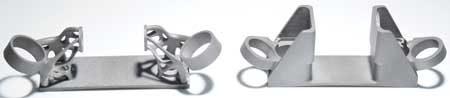
A comparison of the AM-designed bracket (left) and the traditional version (right).
The Additive Manufacturer Green Trade Association (AMGTA), a global advocacy group focused on developing and promoting sustainable additive manufacturing (AM) industry practices, has published an independent piece of research titled "Comparative LCA of a Low-Pressure Turbine (LPT) Bracket by Two Manufacturing Methods."
The report, commissioned by the AMGTA and authored by the Rochester Institute of Technology's Golisano Institute of Sustainability, analyzed a commercial aerospace low-pressure turbine bracket via a life cycle assessment (LCA), evaluating both (i) the comparative manufacturing impact of laser powder bed fusion (LPBF) AM vs. traditional manufacturing of the bracket, and (ii) the impact of a greater than 50% weight reduction of the bracket over the life of the aircraft. While the comparative end result was inconclusive with regard to which manufacturing method used more energy, the results confirmed the dramatic impact that lightweighting commercial aircraft engines and airframes have on carbon emissions.
Key takeaways from the LCA included the following points:
- Inconclusive on Manufacturing Method: Using three separate methodologies, the LCA was inconclusive as to which manufacturing method (traditional or additive) used more energy. On balance, this neutral finding represented an improvement over previous studies showing higher energy used in LPBF manufacturing compared to traditional methods.
- Importance of Energy Mix: The study found that the biggest factor in determining sustainability of production was a manufacturing facility's energy mix at the location of generation, and whether that energy grid was produced using sustainable means.
- Outsized Impact on Lightweighting Aircraft: The study showed that lightweighting aircraft components via AM design resulted in a reduction in carbon emissions over the life of an aircraft, with a reduction of 13,376 kg for every 1 kg of weight reduction.
- Overall, AM Produced a More Sustainable Part: The impact of lightweighting was the most important factor in determining that AM-produced components are more sustainable than a traditionally designed and manufactured part.
"The release of this peer-reviewed LCA-the first of its kind-represents a milestone for the AMGTA," said Sherri Monroe, the AMGTA's Executive Director. "For the first time, we are able to publish tangible results demonstrating the importance of design in AM when compared to traditional methods. This study demonstrates the very real impact that AM can have in aircraft and engine design of the future and bodes well for using similar strategies in other industries and programs."
The two-year study analyzed the two brackets using three LCA methodologies, including the ReCiPe 2016 version 1.1 midpoint method, the Cumulative Energy Demand v1.11, and the Intergovernmental Panel on Climate Change's IPCC 2021 GWP100 methods. Two of the three methods indicated that, strictly from a manufacturing standpoint, the traditional bracket required less energy to produce, while one method indicated that the AM version produced less carbon dioxide. In all cases, however, the results indicated that the energy mix of the underlying electrical grid had an outsized effect on the sustainability of the manufacturing process. The LCA was performed in accordance with ISO 14040:2006(E) and was peer-reviewed by EarthShift Global.
The underlying bracket, which is one of 12 on each of the two GE Aviation CF6-80C2B6F turbine engines powering a Boeing 767 aircraft, secures a fuel manifold to the external case of the engine's low pressure turbine module. It was selected by the AMGTA because it was a relatively simple part that is easy to access and locate. The additive design and manufacturing of the bracket was performed by Sintavia, LLC in Hollywood, FL, and printed on an EOS GmbH M290 printer using Höganäs AB Inconel 718 powder. The traditional part was manufactured by a Tennessee-based machine shop using a CNC process. The optimized AM bracket was over 50%, or 0.063 kg, lighter than the original version. According to Sintavia, the optimized bracket outperformed the traditional bracket in terms of mechanical properties, with an increased fatigue life in spite of its reduced weight.
While the choice of the LPT bracket offered a simple demonstration of how lightweighting could work on an aircraft engine, the AMGTA believes that the lessons embodied in the current LCA could be more widely adopted by airframers and engine manufacturers across multiple mechanical systems. Moreover, lightweighting methods of transportation using additive design technology is not only limited to LPBF AM, as other additive technologies (including binder jetting, directed energy deposition and polymer printing) can similarly remove excess weight across vehicles, aircraft and vessels.
"This study underscores the importance of using AM to develop optimized parts and components that have been lightweighted via AM technology," said Brian Neff, Sintavia's CEO and the Chair of the AMGTA. "No other currently viable commercial technology offers such an immediate impact to carbon emissions as lightweighting aircraft parts via AM does, and we now have independently verified, peer-reviewed data proving so. We look forward to working with Boeing, GE and all of the industry's OEMs as they look to unleash the sustainable potential of AM across existing and future platforms."
For more information contact:
AMGTA
954-308-0888
info@amgta.org
www.amgta.org