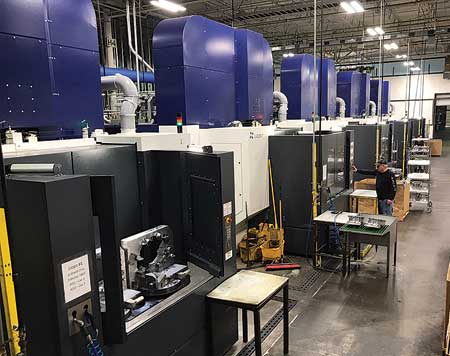
Five highly flexible twin-spindle machining centers from LiCON MT are essential for the production of electric motor housings at Trace Die Cast.
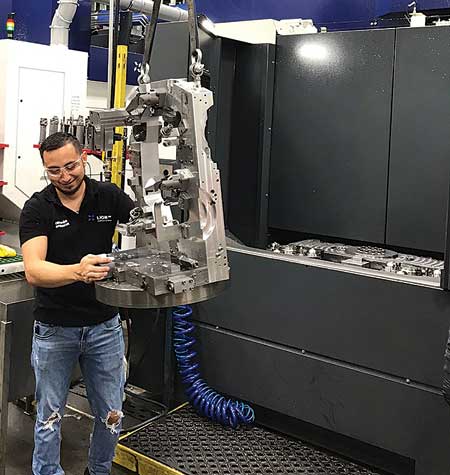
A Trace Die Cast employee during a set-up process.
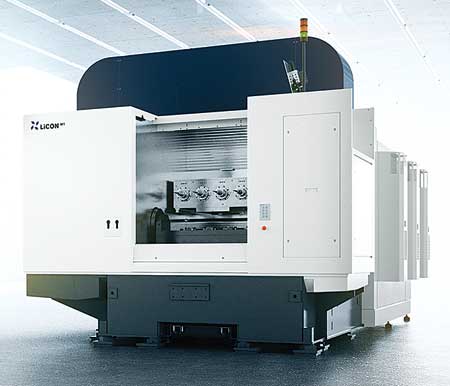
The LiFLEX IV 244 four-spindle machine is suited for the automotive industry due to its high production and precision capabilities.
U.S. specialist for cast components Trace Die Cast recently took on a challenge to produce high-precision cast parts for electric drive housings. The company has been able to meet time constraints and other obstacles with the implementation of five flexible, 5-axis twin-spindle machining centers, type LiFLEX II 766 i3 and has plans to add another.
Electric mobility has been booming around the world for some time. Recently, a major American electric vehicle manufacturer saw the demand and decided to place a new vehicle model in the expanding market through a project with a very challenging time frame. Just one year was estimated from the start of production until regular production levels would be reached with the maximum output capacity. It was a more than ambitious timeline.
For unknown reasons, the original cast parts supplier left the project suddenly, an unexpected development for everyone involved. The moment had come for Trace Die Cast to step in. Managers needed to quickly meet the high requirements for precision and speed. They got in touch with the American branch of LiCON MT in Dexter, MI, and initiated the project.
In the German town of Laupheim, LiCON MT managers realized that, although these technological requirements matched up with LiCON MT's core expertise, this order would pose some challenges.
In particular, the production of motor housings, which is the heart of every electric vehicle, requires the highest level of precision. This precision has a direct impact on the ability of e-drives to run smoothly, and therefore affects the everyday operation of the vehicle.
"LiCON MT produces highly flexible, high-speed machining centers, but it was a unique challenge to produce a solution in such an extremely rapid timeline," said Managing Director Winfried Benz.
After a short project planning phase, build of the first two machines began. LiCON MT has the ability to configure machining centers quickly from mainly standardized assemblies in the modular LiFLEX toolbox. Only when the workpiece itself is introduced are individual customer requests and component requirements addressed. This accelerates the throughput time of the machine build, resulting in shorter delivery times.
Workpieces at Trace Die Cast are processed via a highly individualized process. The example of electric motor housings illustrates this.
A total of three different components are produced on the machines delivered to Trace Die Cast. These are the left and right halves as well as the center part of the electric motor housing. The machines maintain a positioning precision of 35 micron, which is achieved in volume operation without the use of measuring probes. The flexible machining centers achieve 50 micron in concentricity of opposing bores. Taking into account a 1.67 Cmk requirement, position accuracy goes further-to less than 20 microns-seen over the whole production day.
Such high levels of precision can be achieved only through specialized temperature compensation. The i3 series uses a large number of sensors in the relevant machine locations to measure the current temperatures and compensate for fluctuations via developed algorithms. "Without this perfect combination of hardware and software, this kind of precision in production processes would be impossible in large scale production," said a spokesperson.
Another technological highlight is dynamic tool monitoring. "In comparison to conventional machines, LiFLEX series machining centers offer significant added value over other systems," said the spokesperson. "Detecting broken or worn tools reliably is considered state-of-the-art in modern systems. The development engineers in Germany were not satisfied with that standard, however, and continued their research. Through making consistent improvements to monitoring systems, now they are even able to avoid errors when clamping workpieces and exclude collisions with the clamping devices fully in advance. The highly sensitive systems can also reliably detect indications of casting errors, such as blowholes or inclusions of other materials. They do so by interpreting the power consumption through an intelligent process, directly in the motor spindle drive. The motor spindles, which are equipped with numerous other technical features, are developed, produced and maintained at the in-house spindle center."
According to Chris Guthrie, President of Trace Die Cast, "The speed at which projects could be carried out, and the extremely high level of production efficiency offered by the machines, were the decisive factors for us."
Trace Die Cast was founded in 1988 by Lowell Guthrie. Guthrie had previously worked for the Ford Motor Company in Alabama for almost 25 years. After Ford closed its North American die casting plant in Alabama, he founded Trace Die Cast with two die-casting machines. In 2016, his four sons Chris, Kent, Brett and Greg Guthrie took over the growing company and have continued to expand it. Trace Die Cast now has over 40 die-casting machines, with closing forces between 840 tons and 2,200 tons. Over 70 CNC processing centers are in use for processing high-precision components. The company's products, which include valve bodies, torque converter housings, extension housings, transfer cases and end covers, are primarily used in the powertrains of major automotive manufacturers such as Ford, General Motors, Borg Warner Automotive, Allison Transmission and others.
For more information contact:
Trace Die Cast
140 Graham Ave.
Bowling Green, KY 42101
270-781-0049
www.tracediecast.com
LiCON MT LP
2135 Bishop Circle Drive East
Unit 1
Dexter, MI 48130
734-426-2240
info@licon.com
www.licon.com