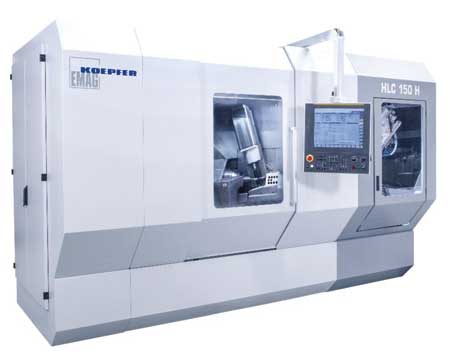
The HLC 150 H gear hobbing machine from EMAG helps ensure high surface quality on components with a maximum length of 500 mm and a weight of 10 kg.
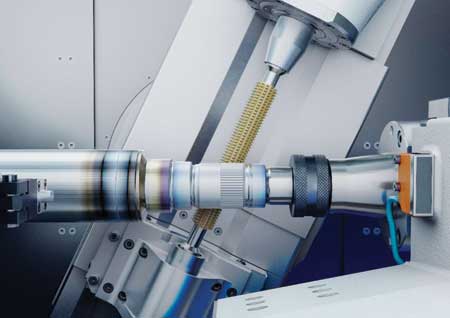
High motor speeds on the milling head and main spindle enable high cutting speeds.
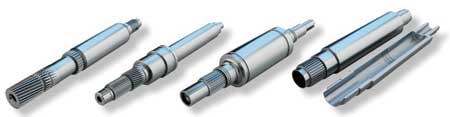
With the HLC 150 H and the K 160, EMAG offers a wide range of gear solutions for rotor shafts.
Machining the teeth of a rotor shaft for electric cars has demanding machining requirements. Very few other applications place such high demands as transmission components. The quiet motor requires the highest surface finishes so that disturbing running noises do not occur. In addition, the number of units in e-mobility is greatly increasing, which is an additional challenge for the mechanical engineering involved. What is needed, therefore, are process-reliable solutions for cost-effective rotor shaft production. The EMAG Koepfer HLC 150 H gear hobbing machine demonstrates how this can work, offering new productivity in this gear sector.
The fact that electric cars do not have any transmissions (apart from the sometimes-indispensable differential) is just a legend-but one that persists quite stubbornly in the public eye. It assumes that the electric motor does not require any gear ratio given its stable torque. In practice, however, it is usually the case that a one-speed gearbox is used, which helps reduce the speed of the electric motor by a certain factor. As a result, there are numerous gearing elements on components such as the drive shaft, rotor shaft or axle drive, and their component quality must be exceptional so that, for example, there are no loud running noises-these would be audible given the quiet electric motor.
In this context, the technology of EMAG is grabbing the attention of production planners. For many years, the specialists have been developing highly versatile mechanical engineering solutions for machining a huge range of workpieces, from gear shafts to steering pinions and worm gears to planetary gears-an ideal experience base for providing efficient solutions for the gear cutting of rotor shafts as well. The HLC 150 H gear hobbing machine is one of the focal points here, offering a high level of productivity for components with a maximum length of 500 mm and a weight of 10 kg.
The milling head is rigidly suspended and moves completely during machining. The shift axis is made up of the interpolation of two axes. In this way, a large milling head swiveling angle is realized with a large shift path at the same time. As a result, gear hobbing is smooth and the gear quality is high. The horizontal arrangement of the workpiece also prevents chip clusters from forming. In the end, this technology helps ensure large performance figures in the machining of rotor shafts with cycle times of only 35 seconds at a gear quality of DIN Q7.
On this basis, the machine builders plan and develop complete lines for the rotor shaft in which all machining processes are linked one after the other-from the soft machining of the blanks to the final hard machining, including the tooth flank grinding processes or skiving hobbing. The HLC 150 H is also used here, which is no problem in view of its integrated high-speed gantry loader. It picks up the components from EMAG's own TrackMotion system, which in a sense drives through the machines on the line.
Incidentally, EMAG has the K 160 gear hobbing machine-a solution for components with a maximum length of 300 mm and a weight of 2.5 kg, which is particularly interesting for assembled rotor shafts, because their individual parts are relatively small and light (before joining). At the same time, this machine can also be integrated into EMAG lines or largely automated. In any case, the high vibration damping ensures long tool life and high surface finishes. Maximum motor speeds at the milling head and main spindle result in high cutting speeds even for shafts with small numbers of teeth.
Authored by EMAG
For more information contact:
EMAG L.L.C.
38800 Grand River Ave.
Farmington Hills, MI 48335
248-447-7440
info@usa.emag.com
www.emag.com