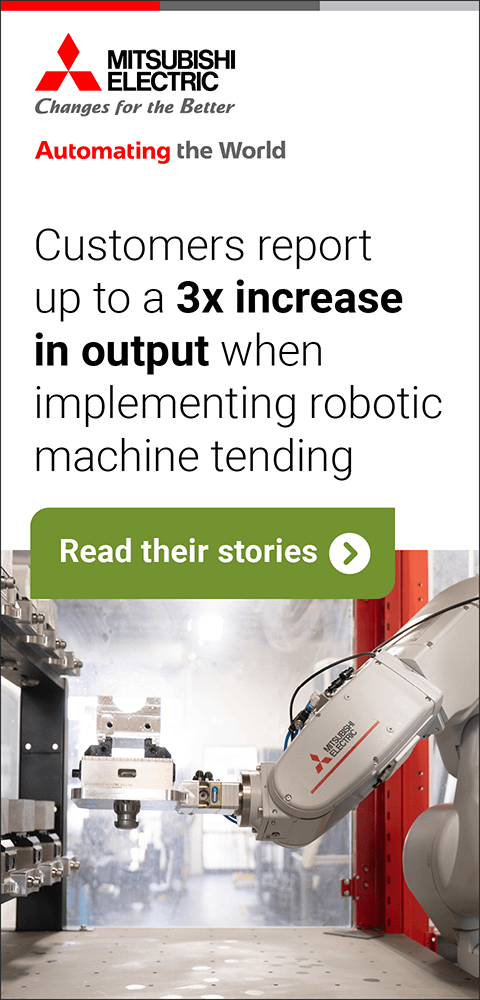
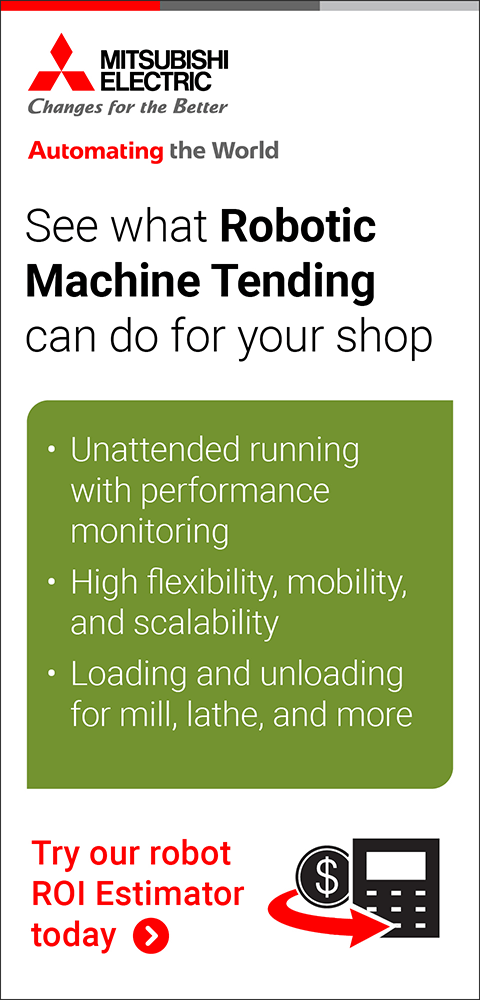
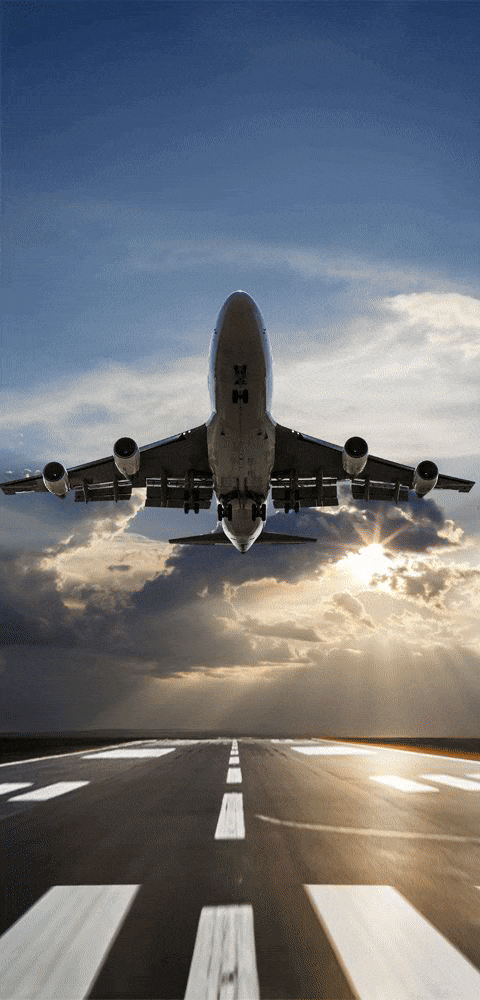
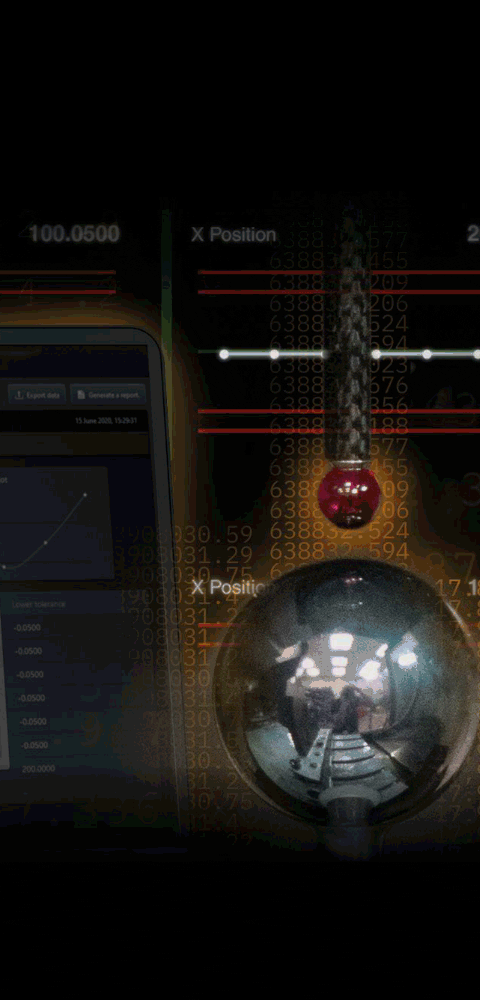
Collaborative Welding System with Auto Deltaweld
September 1, 2024
Miller Electric Mfg. LLC has announced that the Copilot collaborative robotic welding system now features the new Auto Deltaweld as its welding power source. The Auto Deltaweld is currently featured on the air-cooled Copilot and will soon be offered on the water-cooled version.
With the integration of Auto Deltaweld, the Copilot system provides advanced features with a headless power source design that focuses user interface on the machine's teach pendant-ultimately making the Copilot intuitive and accessible to welders of all skill levels. The incorporation of the Auto Deltaweld as the power source also means that its input power flexibility accommodates single-phase and three-phase input. Lastly, the Modbus TCP communications protocol eliminates extra hardware and code between the Auto Deltaweld power source and cobot arm controller, which further mitigates software bugs and the need to troubleshoot errors.
"Miller introduced the Copilot collaborative welding system to help operations increase weld quality and consistency, minimize downtime and further productivity," said a company spokesperson. "In short, it helps to empower welders to amplify their skillsets-making it easy for shops to wade into welding automation for the first time. Because welders can learn to operate the Copilot in a matter of hours or even minutes, it is possible to increase outputs nearly immediately, generating ROI on the machine while adding to an operation's bottom line."
Features of the Copilot include:
- AccuGuide positioning control: The precision joystick helps fine-tune the position of the torch during programming.
- IntelliSet weld settings assistant: An intuitive interface that recommends weld settings based on material, process and joint type, allowing operators to build programs with confidence for repeatable, high-quality welds
- Advanced capabilities: Operators can load and unload from a single station that can be shared with the robot envelope, making it suited for users across all skill levels. It is also effective for addressing challenges often faced by high-mix, low-volume operations-allowing companies to accelerate training and enhance productivity to meet deadlines.
For more information contact:
Miller Electric Mfg. Co.
An ITW Welding Company
1635 W Spencer St.
P.O. Box 1079
Appleton, WI 54912
920-734-9821
info@millerwelds.com
www.millerwelds.com/products/copilot-cobot
< back