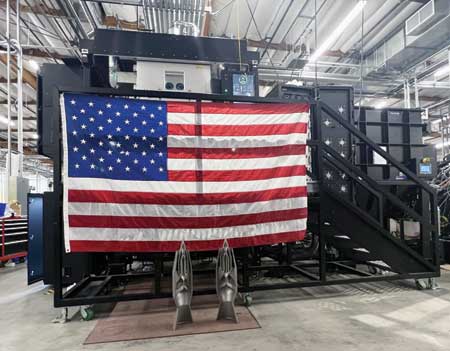
A large-format Sapphire XC in Velo3D's Lakeview, CA, manufacturing facility. BPMI has chosen a Sapphire XC to be operated by ATI in a new Florida facility that supports the U.S. Navy.
Velo3D, Inc. announced that Bechtel Plant Machinery Inc. (BPMI) has selected a fully integrated metal additive manufacturing (AM) solution from the company to produce parts for the U.S. Naval Nuclear Propulsion Program. The Sapphire XC large format printer, calibrated for stainless steel 415, will be operated by ATI at its new AM facility outside Fort Lauderdale, FL. Earlier this year, BPMI awarded a contract to ATI to support development of highly engineered part solutions for advanced manufacturing methods including metal AM. The partners will use the printer to produce parts previously produced through casting, reducing lead times for mission critical parts and streamlining their supply chain.
"Conventional 3D printers often struggle to produce parts with overhanging features beyond 45° without support structures," said a company spokesperson. "However, Velo3D's proprietary technology offers the ability to produce parts with a wide variety of geometries with few-to-no supports. This has allowed the company to address applications that other 3D printing technologies cannot. In addition to using this technology to 3D print parts that are traditionally cast, Velo3D's technology also enables more innovative designs to replace components currently in use. Furthermore, this capability can be scaled to additional machines across multiple locations and operators."
"BPMI and ATI's progressive approach to 3D printing is extremely forward-thinking, and this new, revolutionary facility will significantly augment the U.S. Navy's supply chain for maintenance, repair and operations," said Brad Kreger, CEO at Velo3D. "Both companies are early adopters of metal 3D printing and innovators in the manufacturing industry. We look forward to working with them as they support the U.S. Navy's fleet, including its aging vessels."
The U.S. Navy currently operates approximately 300 vessels, many of which were commissioned decades ago. They, along with the broader U.S. Department of Defense, have actively incorporated AM, acknowledging its efficiency in supporting its aging equipment, enhancing warfighter readiness and reducing replacement part lead times. AM accomplishes this by enabling distributed supply chains and digital inventories where manufacturers can produce parts within spec across any similar printer calibrated for the same metal alloy. ATI's new secure facility, along with Velo3D's fully integrated solution, are significant steps forward in advancing the Navy's maintenance and operational capabilities.
"Printers with larger build volumes and the ability to print with less support structures are ideal for U.S. Naval Nuclear Propulsion Program applications," said Nathan Weiderspahn, BPMI Executive Manager, Industrial Base Management. "This AM technology will greatly support our efforts in delivering new technology to the U.S. Navy and helping maintain its fleet of ships."
"ATI will be able to more easily additively produce complex parts with fewer support structures, at lower angles and larger sizes than ever before," said Joe Thompson, General Manager of ATI Additive Manufacturing Products. "This enables us to broaden the scope of possible part designs for our defense and aerospace customers, enabling higher performance and better quality. The business opportunity represented by these previously unproduceable part designs is significant."
BPMI's new Sapphire XC printer is the first such printer from Velo3D calibrated for stainless steel 415, an alloy of iron, chromium and nickel that provides good tensile strength and corrosion resistance at a range of temperatures.
For more information contact:
Velo3D
2710 Lakeview Court
Fremont, CA 94538
408-610-3915
info@velo3d.com
www.velo3d.com
ATI
www.atimaterials.com
BPMI
www.bpmionline.com